High-performance plastics are advanced materials with exceptional mechanical, thermal, and chemical properties, making them ideal for demanding applications across various industries. These plastics exhibit superior strength, durability, heat resistance, and dimensional stability compared to traditional plastics. They offer excellent resistance to chemicals, abrasion, impact, and wear, allowing them to withstand harsh operating conditions.
When selecting a high-performance plastic for a specific application, it is crucial to consider several factors. The right choice ensures optimal performance, longevity, and cost-effectiveness. Factors to consider include the required mechanical properties, temperature range, chemical compatibility, electrical insulation, flame resistance, and regulatory compliance. Additionally, considering factors like manufacturing processes, cost, and sustainability helps in selecting the most suitable high-performance plastic for the application, maximizing performance and achieving desired outcomes.
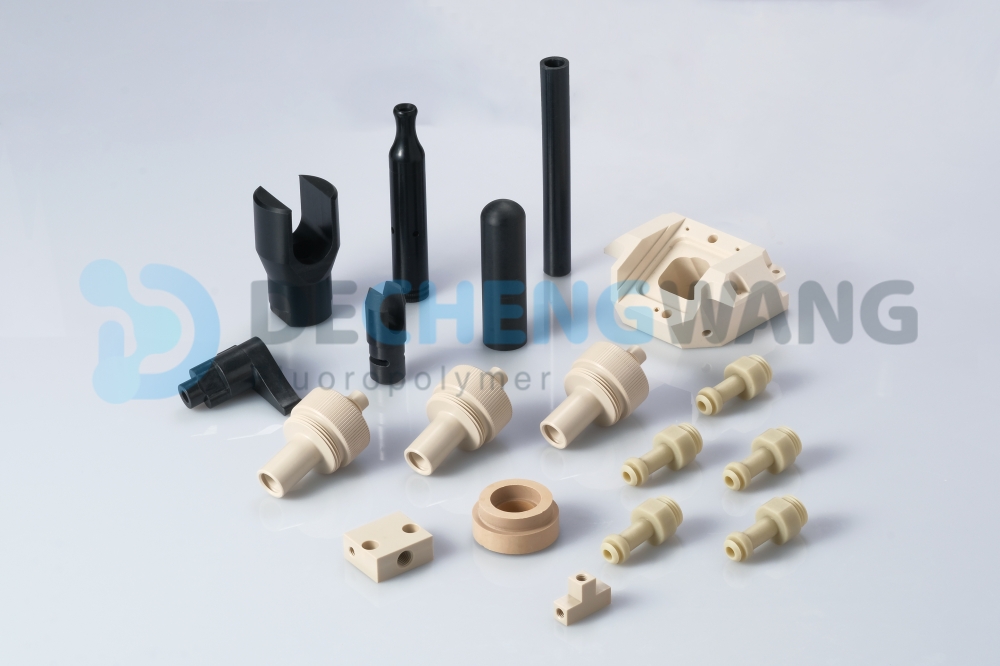
Definition of high performance plastic
High-performance plastics are highly regarded for their exceptional properties that enable them to excel in extreme environments. These plastics are specifically characterized by their ability to withstand and thrive in challenging conditions, including extreme temperatures, high pressure, high velocity, and more.
When looking at the plastics pyramid, the top two tiers are considered high-performance materials. They are extensively chosen for a wide range of applications, such as aerospace and aircraft industries, deep downhole drilling operations, medical device manufacturing, food processing, glass production, and numerous other fields. These plastics play a vital role in enabling the development of products that can endure demanding circumstances while maintaining optimal performance and reliability.
Despite their potentially higher cost, high-performance materials are frequently chosen by end users due to the favorable balance they offer between cost and performance.
These materials provide an excellent combination of performance, durability, and versatility, making them a cost-effective solution for applications where metal parts may be traditionally used.
