This blog is a comprehensive guide on a kind of essential industrial component, lip seals. The lip seals are commonly used in various mechanical systems, ranging from industrial machinery to automotive applications.
The reason why they are used in so many applications is their excellent performance in preventing leakage and contamination.
This blog will talk about the information on lip seals from all the aspects, such as their design, functions, materials, and so on. No matter whether you are an expert in the field of industrial parts or who want to get some basic knowledge about mechanical systems, this post will always be helpful.
You’ll learn the secrets of the lip seals’ high efficiency and outstanding durability, as well as the vital role they play in keeping industries running smoothly.
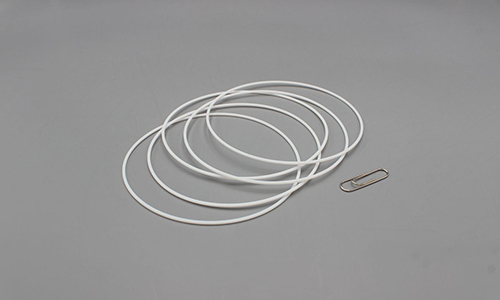
What Are Lip Seals
Lip seals are called by many names, such as oil seals or rotary shaft seals. This type of mechanical seal is designed to prevent the leakage of some fluids used in industrial processes, including oil or grease. Those seals provide a barrier between the moving shaft and the fixed shell or hole.
In order to achieve the perfect effect of lip seal in isolating liquid, people choose to use some elastic material to produce them. The lip seals made of elastic materials can have sufficient contact pressure with the holding shaft, which is more effective in preventing fluid leakage and eliminating the risk of contaminants entering the system.
Common Types of Lip Seals in Industries
Lip seals come in various types, each designed to suit specific sealing applications. Let’s explore some of the most common types of lip seals found in industries.
Radial Lip Seals
Radial lip seals feature a flexible lip made of an elastomeric material that creates a dynamic seal with a rotating shaft, preventing lubricant leakage and the ingress of contaminants.
The outer casing of the seal provides structural support, while additional features like garter springs enhance sealing performance. Radial lip seals play a crucial role in applications such as engines, pumps, gearboxes, and motors, ensuring optimal lubrication, preventing damage, and extending the lifespan of machinery.
Their selection depends on factors such as shaft size, operating conditions, and application requirements.
Axial Lip Seals
The key difference between axial lip seals and other kinds of lip seals lies in the design of the sealing lip. In axial lip seals, the lip is typically angled or curved to match the rotational movement of the shaft. This design allows the lip to maintain constant contact with the shaft during rotation, ensuring a reliable and consistent seal.
The lip is often spring-loaded to provide optimal sealing pressure, compensating for wear and variations in shaft movement.
Another difference between axial lip seals and other kinds of lip seals is the consideration for lubrication. Axial lip seals are specifically designed to retain lubricants within the system and prevent their leakage during rotary motion. This is particularly important in applications where continuous lubrication is required, such as in rotating machinery and equipment.
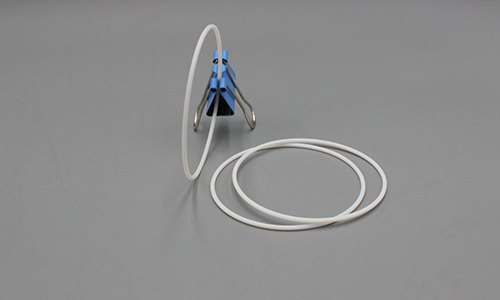
Rotary Lip Seals
Rotary lip seals can be engineered with specific materials and designs to meet the demands of extreme temperatures, from freezing cold to high-heat environments. They are capable of maintaining their sealing performance and flexibility even under these challenging conditions.
Additionally, rotary lip seals can be designed to withstand varying pressure differentials. They are constructed to handle both high-pressure and low-pressure applications, ensuring effective sealing performance in systems that operate under different pressure conditions.
