Introduction:
PTFE, or polytetrafluoroethylene, is a synthetic fluoropolymer of great commercial value. Its unique properties such as high chemical resistance, non-stick surface, and low coefficient of friction have earned it special recognition in the plastic industry. Since its discovery by Dr. Roy Plunkett in 1938, it has ” revolutionized the plastic industry and led to vigorous applications not otherwise possible. PTFE manufacturing process is important to ensure the property of PTFE finished parts.
While PTFE is a thermoplastic, it exhibits extremely high viscosity and is prone to fracturing when subjected to shear stresses within the temperature range between its crystalline melting point (327-340 °C; 621-644°F) and the onset of rapid thermal degradation (>410°C; >770 °F). Consequently, PTFE cannot be injection molded or melt extruded like other thermoplastics, necessitating the development of fundamentally different processing methods.
In this blog, we will explore the various manufacturing processes involved in creating PTFE products, including PTFE compression molding, PTFE automatic molding, PTFE isostatic molding, PTFE machining, PTFE paste extrusion, PTFE ram extrusion, PTFE etching, PTFE skiving, PTFE punching, and PTFE coating.
PTFE manufacturing process 1 – PTFE Compression molding:
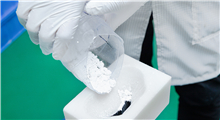
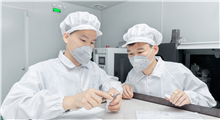
PTFE Compression molding, the basic technique for PTFE molding, allows for the production of articles with simple shapes, such as sheets, blocks, rods, tubes, and more. The underlying principles of compression molding can be summarized as follows:
- Uniform PTFE Powder Charging: The mold is evenly filled with powder.
- Compression: The PTFE powder is compressed to pressure ranging from 10 to 100 MPa at room temperature.
- Sintering: The compressed material is sintered at temperatures between 360°C and 380°C (680°F and 716°F), causing the particles to bond together.