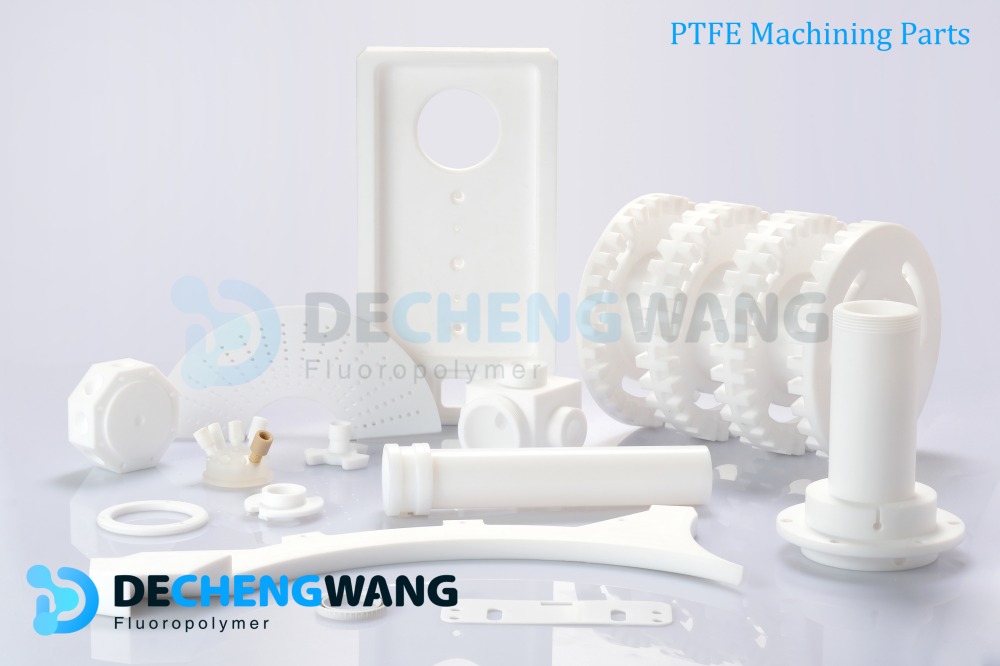
Key benefit of high performance plastic
High-performance plastics are aptly named due to the exceptional level of performance they provide compared to traditional plastics. These materials exhibit a range of advantageous properties that set them apart.
Superior mechanical strength and durability
First and foremost, high-performance plastics offer superior mechanical strength and durability. They can withstand heavy loads, resist deformation, and maintain their structural integrity even under extreme conditions. This makes them highly suitable for applications that require components with high strength-to-weight ratios or those subjected to intense stress or impact.
HIGH TEMPERATURE RESISTANCE
Additionally, high-performance plastics excel in temperature resistance. They can withstand both very high and very low temperatures without experiencing degradation or loss of mechanical properties. This characteristic makes them valuable in applications that involve extreme heat or cryogenic environments, such as aerospace, automotive, and electronic industries. The whole families of high performance plastics can be used at permanent service temperatures of more than 302°F up to over 572°F depending on the operating conditions.
Chemical resistance
Chemical resistance is another key aspect of high-performance plastics. They exhibit excellent resistance to a wide range of chemicals, including acids, solvents, and corrosive substances. This property ensures the longevity and reliability of components used in industries like chemical processing, oil and gas, and pharmaceuticals.
Electrical insulation
High-performance plastics also possess exceptional electrical insulation properties. They can effectively resist the flow of electricity, making them invaluable in applications that require electrical insulation, such as electronic components and wiring systems.
Wear resistance
Furthermore, these plastics offer low friction and excellent wear resistance. This makes them suitable for applications involving sliding or rotating parts, reducing frictional losses, and extending the lifespan of components.
Overall, these high-performance plastics offer the highest levels of structural strength at elevated temperatures, the ability to withstand the broadest spectrum of aggressive chemicals, and exceptional resistance to wear and creep from high dynamic and static loads and stresses. Noteworthy properties of these high-performance plastics also include toughness at low temperature extremes, impressive resistance to radiation exposure, low thermal expansion and excellent flammability ratings and outstanding electrical and thermal insulative properties.