Furthermore, rotary lip seals exhibit compatibility with a wide range of fluids and media, including oils, lubricants, hydraulic fluids, fuels, and chemicals. Depending on the specific application and media being sealed, appropriate materials and lip designs can be chosen to ensure compatibility and prevent degradation or chemical attacks.
V-Ring Seals
V-ring seals have the ability to provide reliable sealing in both static and dynamic applications.
In static applications, where there is no relative motion between the shaft and housing, V-ring seals can create a secure and leak-proof seal. They can be used to seal stationary shafts or stationary housings, preventing the escape of fluids or the ingress of contaminants.
In dynamic applications, where there is relative motion between the shaft and housing, V-ring seals excel at maintaining effective sealing. The flexible nature of the V-ring allows it to adjust and maintain contact with the rotating or reciprocating shaft, ensuring a continuous seal even during movement.
This makes V-ring seals suitable for applications where there are axial movements or vibrations, providing reliable sealing performance.
Materials for Manufacturing Lip Seals
Lip seals are available in a variety of materials, each with its own unique properties and suitability for specific applications. Here are some commonly-used materials for lip seals:
Polytetrafluoroethylene (PTFE)
Polytetrafluoroethylene (PTFE) offers numerous advantages for manufacturing lip seals. For example, it exhibits exceptional chemical resistance to a wide range of aggressive substances, ensuring reliable sealing performance in chemically demanding environments.
PTFE’s low friction coefficient reduces energy consumption, minimizes wear, and promotes smooth operation. With its wide temperature range, PTFE lip seals maintain their sealing properties in extreme conditions, from high heat to cryogenic temperatures. The non-stick surface prevents the adhesion of contaminants, ensuring clean and efficient sealing.
These properties make PTFE lip seals reliable, long-lasting, and well-suited for demanding industrial applications where superior sealing performance and resistance to harsh environments are required.
Also Read: >> PTFE VS PFA: A Brief Comparison
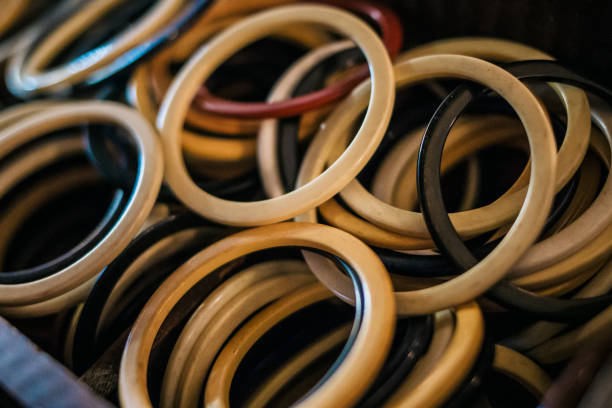
Silicone Rubber
Silicone rubber offers a wide temperature range, allowing lip seals to function reliably in both high-heat and cold environments. Its flexibility and elasticity enable the seals to adapt to shaft movements and minor misalignments, maintaining effective sealing.
Silicone rubber exhibits excellent resistance to weathering, UV radiation, and ozone, making it suitable for outdoor applications. The material’s good sealing performance ensures a reliable barrier against fluid leakage. Silicone rubber is also versatile, allowing for customization based on specific requirements.
Additionally, its biocompatibility makes it suitable for medical applications, and its ease of manufacturing allows for efficient production of lip seals.
Thermoplastic Polyurethane (TPU)
TPU lip seals possess hydrolysis resistance, ensuring durability in moist environments. The material’s low compression set enables quick recovery after compression, maintaining effective sealing over time. TPU’s inherent noise-dampening properties reduce vibration and noise transmission, beneficial in applications prioritizing noise reduction.
Additionally, TPU lip seals can have a softer sealing surface for improved conformability on rough mating surfaces. These advantages, along with wear resistance, flexibility, wide temperature range, and chemical resistance, make TPU an ideal choice for lip seals in various industries and demanding applications.