- Cooling: After sintering, the material is cooled down to set its shape.
PTFE Compression molding can be categorized into normal compression molding, automatic compression molding, and isostatic molding. The mechanical processes associated with these primary methods are explained as below:
Molding Method | Charging | Compression | Sintering |
Normal compression molding | Manual | Press | Sinter, then cool slowly |
Automatic compression molding | Manual or Automatic | Automatic press | Sinter, then cool slowly |
Isostatic molding | Manual | Fluid pressure | Sinter, then cool slowly |
PTFE normal compression molding:
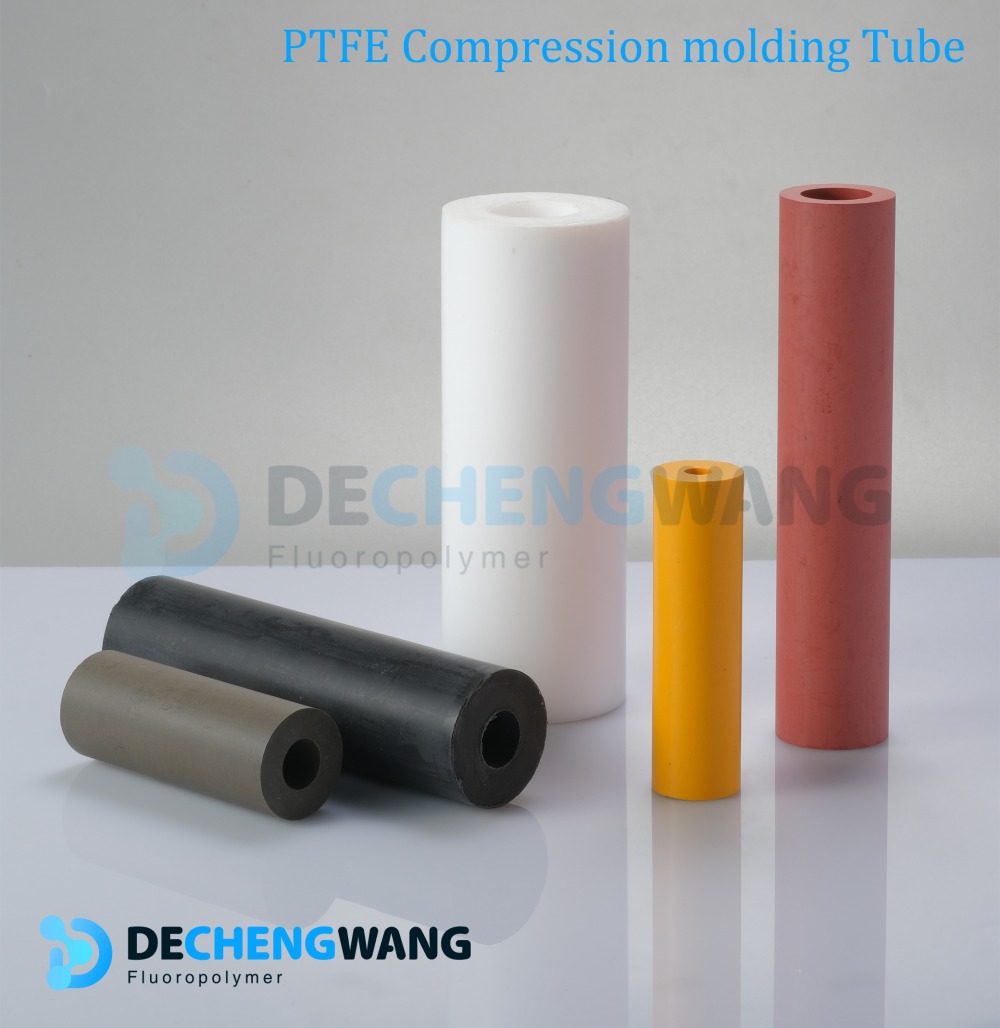
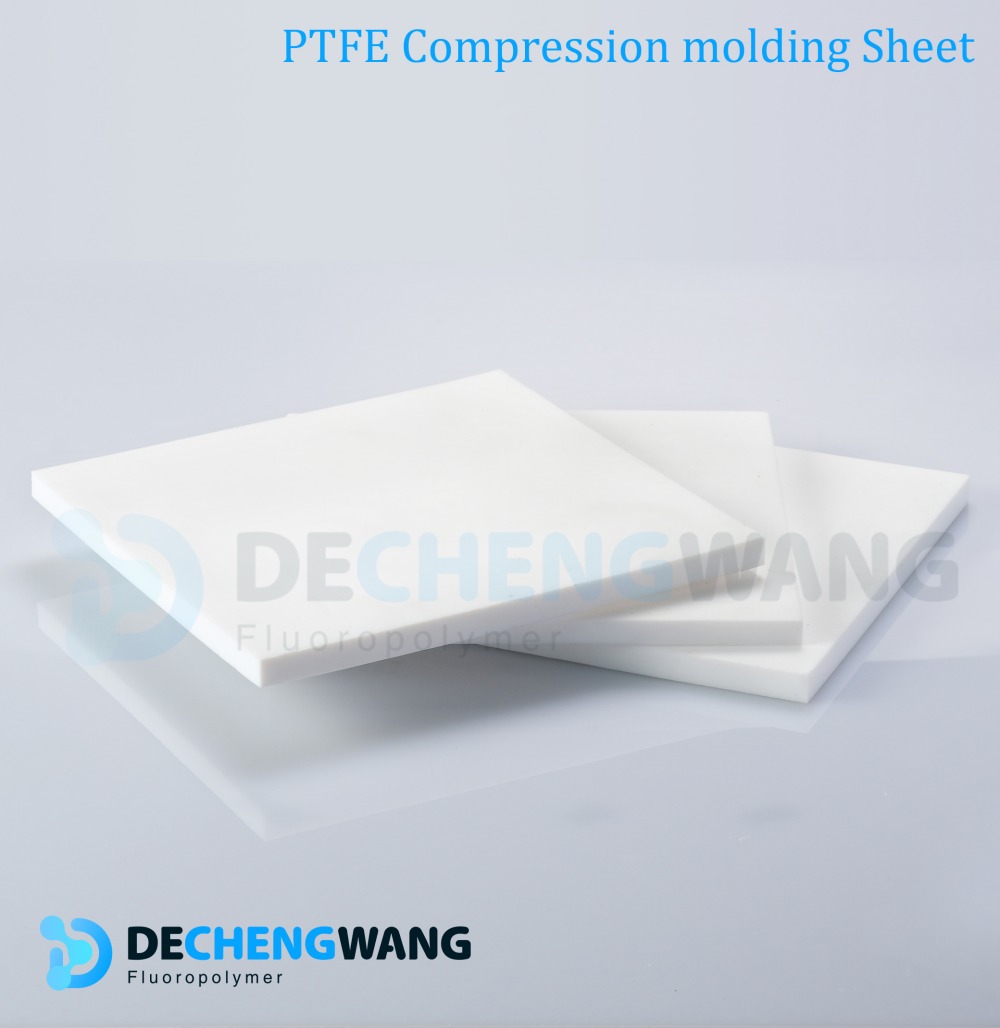
PTFE normal compression molding is the simplest method of PTFE molding. This method of compression molding allows for the production of final products ranging from several grams to several hundred kilograms in weight. It is the most used processing method for cylindrical, rectangular and sheet shapes of PTFE.
PTFE resin is manually loaded into the mould and compressed to form a preform under vertical pressure in a hydraulic press for a specified time delivering the desired shape. The preform is then placed inside an oven, where it undergoes a series of programmed heating and cooling rates and dwell times. The two cycles together are commonly called sintering cycle.
During the sintering cycle, the preform is subjected to heating above the resin’s crystalline melting point. This elevated temperature allows the resin fuse together, forming a solid part with the desired shape. The subsequent cooling cycle is employed to regulate the crystallinity of the part, thereby influencing its final properties.
The characteristics of the molded part are influenced by several factors, including the pressure applied during preforming, the duration of dwell time, the sintering time and temperature, as well as the rate of cooling. These parameters collectively determine the physical and mechanical properties of the final product.