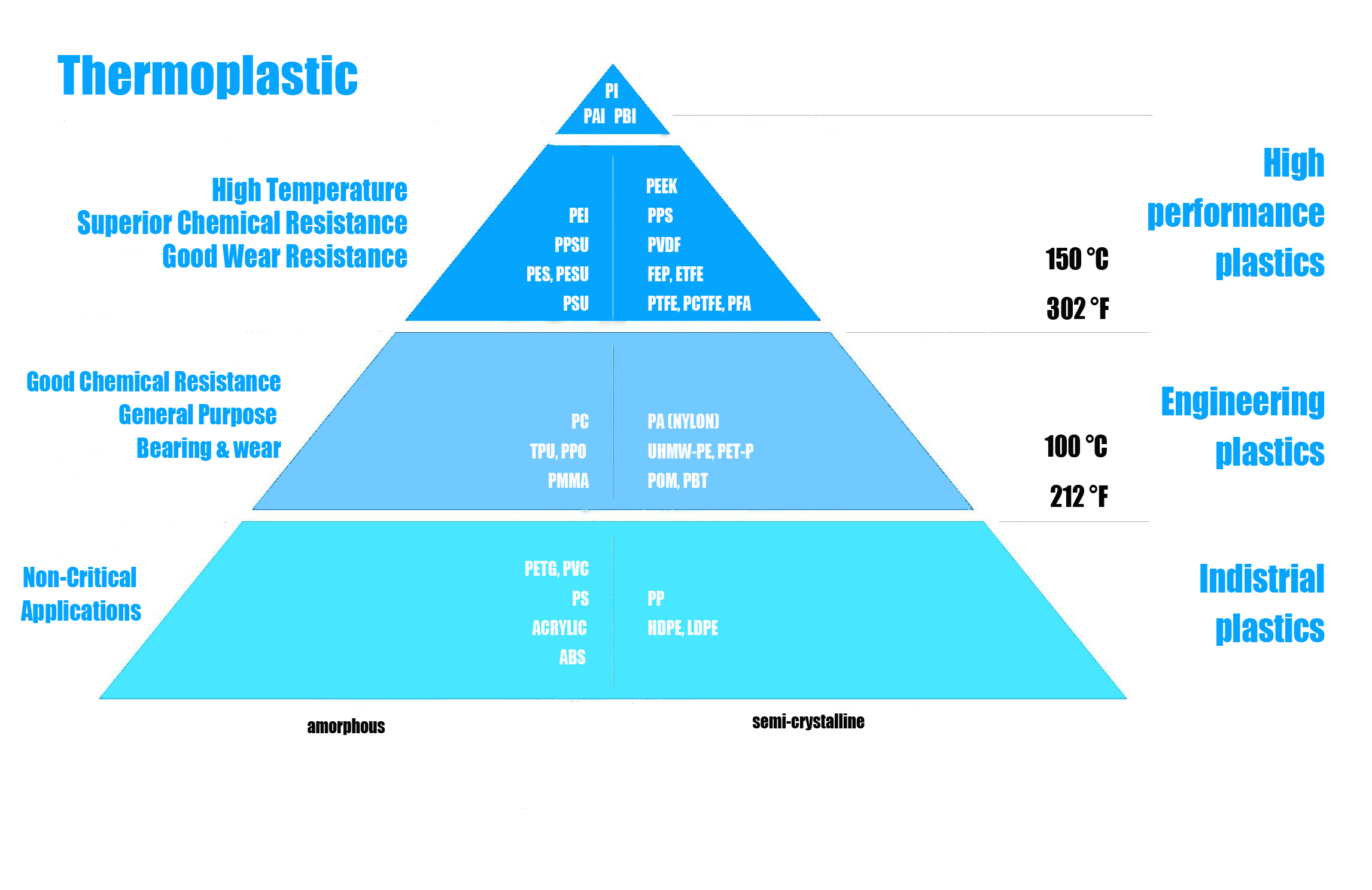
Types of high-performance plastic material
High-performance plastics include: PTFE, PCTFE, PFA, FEP, ETFE, PVDF, PEEK, PPS, PI, PAI, PBI, PSU, PES, PPSU,, PEI and etc.
PTFE (Polytetrafluoroethylene)
Description: PTFE is a fluoropolymer known for its excellent chemical resistance, low friction, and high-temperature stability.
Performance advantages: Outstanding non-stick properties, electrical insulation, and low coefficient of friction. Resistant to heat, chemicals, and weathering.
Applications: It is widely used as electrical insulation, gaskets, seals, bearings, and in the chemical processing industry.
Main manufacturers: Chemours (Teflon PTFE), Daikin (Polyflon PTFE), 3M (Dyneon), Dongyue, and etc.