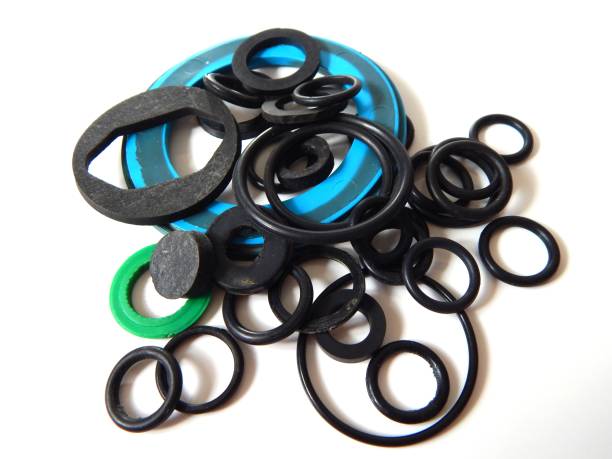
Nitrile Rubber (NBR)
NBR lip seals exhibit excellent resistance to oils and fuels, making them ideal for sealing applications in automotive, oil and gas, and hydraulic systems. NBR is a cost-effective option without compromising sealing performance.
The material maintains its shape and sealing properties even after prolonged compression. NBR lip seals perform well across a broad temperature range and offer good abrasion resistance. Additionally, NBR is easy to process and mold, allowing for efficient manufacturing. These advantages, along with chemical compatibility and durability, make NBR lip seals a reliable choice for various industries.
Fluoroelastomers (FKM)
FKM lip seals exhibit excellent weather resistance, maintaining sealing performance in harsh outdoor environments. They provide a wide range of hardness options, allowing customization to meet specific application requirements. FKM lip seals have inherent flame resistance, enhancing safety compliance.
With high chemical inertness, they resist aggressive substances. FKM lip seals show minimal swelling and volume change when exposed to fluids, ensuring dimensional stability. These added benefits, combined with FKM’s temperature resistance, make them versatile and reliable in industries such as automotive, aerospace, chemical processing, and oil and gas.
Ethylene Propylene Diene Monomer (EPDM)
EPDM lip seals exhibit excellent weather resistance, making them suitable for outdoor applications. They have a wide temperature range capability, maintaining sealing effectiveness in extreme conditions. EPDM is highly resistant to water, steam, and chemicals, ensuring reliable sealing performance.
This material also possesses good electrical insulation properties, adding versatility to its applications. With a low compression set, EPDM lip seals maintain their shape over time. Additionally, EPDM exhibits good elasticity and flexibility, adapting to surface irregularities and dynamic movements.
These advantages, coupled with durability and cost-effectiveness, make EPDM lip seals popular in various industries.
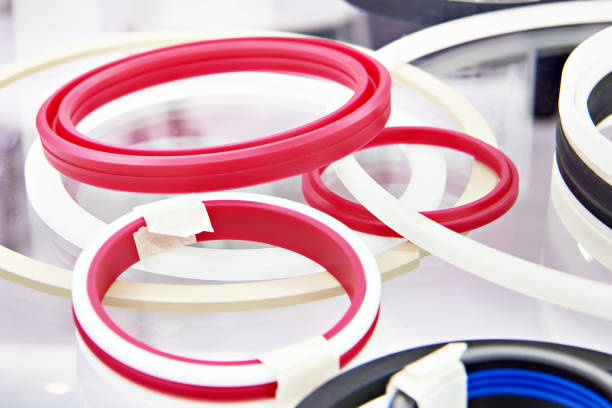
The Wide Applications of Lip Seal in Various Industries
Lip seal is widely used in various industries, including but not limited to the automobile manufacturing industry, aviation industry, etc. They can ensure efficient sealing and lubrication of motors, pumps, transmissions, and other equipment.
Automotive Industry
The lip seals provide effective fluid sealing, protecting automotive systems from leaks and maintaining proper functionality. Lip seals offer environmental protection, guarding against contaminants and harsh conditions. They reduce friction between moving parts, minimizing wear and extending component lifespan.
With reliable sealing performance, they ensure system efficiency. Additionally, lip seals are a cost-effective solution, customizable for various automotive applications. Their versatility and widespread use in engines, transmissions, steering systems, and more make them indispensable in the automotive industry.