PTFE Automatic compression molding:
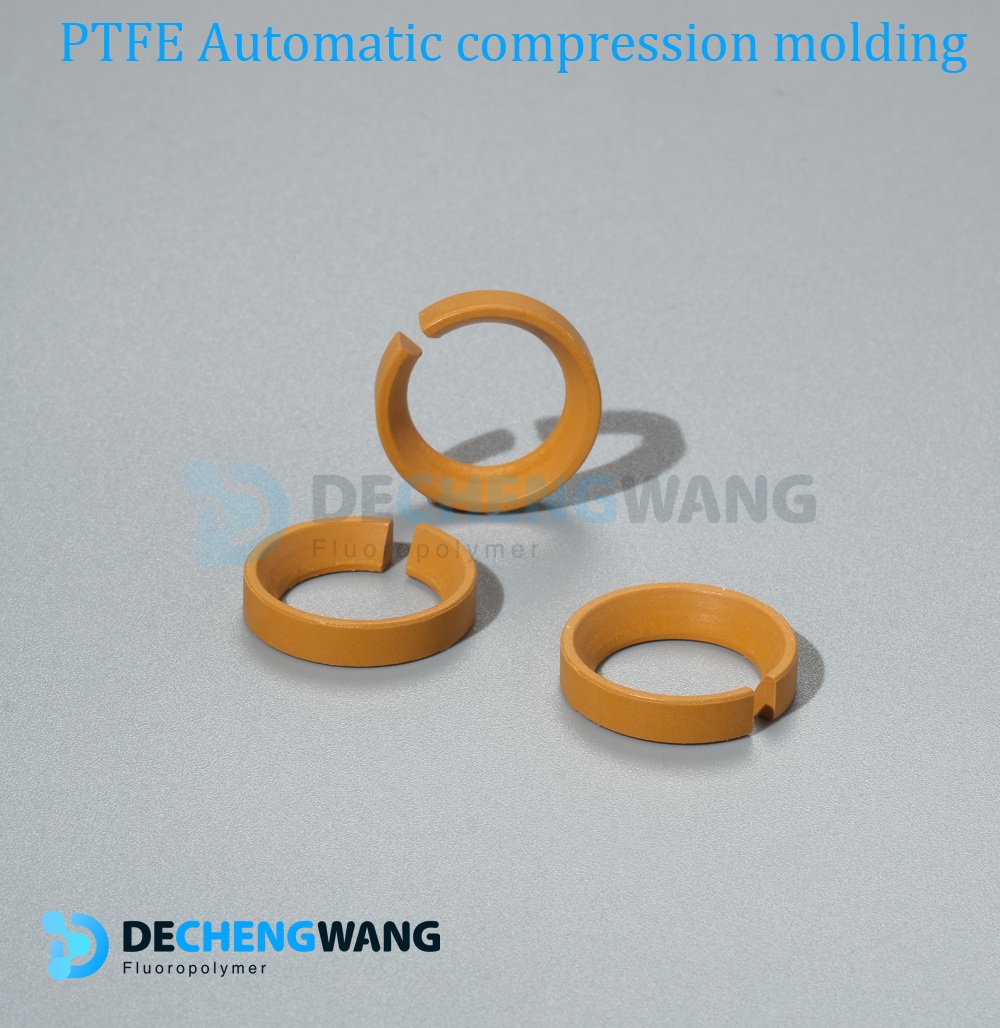
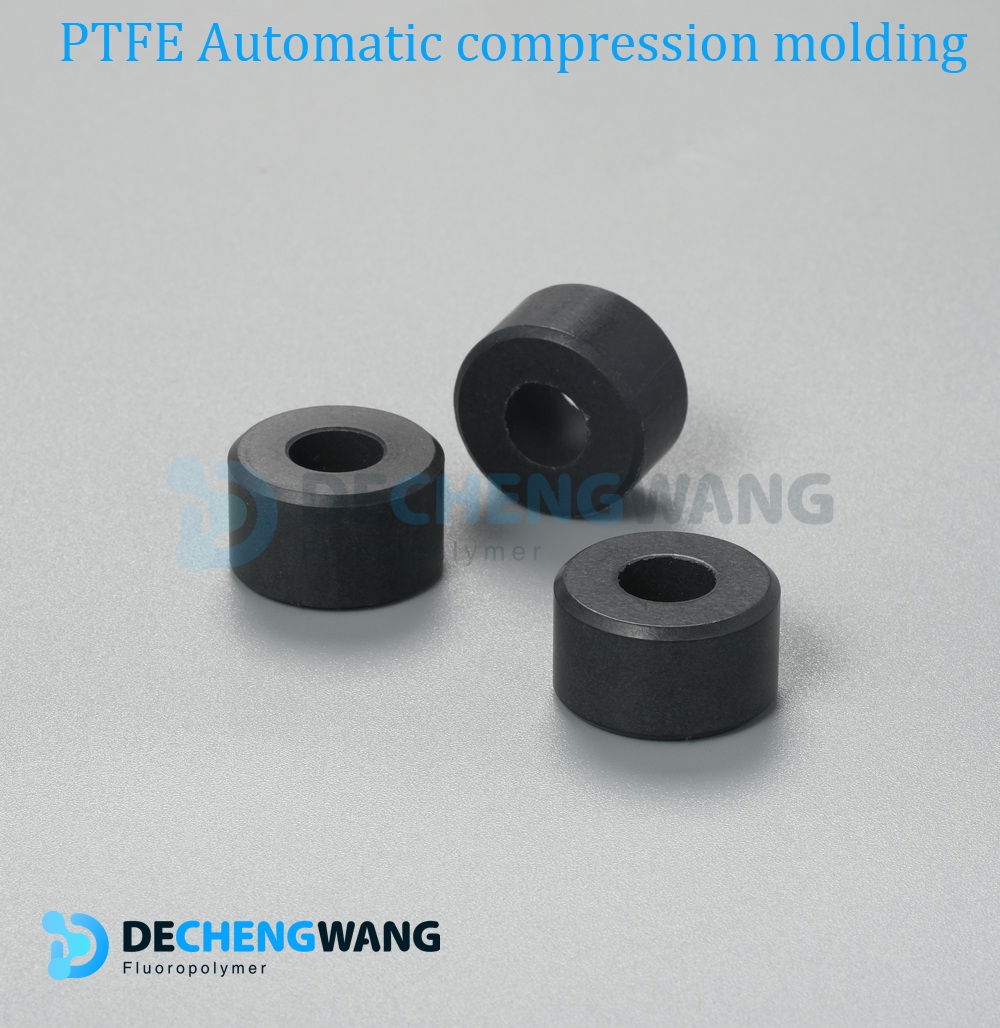
Automatic compression molding is a highly efficient and automated process specifically designed for mass production of small molded articles. It requires the use of free-flow PTFE resin, which exhibits good flowability and allows for automated charging of the powder during the molding process.