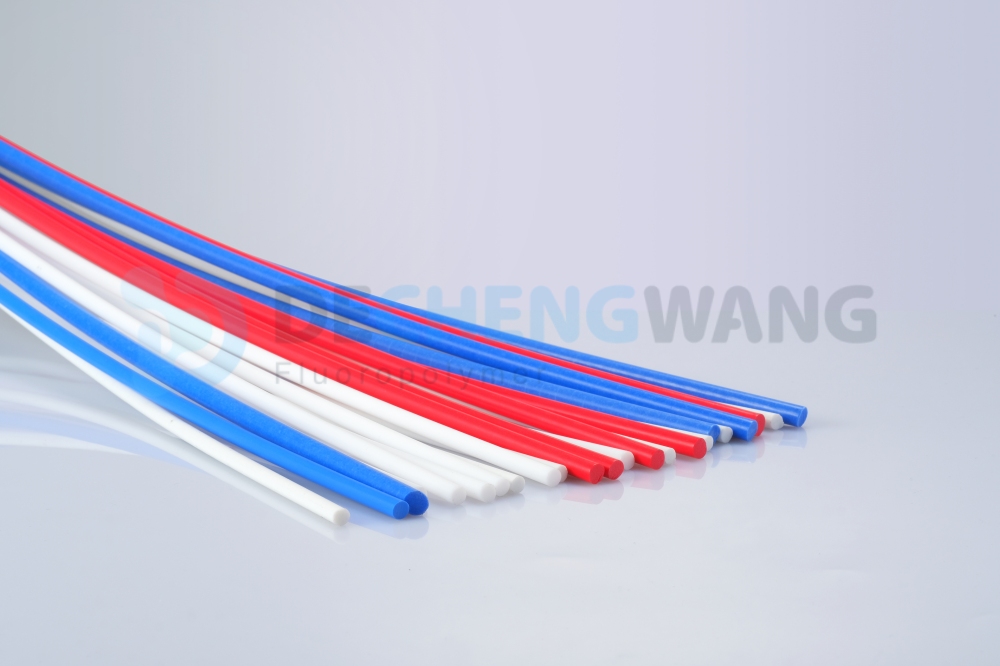
PCTFE (Polychlorotrifluoroethylene)
Description: PCTFE is a highly crystalline thermoplastic known for its exceptional chemical resistance and dimensional stability.
Performance advantages: Excellent barrier properties, high resistance to chemicals and solvents, low moisture absorption, and excellent electrical insulation.
Applications: It is commonly used in aerospace, cryogenic applications, valves, pumps, seals, and electrical connectors.
Main manufacturers: Daikin (Neoflon PCTFE).
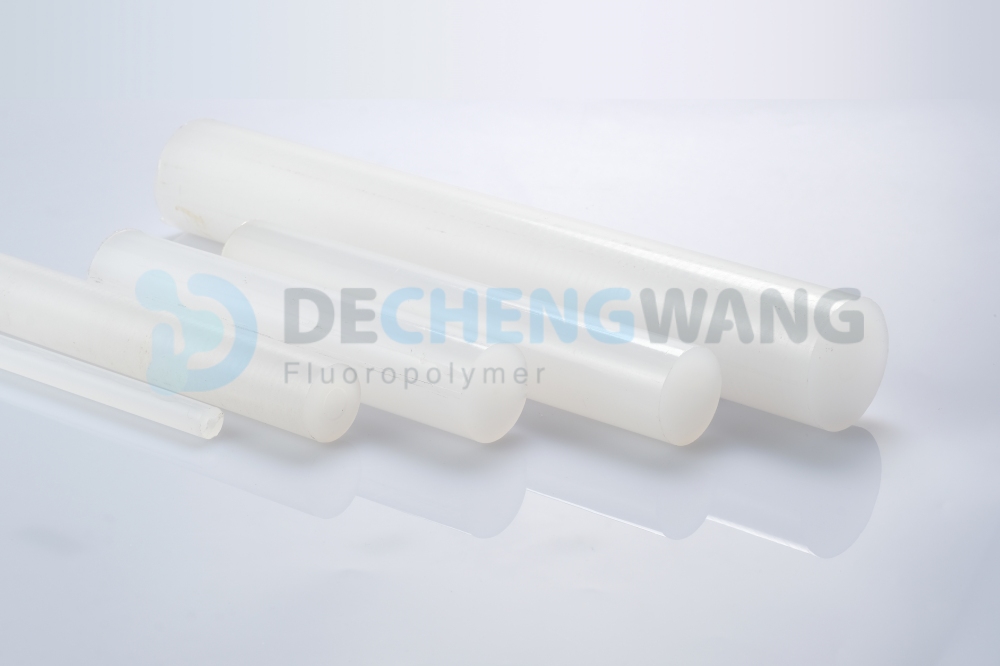
PFA (Perfluoro Alkoxy)
Description: PFA is a melt-processable fluoropolymer with similar properties to PTFE but with improved processability.