Aerospace Industry
Lip seals are highly valued in the aerospace industry for their exceptional benefits and widespread use. With their precise fluid sealing capabilities, lip seals play a crucial role in safeguarding critical systems from leakage and ensuring reliable operation in demanding aerospace environments.
Additionally, lip seals offer environmental protection by preventing the ingress of contaminants and resisting extreme conditions such as high temperatures and pressure differentials. Their ability to reduce friction between moving components contributes to improved energy efficiency and extended equipment lifespan.
Compliant with stringent aerospace standards, lip seals provide the necessary reliability and performance required for aerospace applications. Furthermore, their customization options and seamless integration into various components make them a preferred choice. Lastly, lip seals contribute to reduced maintenance needs, resulting in increased operational uptime and cost savings for the aerospace industry.
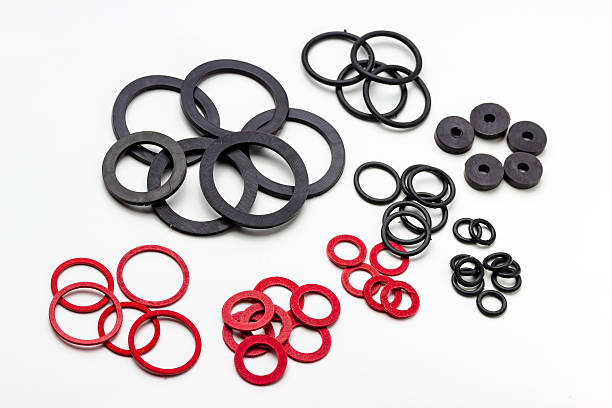
Oil and Gas Industry
The oil and gas industry widely embraces lip seals due to their multitude of benefits and the vital role they play in various applications. With their ability to effectively contain fluids within systems, lip seals ensure the safe and efficient transfer of fluids while minimizing the risk of leakage.
Besides that, lip seals provide crucial environmental protection by sealing out contaminants and withstanding the demanding conditions commonly encountered in oil and gas operations. These versatile seals also reduce friction and wear, prolonging equipment lifespan and reducing maintenance costs.
Overall, lip seals offer indispensable advantages that enhance the safety, reliability, and efficiency of the oil and gas industry.
Industrial Machinery
When it comes to industrial machinery, lip seals have garnered widespread usage owing to their manifold benefits and their indispensable role in various applications. These seals are specifically designed to effectively contain fluids within machinery, ensuring a secure and efficient transfer while mitigating the risk of leaks.
By sealing the gaps between rotating or reciprocating components, such as shafts and cylinders, lip seals play a crucial role in maintaining fluid integrity. Additionally, lip seals act as a protective barrier, safeguarding sensitive machinery components from contamination caused by dust, dirt, and moisture commonly present in industrial environments.
Chemical Processing
In the realm of chemical processing, lip seals have gained significant traction owing to their manifold benefits and their pivotal role in ensuring safe and efficient operations. These seals excel in chemical compatibility, effectively containing fluids within equipment and preventing leaks that could lead to hazardous situations.
Moreover, lip seals offer vital environmental protection by resisting harsh conditions and sealing out contaminants that could compromise the integrity of the system. By reducing friction and wear, these seals extend the lifespan of equipment, resulting in reduced maintenance costs and minimal downtime. Customizable to specific applications, lip seals provide a tailored solution to meet the diverse needs of the chemical processing industry.
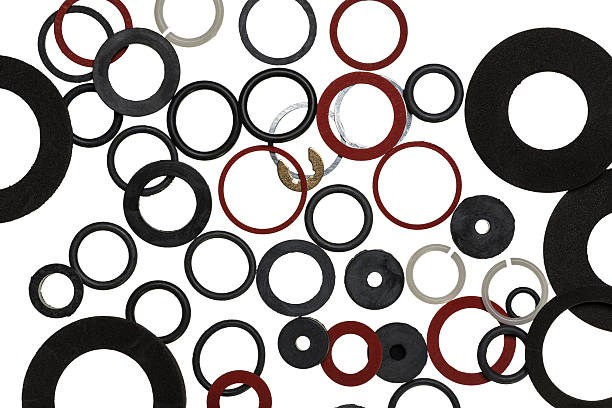
Power Generation
The lip seals are also popular in the power generation industry due to their ability to effectively contain fluids, such as water, steam, and lubricants, within the equipment, thus preserving the integrity and safety of power generation systems.