In this method, a predetermined quantity of powder is automatically filled into the mold cavity. Once filled, a ram is then lowered to compress the powder, followed by the raising of a lower ram to apply pressure to the material from both directions. This pressure is maintained for a fixed period of time. Subsequently, the upper ram is retracted, and the compressed preform is extruded using the raising action of the power ram. This entire operation follows a pre-programmed operation cycle.
Due to the short compression time in automatic molding, higher pressure is applied compared to normal compression molding.
The sintering conditions for automatic compression molding closely resemble those of normal compression molding. However, since the molded articles are smaller in size and often used as finished products without additional secondary processing such as machining, it becomes crucial to minimize any dimensional or shape changes during the sintering process.
To address this concern, the implementation of improvements such as rotary-type sintering ovens and continuous-type sintering ovens is recommended.
PTFE isostatic molding:
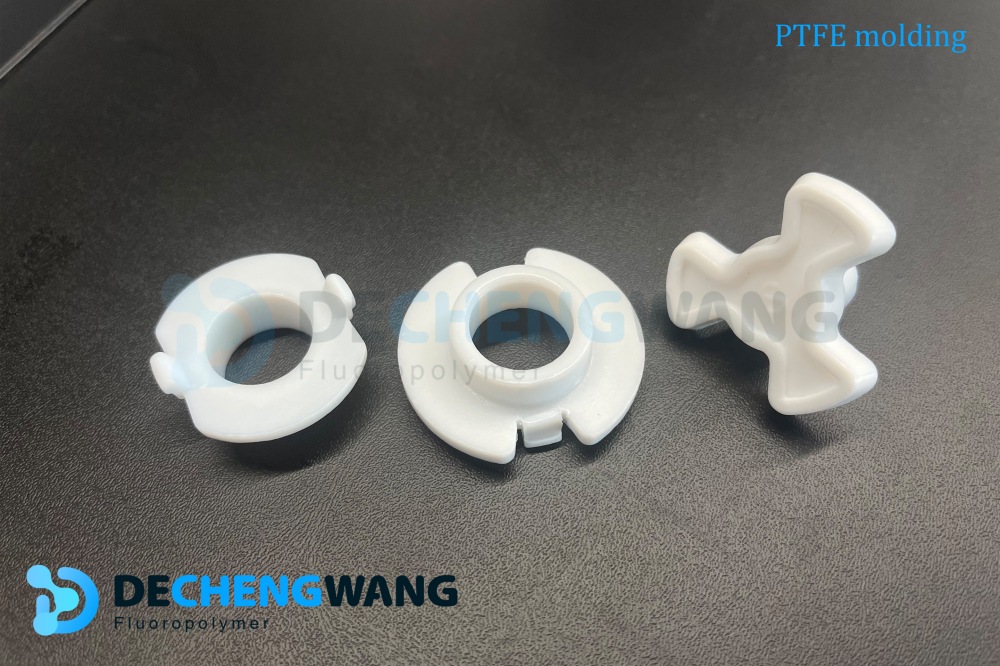
Isostatic molding is comprising charging PTFE powder between a mold and an elastic mold(for example rubber) and pressing the powder by fluid pressure (water, oil) from every direction via the elastic mold to bond the particles to each other. This method is suitable for molding articles with complex shapes, including thin-wall pipes with large diameters, beaker-shaped containers and bottles, and various piping parts.