Performance advantages: High-temperature resistance, excellent chemical resistance, low friction, and good electrical insulation.
Applications: It is commonly used in the semiconductor industry, chemical processing equipment, wire and cable insulation, and medical devices.
Main manufacturers: Chemours (Teflon PFA), Daikin (Neoflon PFA), AGC (Fluon PFA) and etc.
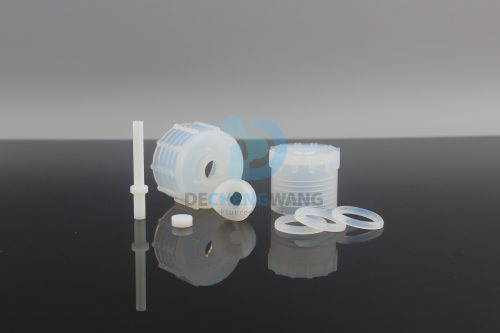
FEP (Fluorinated Ethylene Propylene)
Description: FEP is a transparent, melt-processable fluoropolymer with excellent electrical properties and chemical resistance.
Performance advantages: Outstanding non-stick properties, good electrical insulation, low friction, and excellent chemical resistance.
Applications: It is widely used in wire and cable insulation, semiconductor manufacturing, chemical process equipment, and medical tubing.
Main manufacturers: Daikin (Neoflon FEP), Chemours (Teflon FEP) and etc.
ETFE (Ethylene Tetrafluoroethylene)
Description: ETFE is a highly transparent, lightweight fluoropolymer known for its exceptional weather resistance and electrical properties.
Performance advantages: Excellent chemical resistance, high dielectric strength, UV resistance, and high-temperature stability.
Applications: It is commonly used in architectural membranes, wire insulation, solar panels, and corrosion-resistant coatings.
Main manufacturers: AGC (Fluon ETFE), Daikin (Neoflon ETFE), Chemours (Tefzel ETFE), and etc.
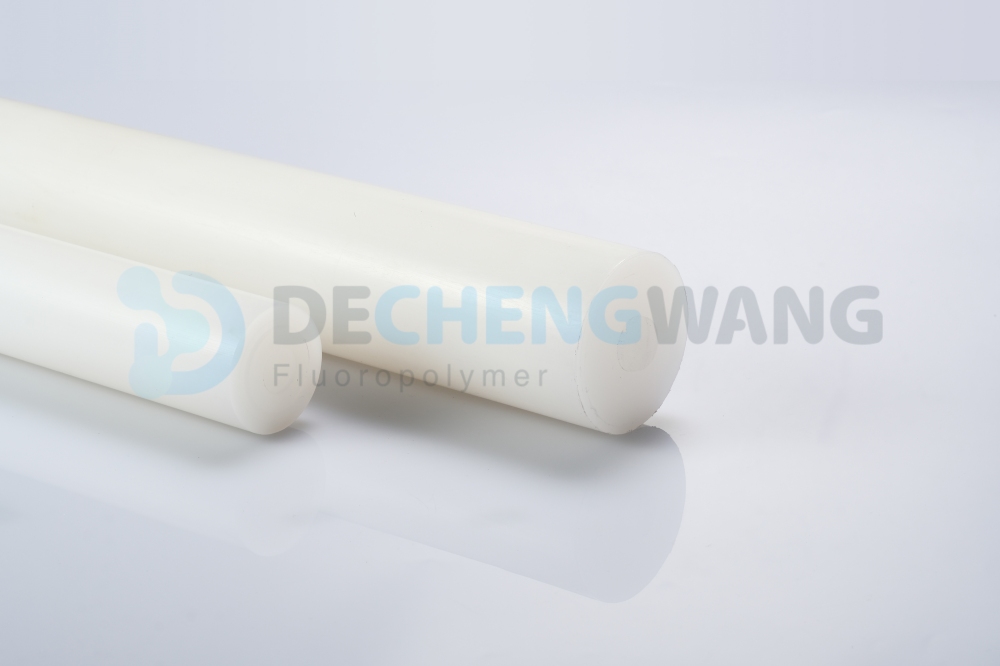
PVDF (Polyvinylidene Fluoride)
Description: PVDF is a versatile fluoropolymer with excellent chemical resistance and high-temperature stability.
