With the information and expertise you’ll gain from this detailed guide, you can machine PEEK (Polyetheretherketone). PEEK is a versatile material renowned for its excellent performance properties. Learn priceless insights and tips to improve your machining skills and release PEEK’s full potential in precision manufacturing. Let’s get started and learn to machine PEEK efficiently.
What Features Make PEEK Suitable For Machining?
Industries frequently use PEEK to create a variety of products. This is because PEEK plastic has superb and remarkable qualities. The following characteristics of PEEK are highly valued by manufacturers:
High Temperature And Chemical Resistance
PEEK is known for its exceptional performance during high temperatures. It performs electrically well when faced with high frequencies and temperatures. It can survive intense amounts of ionizing radiation and keeps its stability when exposed to chemicals.
Also, when used with corrosive materials, it offers strong resilience. Like most metals, it maintains its non-corrosive chemical structure even at high temperatures and offers resistance. These qualities make it suitable for PEEK machining.
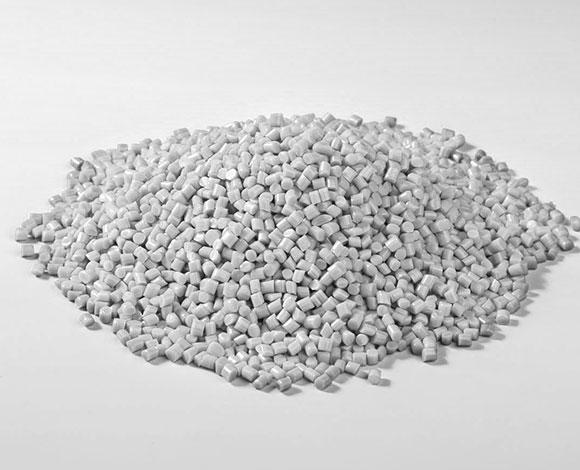
Mechanical Strength
PEEK is the perfect material for plastic machining because it offers outstanding mechanical strength. It provides exceptional wear, impact, and fatigue resistance when applied in demanding applications and retains structural integrity. It performs well even under heavy loads, guaranteeing long-lasting performance in various machining procedures.
Dimensional Stability
Dimensional stability is a necessary property to look for in a material to apply for machining. PEEK plastic is famous for its remarkable dimensional stability, maintaining its size and form even in challenging conditions such as precision machining and high-temperature conditions.
Due to PEEK’s low coefficient of thermal expansion, there is less chance that temperature changes may result in dimensional changes. This results in accurate and dependable PEEK milling results.
Applications That Benefit From Machined PEEK Parts
The number of industries that use machined PEEK parts is limitless. A few of the main industries that reap the benefits of machined PEEK parts are:
Oil And Gas
PEEK’s exceptional chemical resistance makes it ideal for the oil and gas industry. Electrical connections and seals made of PEEK are common parts that act as insulators and isolators and support softer seal materials. Additionally, PEEK valve seats and seals regulate the flow of chemical gases and liquids without risking deterioration.
Electronics And Electrical Engineering
Excellent electrical characteristics make PEEK a perfect electrical insulator. PEEK can be processed into components with long-term operational dependability in wildly varying temperature, pressure, and frequency ranges. These qualities make it perfect for applications in electronics.
Electronic enclosures, housings, semiconductor manufacturing, connectors, and insulator production all commonly use PEEK.
Food And Beverage
The Food and Beverage sector has benefited greatly from the innovative uses of PEEK machined components, which have transformed how consumables are handled and processed. PEEK guarantees that the quality and flavor of food and beverages are not impaired because of its outstanding chemical resistance.
PEEK machining parts endure the toughest circumstances while upholding hygienic requirements, withstanding anything from caustic cleaning agents to high-temperature sterilizing procedures. Due to its various strength and resilient properties, it is a stable material for food processing equipment. PEEK ensures safety and high performance because of its non-reactive nature and FDA compliance.
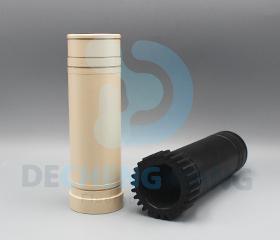
Chemical Processing
PEEK machined parts stand as pioneers in the dynamic world of chemical processing, delivering durability and adaptability to the sector. Because of their outstanding chemical resistance, PEEK parts can endure caustic chemicals, strong solvents, and high temperatures.
PEEK is used to create pumps, valves, seals, and gaskets for the chemical processing industry. It performs amazingly for critical applications where accuracy and durability are important because of its mechanical strength and dimensional stability, which are mentioned in the above section. PEEK gives the chemical processing sector the confidence to pursue innovation and create the best products.
Tips For The Process of Machining PEEK
Machining PEEK requires careful consideration to provide the best results. Continue reading to find out the tips for the optimal process of PEEK milling.