The molding pressure typically ranges from 15 to 30 MPa in isostatic molding. During the sintering process, the surfaces in contact with the rubber mold may become rough. Additionally, PTFE tends to experience shrinkage during sintering, leading to some degree of dimensional inaccuracy in the final product. As a result, machining is often required to achieve the desired precision and finish when necessary.
PTFE manufacturing process 2 – PTFE paste extrusion:
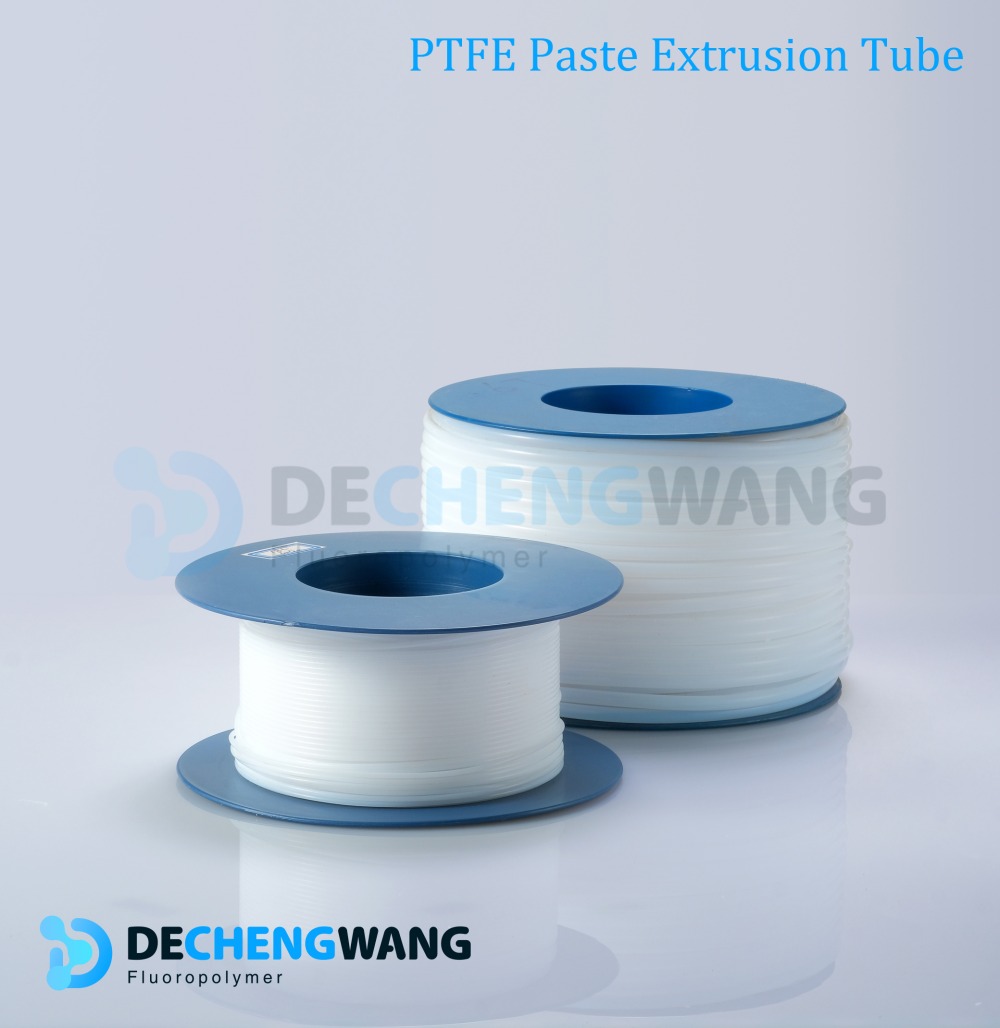
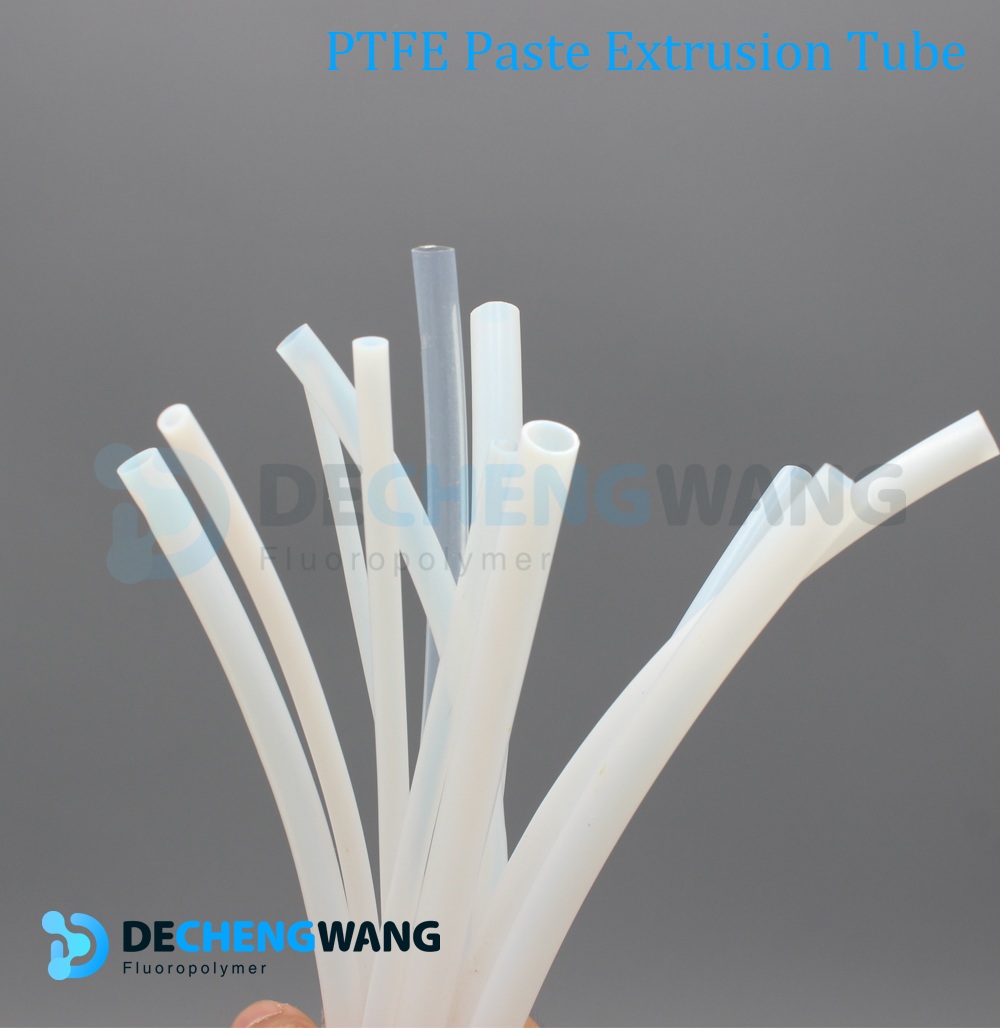
PTFE paste extrusion starts with PTFE fine powders, add a volatile lubricant to these powders, which distributes itself uniformly within the powder. This mixture becomes in fact the “paste” = powder + lubricant. Before extrusion this paste is typically compressed, to remove as much air as possible, into a cylindrical perform or “candle”. The perform is subsequently placed in a special constant rate ram extruder and the PTFE is extruded into the desired shape. Such extrusions are typically performed at powder temperatures of 35 – 50 °C. During extrusion many of the particles transform into fibrils, which give strength to the extrudate. Subsequently the extruded parts are dried to remove lubricant and then sintered at 360 to 400°C, resulting in melting and the formation of uniform, air-free objects.
Typical products made from PTFE paste extrusion are high quality hoses and wires for the aerospace and automotive industries, pipe liners and transfer hoses for corrosive materials and solvents in the chemical industry, etc.