Performance advantages: Strong mechanical properties, good chemical resistance, excellent UV resistance, and flame retardancy.
Applications: It is commonly used in chemical processing, electrical insulation, membranes, piping systems, and lithium-ion battery components.
Main manufacturers: Arkema (Kynar), Solvay (Solef).
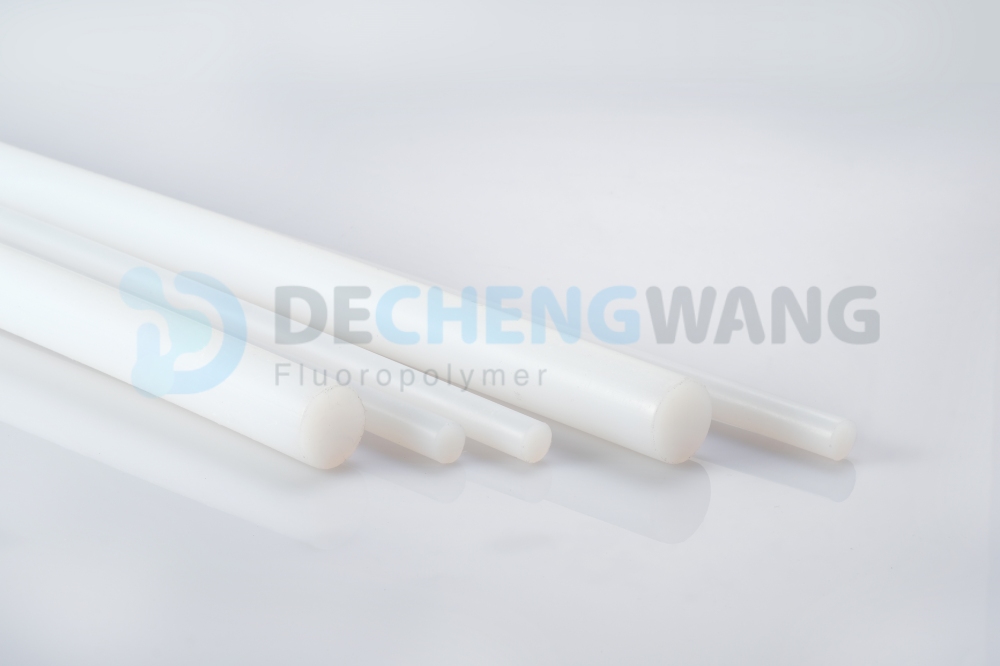
PEEK (Polyether Ether Ketone)
Description: PEEK is a high-performance thermoplastic known for its excellent mechanical properties, high-temperature resistance, and chemical resistance.
Performance advantages: Exceptional strength and stiffness, excellent dimensional stability, high-temperature resistance (up to 250°C), good chemical resistance, and low flammability.
Applications: It is widely used in aerospace, automotive, medical, and electrical industries for applications such as gears, bearings, medical implants, and electrical connectors.
Main manufacturers: Victrex, Solvay (Zeniva), Evonik (Vestakeep).