Choose The Right Cutting Tools
Selecting the appropriate cutting tools is critical for getting the best results while PEEK machining. Tools with a carbide or diamond coating are strongly advised due to PEEK’s special qualities, such as its great strength and heat resistance.
These tools are exceptionally hard and are capable of withstanding the difficult machining conditions related to PEEK. On the other hand, high-speed steel tools cannot be as durable and can wear out quickly when used with PEEK.
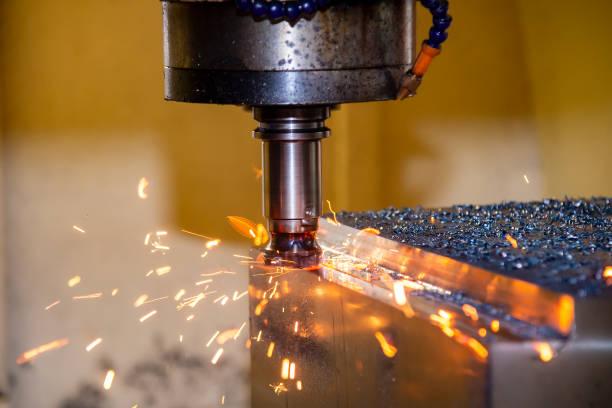
Set Proper Cutting Parameters
The most important step in effective PEEK machining is adjusting the cutting settings. Cutting speed and depth of cut adjustments should be made carefully since they greatly influence the whole plastic machining process and the quality of the completed components.
- Maintaining a low cutting speed to reduce heat accumulation
- Choosing a moderate feed rate for effective material removal
- Carefully controlling the depth of cut to avoid tool overload and workpiece deformation
These are the steps in optimizing cutting parameters for PEEK machining. These factors help to provide effective PEEK machining with increased precision and reduced hazards.
Effective Cooling And Lubrication
Due to PEEK’s poor thermal conductivity, controlling heat accumulation during milling is essential. Successful PEEK machining depends heavily on adequate cooling and lubricating methods.
- Cooling: Continuous cooling aids in temperature regulation and prevents the buildup of too much heat, which might cause the material’s melt or damage the cutting tool.
- Lubrication: Through a reduction in chip adherence to the tool or workpiece surface, lubrication promotes chip evacuation.
Machinists can lessen the difficulties caused by PEEK’s limited heat conductivity by using efficient cooling and lubricating procedures. The success and effectiveness of PEEK milling operations are largely dependent on proper heat management, which guarantees increased tool life, dimensional precision, and surface polish.
Regularly Monitor The Machining Process
Monitoring the machining process is essential and critical to ensure constant and reliable output and avoid any possible problems throughout the operation. The steps for monitoring the PEEK milling process are as follows:
- Check the tools being used on a regular basis for damage.
- While machining, keep an eye on many additional elements, such as cutting forces, temperature changes, and chip formation
- Examine the forces applied to the tool and workpiece during the process
- A crucial part of the reviewing machining process also involves temperature monitoring
Appropriate Chip Evacuation Methods
Working with PEEK machining often means dealing with long, stringy chips that can hinder the cutting process if not addressed properly. To prevent disruption during machining and maintain overall efficiency in product quality standards, it’s important to apply accurate chip removal methods.
Reliable Provider Of PEEK Machining Service: DCW
DCW (Dechengwang), a Chinese company based in Shenzhen, has steadily risen to the top of the country’s leading experts in the fluoropolymer field.
Aided by proficient knowledge coupled with years-long experience within this sector, DCW is well-positioned to offer versatile customized PEEK parts production solutions, thereby building trust amongst the customer base.
Custom The Sizes Of PEEK Parts
The value proposition of selecting DCW lies not only with our superior products but also with our commitment to individualized customer service – starting with bespoke PEEK component size offerings.
Furthermore, quality machining ensures accurate sizing for small-batch orders and mass production, promising optimal performance and longevity of end-use products upon installation.
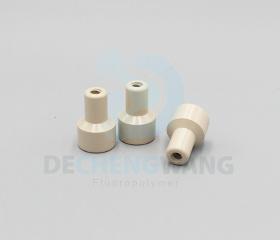
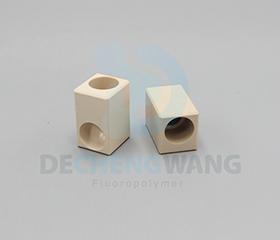
Source: PEEK parts
Flexible MOQ
DCW offers minimum order quantities (MOQ) that are customizable. Since not every customer has the same volume requirements, DCW offers small and big production runs, guaranteeing that every client has unlimited access to their premium PEEK machining services.
Conclusion
PEEK has become one of the most sought-after materials for creating parts for various applications in different industries. With the above-given information, you can optimally use this material for your business needs.
DCW provides the best PEEK machining products and uses top-quality PEEK plastic and methods to create products that perform exceptionally. You can anticipate excellent craftsmanship, attention to detail, and first-class customer service when working with DCW for your PEEK machining needs. Contact DCW today and get a quote.