PTFE manufacturing process 3 – PTFE Ram extrusion:
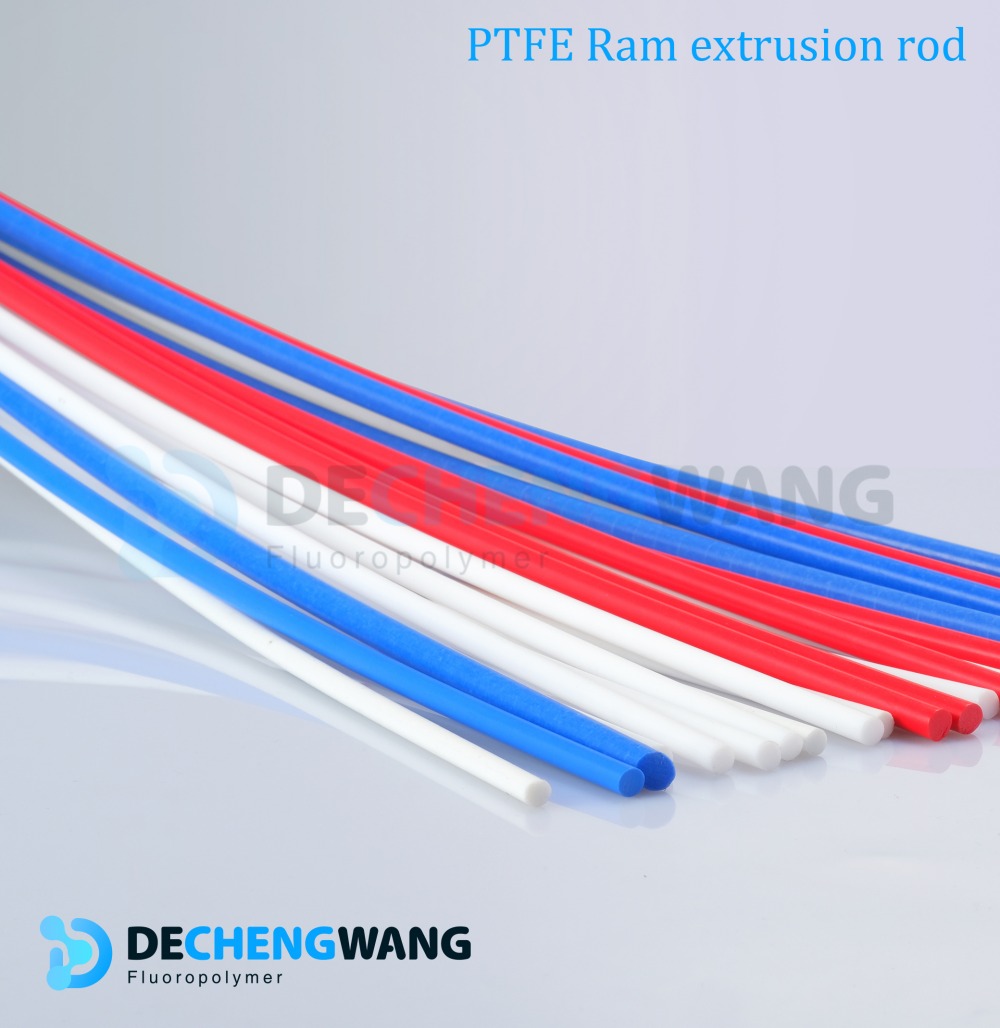
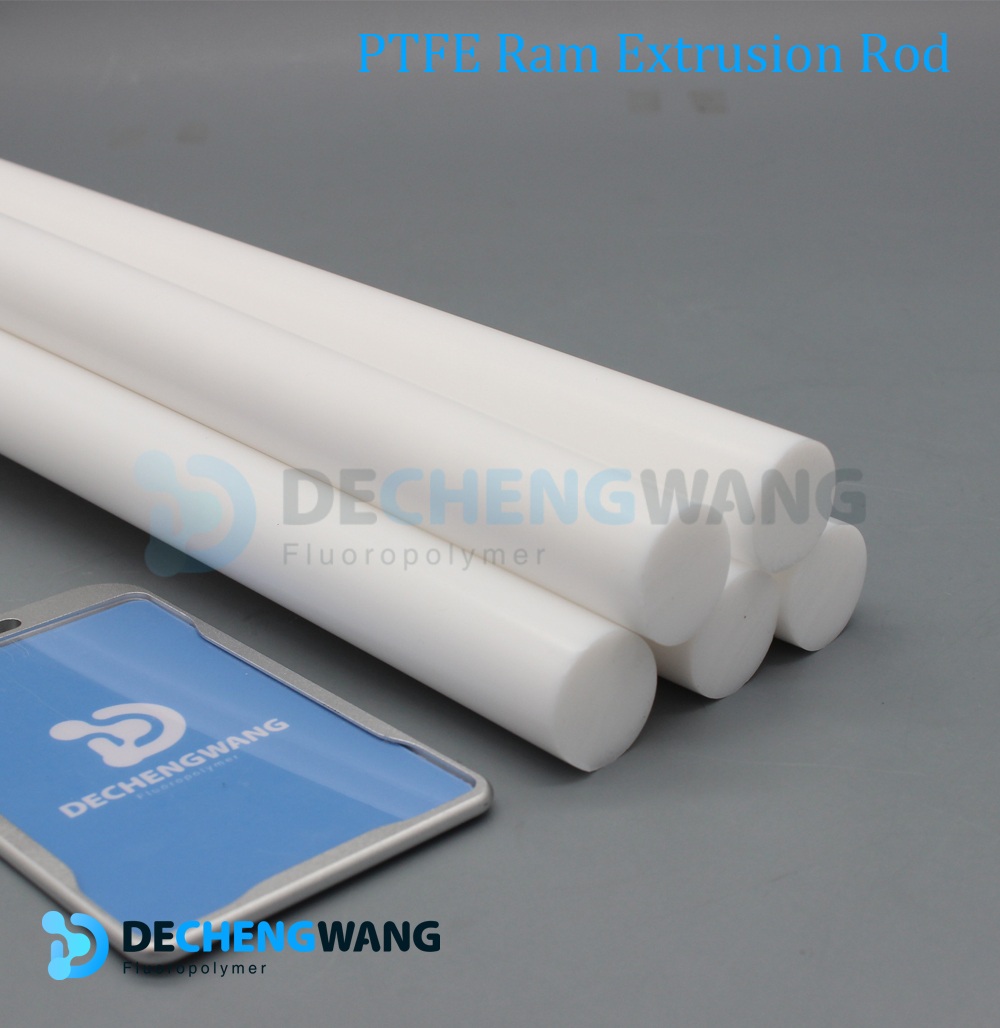
PTFE Ram extrusion is a method of operating the process to produce continues lengths of PTFE cylindrical parts (for example PTFE tube, PTFE rods) and simple profile. The compaction and sintering steps are performed simultaneously into the extruder.