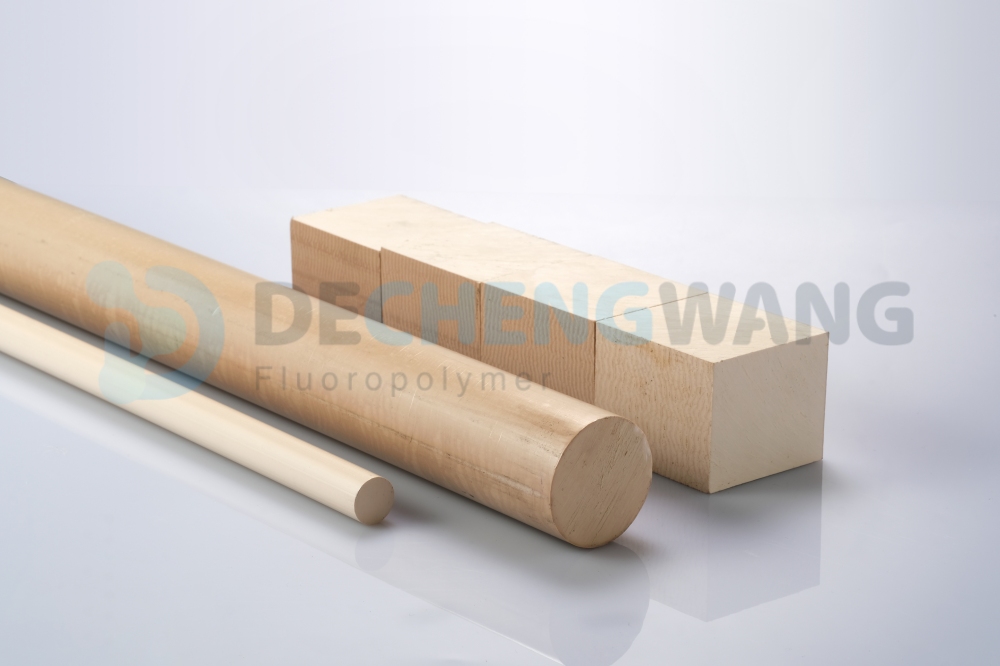
PPS (Polyphenylene Sulfide)
Description: PPS is a high-performance engineering plastic with a combination of high-temperature resistance, chemical resistance, and dimensional stability.
Performance advantages: High strength and rigidity, excellent chemical resistance, low moisture absorption, and good dimensional stability at elevated temperatures.
Applications: It is commonly used in automotive, electrical, and industrial applications such as fuel system components, electrical connectors, and pump parts.
Main manufacturers: Solvay (Ryton), Toray (Torelina).
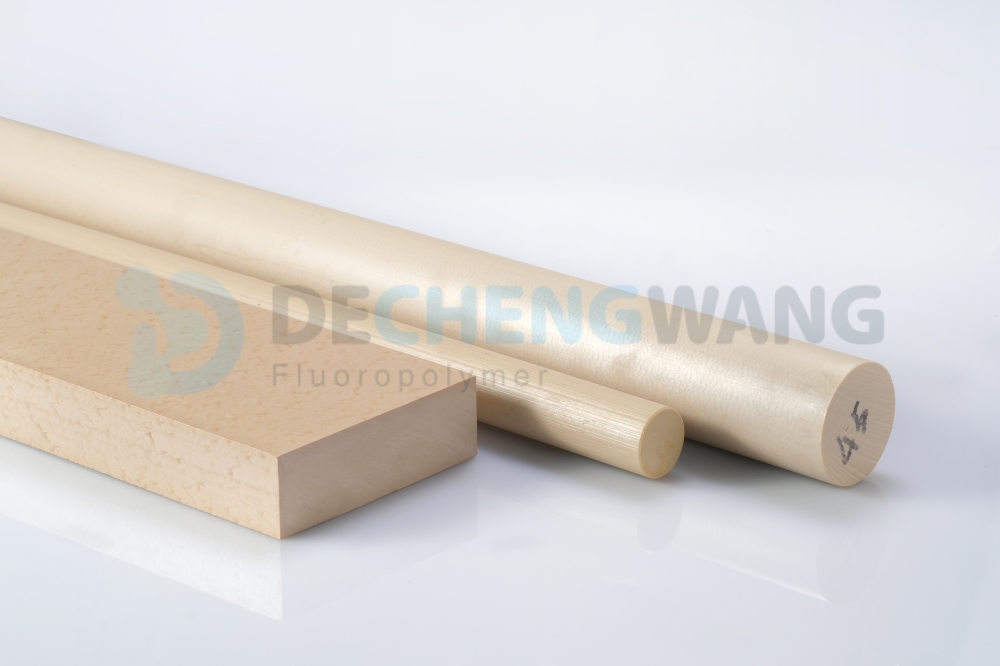
PI (Polyimide)
Description: PI is a high-temperature-resistant polymer known for its exceptional thermal stability, mechanical strength, and chemical resistance.