In addition to that, lip seals provide crucial environmental protection, effectively sealing out contaminants and resisting the demanding conditions encountered in power generation processes. By reducing friction and wear, these seals contribute to extended equipment lifespan, resulting in reduced maintenance costs and improved operational efficiency.
With their versatility, cost-effectiveness, and positive impact on system performance, lip seals have become indispensable components in the power generation industry.
Factors That Influence the Performance of Lip Seals
Lip seals play a critical role in maintaining the integrity and functionality of various systems. Several factors can significantly influence the performance of lip seals, ensuring their effectiveness and longevity.
Pressure
Pressure significantly influences the performance of lip seals. Higher pressure levels exert greater forces on the sealing interface, potentially causing extrusion or deformation. Selecting a lip seal that can withstand the specific pressure requirements is crucial to ensure reliable sealing and prevent leaks.
Insufficient pressure can result in inadequate sealing force and potential system leaks. It is essential to consider the pressure conditions under which the lip seal will operate and choose a seal designed to withstand the required pressure range. This ensures optimal sealing performance, prevents costly downtime, and avoids system failures.
Temperature
Extreme temperatures can affect the seal material’s elasticity and sealing properties. High temperatures can lead to material softening and degradation, compromising sealing integrity, while low temperatures can result in stiffness and reduced flexibility.
Selecting a lip seal that can withstand the temperature range is vital to maintain effective sealing. Temperature compatibility ensures the seal material retains its integrity and flexibility, preventing leaks.
By considering temperature requirements and choosing an appropriate lip seal material, optimal sealing performance can be achieved, preventing temperature-induced seal failure and ensuring reliable operation.
Surface Finish and Roughness
The performance of lip seals is also influenced by the surface finish and roughness of mating surfaces. Rough surfaces and irregularities cause increased friction, wear, and reduced sealing efficiency. Proper surface preparation, including machining and finishing, ensures optimal contact between the lip seal and mating surfaces.
A smooth and well-finished surface promotes a secure seal, minimizes friction, and distributes sealing force evenly. Controlling surface finish and roughness is crucial for optimizing sealing performance and extending lip seal lifespan. By considering and managing surface conditions, engineers enhance lip seal effectiveness, reduce leak risks, and ensure efficient system operation.
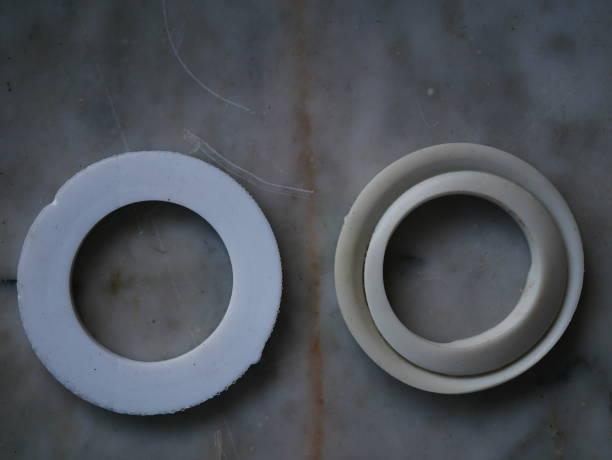
Lubrication
Lubrication is another factor that affects the sealing effectiveness, frictional behavior, and overall longevity of the seal.
Proper lubrication reduces friction and wear between the lip seal and the mating surfaces, minimizing heat generation and ensuring smooth operation. It helps to maintain a consistent and reliable sealing interface, preventing leaks and optimizing sealing performance.