To ensure efficient operation of this process, PTFE powders must exhibit good flow characteristics so that they feed readily into the extruder die tube. This is achieved by using either pre-sintered or agglomerated, both of which are free flowability.
Firstly, fed a quantity of PTFE resin into one end of a straight die tube of uniform bore where it is compacted by a ram and forced along the tube which incorporates a heated sintering zone. The ram is then withdrawn, the die tube re-charged with powder and the cycle repeated. In this way the compacted powder is forced step by step through the heated section of the die tube where it is sintered and them through a cooler section from which is emerges in a continuous length.
In general, extruded parts exhibits lower performance in comparison to compression molded parts.
PTFE manufacturing process 4 – PTFE machining:
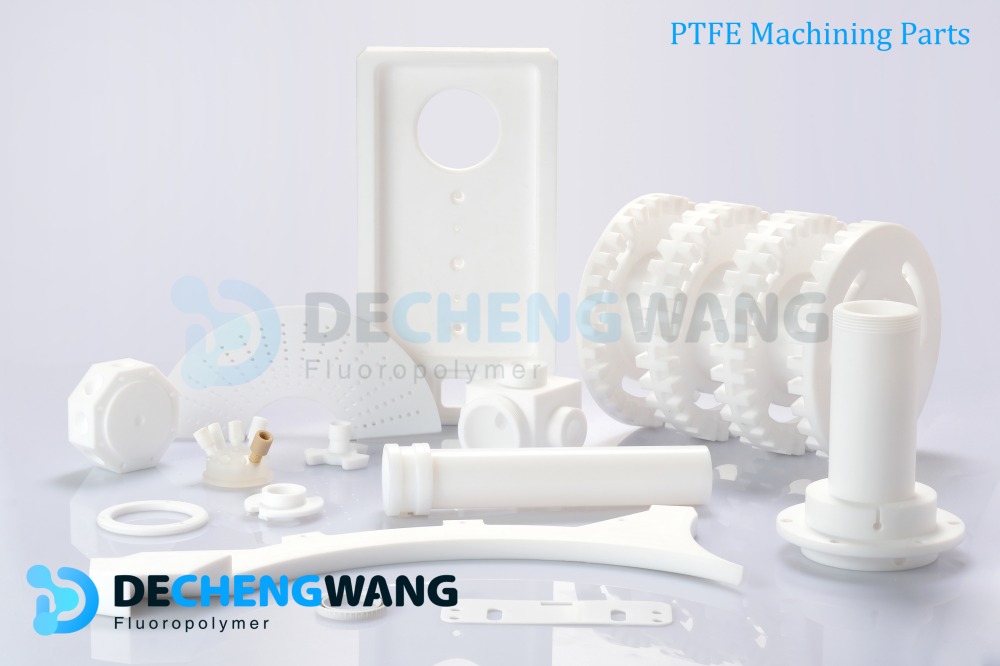
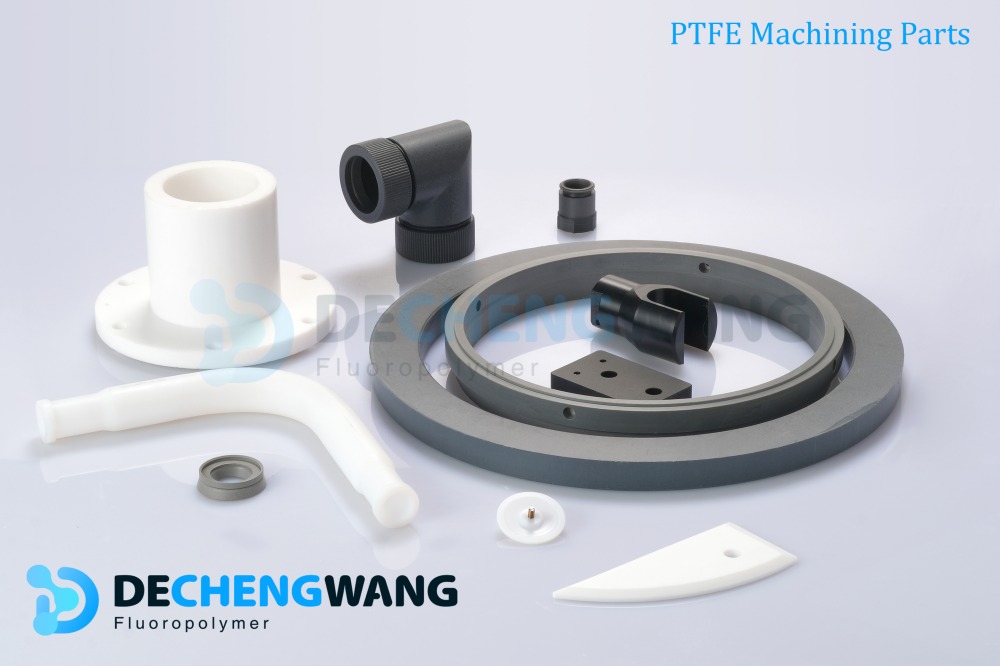
As mentioned at the beginning of this blog, PTFE cannot be injection molded or melt extruded like other thermoplastics. However, in cases where precise tolerances are required, complex product shapes are involved, or only a few prototypes are needed, machining PTFE parts emerges as a viable fabrication method.