Performance advantages: Excellent high-temperature resistance (up to 300°C and beyond), exceptional mechanical properties, good chemical resistance, low outgassing, and low coefficient of thermal expansion.
Applications: It is widely used in aerospace, electronics, and semiconductor industries for applications including flexible printed circuit boards, insulation films, and aerospace components.
Main manufacturers: DuPont (Kapton), Mitsui Chemicals (Duratron),.
PAI (Polyamide-Imide)
Description: PAI is a high-performance thermoplastic with exceptional mechanical, thermal, and chemical properties, combining the advantages of polyamides and polyimides.
Performance advantages: High strength and rigidity, excellent dimensional stability, high-temperature resistance (up to 260°C), excellent chemical resistance, and low creep.
Applications: It is commonly used in aerospace, automotive, and electronics industries for applications such as bearings, gears, electrical connectors, and structural components.
Main manufacturers: Mitsui Chemicals (Duratron), Solvay (Torlon)
PBI (Polybenzimidazole)
Description: PBI is a high-performance polymer known for its exceptional heat resistance and flame retardancy.
Performance advantages: Excellent thermal stability (up to 400°C), outstanding flame resistance, low smoke emission, excellent chemical resistance, and high mechanical strength.
Applications: It is commonly used in aerospace, automotive, and industrial applications, including protective clothing, gaskets, seals, and high-temperature electrical insulation.
Main manufacturers: Mitsui Chemicals (Duratron), Solvay (Celazole).
PSU (Polysulfone)
Description: PSU is a high-performance amorphous thermoplastic known for its combination of high-temperature resistance, mechanical strength, and chemical resistance.
Performance advantages: Good dimensional stability, high heat resistance (up to 180°C), excellent chemical resistance, high impact strength, and good electrical properties.
Applications: It is commonly used in medical and dental devices, automotive components, electrical connectors, and plumbing fixtures.
Main manufacturers: Solvay (Udel), BASF (Ultrason).
PES (Polyethersulfone)
Description: PES is a high-performance amorphous thermoplastic known for its excellent combination of mechanical properties and thermal resistance.
Performance advantages: High heat resistance (up to 180°C), excellent dimensional stability, good chemical resistance, high toughness, and good electrical properties.
Applications: It is commonly used in medical equipment, filtration membranes, aerospace components, and electrical insulation.
Main manufacturers: Solvay (Radel), BASF (Ultrason).
PPSU (Polyphenylsulfone)
Description: PPSU is a high-performance amorphous thermoplastic known for its exceptional thermal and chemical resistance.
Performance advantages: Excellent heat resistance (up to 220°C), outstanding chemical resistance, good dimensional stability, high impact strength, and transparency.
Applications: It is commonly used in medical and dental instruments, aircraft interiors, plumbing components, and electrical connectors.
Main manufacturers: Solvay (Radel), BASF (Ultrason).
PEI (Polyetherimide)
Description: PEI is a high-performance amorphous thermoplastic known for its excellent balance of mechanical, thermal, and electrical properties.
Performance advantages: High heat resistance (up to 180°C), excellent dimensional stability, good chemical resistance, high strength and stiffness, good electrical insulation properties.
Applications: It is commonly used in electrical connectors, automotive components, aerospace applications, and medical devices.
Main manufacturers: SABIC (Ultem)
Conclusion
In conclusion, high-performance plastics play a vital role in various industries, offering a wide range of exceptional properties and performance advantages. These advanced materials provide superior mechanical strength, temperature resistance, chemical resistance, wear resistance, and electrical insulation properties. Their applications span across aerospace, automotive, medical, electronics, and many other sectors.
At Dechengwang, we recognize the significance of high-performance plastics and the value they bring to modern engineering and manufacturing. As a leading company in the industry, we are committed to providing top-quality high-performance plastics, collaborating with reputable manufacturers, and delivering innovative solutions tailored to meet our customers’ specific requirements. Partner with us to unlock the full potential of high-performance plastics and gain a competitive edge in today’s demanding market.