Insufficient lubrication can lead to increased friction and wear, resulting in accelerated seal degradation and potential system failures. On the other hand, excessive lubrication may cause seal swelling or loss of sealing integrity.
Choosing the right lubricant and applying it in the correct quantity is crucial for the optimal performance of lip seals. It ensures proper lubrication film formation, reduces friction, and enhances the overall lifespan of the seal.
Tips for the Maintenance of Lip Seals
Proper maintenance is essential to ensure the longevity and optimal performance of lip seals. By following these tips, you can enhance the reliability and efficiency of your sealing system.
Follow Proper Installation Procedures
Proper installation procedures are essential for maintaining lip seals effectively. They ensure correct positioning, alignment, and securing of the seals within the system. This promotes effective sealing, prevents leaks, and maintains system integrity. Adhering to manufacturer recommendations safeguards seals from distortion, misalignment, or damage, ensuring longevity and performance.
Regular Inspection
Regularly inspect lip seals for wear, damage, or leakage. Early detection allows for timely repairs or replacement, preventing potential system failures and costly downtime.
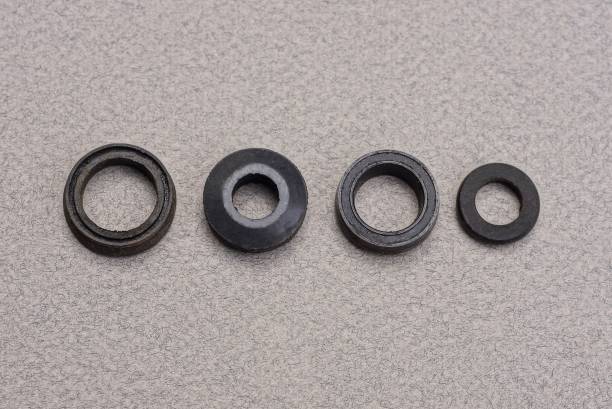
Clean Surrounding Areas
Maintain a clean environment around lip seals to prevent the accumulation of dirt, debris, or contaminants. Regular cleaning prevents abrasion, interference with sealing, and accelerated wear.
Consult Manufacturer Recommendations
Refer to the manufacturer’s guidelines for specific maintenance procedures, cleaning agents, lubricants, and replacement intervals. Following their recommendations ensures effective maintenance and optimal performance.
Get High-Quality PTFE Lip Seals from DECHENGWANG
When it comes to PTFE lip seals, DECHENGWANG is your trusted source for high-quality components. Here’s why you should choose us:
OEM PTFE Components
DECHENGWANG specializes in manufacturing OEM PTFE lip seals tailored to your specific requirements. Our experienced team works closely with you to understand your needs and deliver custom solutions that meet your exact specifications.
Maintain Tight Tolerance
Precision is our priority. We have advanced manufacturing capabilities that allow us to maintain tight tolerances, ensuring the accuracy and consistency of our PTFE lip seals. You can rely on our products for reliable sealing performance and long-lasting durability.

Cleanroom Manufacturing
We prioritize cleanliness and purity in our manufacturing processes. Our state-of-the-art cleanroom facilities ensure that our PTFE lip seals are produced in a controlled environment, minimizing the risk of contamination and ensuring optimal quality.
Flexible MOQ
We understand that each project has unique requirements, and we offer flexible minimum order quantities (MOQ) to accommodate your needs. Whether you need a small batch or a large production run, we can provide you with the desired quantity of PTFE lip seals.
Conclusion
In conclusion, lip seals are essential components widely used across industries for reliable sealing solutions. Understanding their types, materials, and performance factors is crucial for selecting the right seal. Proper installation, regular maintenance, and adherence to manufacturer recommendations ensure optimal performance.
DECHENGWANG offers high-quality PTFE lip seals with customized solutions, precision manufacturing, cleanroom facilities, and flexible MOQ. By choosing DECHENGWANG, you gain access to expertly crafted sealing solutions that enhance reliability and efficiency. Trust in DECHENGWANG’s expertise to meet your lip seal needs and enjoy the benefits of reliable sealing solutions.