PTFE parts can undergo all standard machining operations such as turning, facing, boring, drilling, threading, tapping, reaming, and grinding. It’s worth noting that no special machinery is needed for these processes.
When machining PTFE, whether manually or automatically, it is essential to keep in mind that its physical properties differ from those of commonly machined materials. PTFE is soft yet springy, waxy yet tough. It possesses a cutting “feel” similar to brass but has a tool-wear effect akin to stainless steel, especially for filled PTFE. However, with the expertise of a skilled machinist, machining PTFE to tolerances of +0.002 inch is easily achievable. A machinist with a strong command of PTFE’s properties and skill experience is indispensable for machining PTFE parts.
When machining parts from PTFE, following are some tips need to consider:
- tools must be kept sharp and smooth at all times,
- feed rates should be as high as possible,
- tools must have sufficient clearance so that the cutting edge only comes in contact with the plastics material,
- a good swarf removal from the tool must be assured,
- coolants should be applied for operations where plenty of heat is generated (e.g. drilling).
PTFE can be machined to produce a wide range of components, including: Manifolds, insulators, guides, slide blocks, cathode and anode end blocks, arc shields, beads, seals, washers, valve seats and many more.
At DCW, we excel at machining PTFE to achieve a burr-free and high-quality surface finish, especially in sealing areas where precision is crucial. We ensure that the components are free from dents and can mitigate any potential size changes over time through proper annealing and machining techniques. Although PTFE is relatively easy to machine due to its softness, it still requires the expertise and experience of skilled machinists to accurately produce dimensionally precise features.
PTFE manufacturing process 5 – PTFE surface etching:
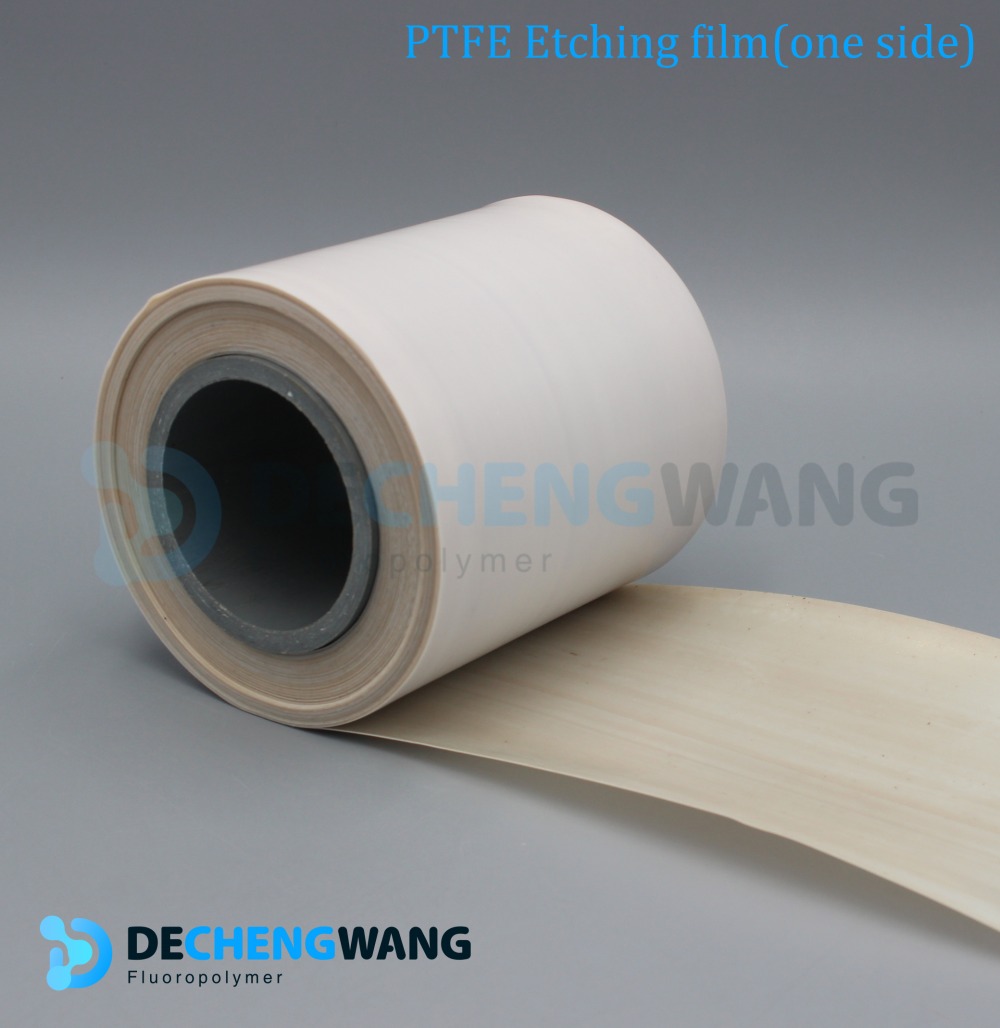
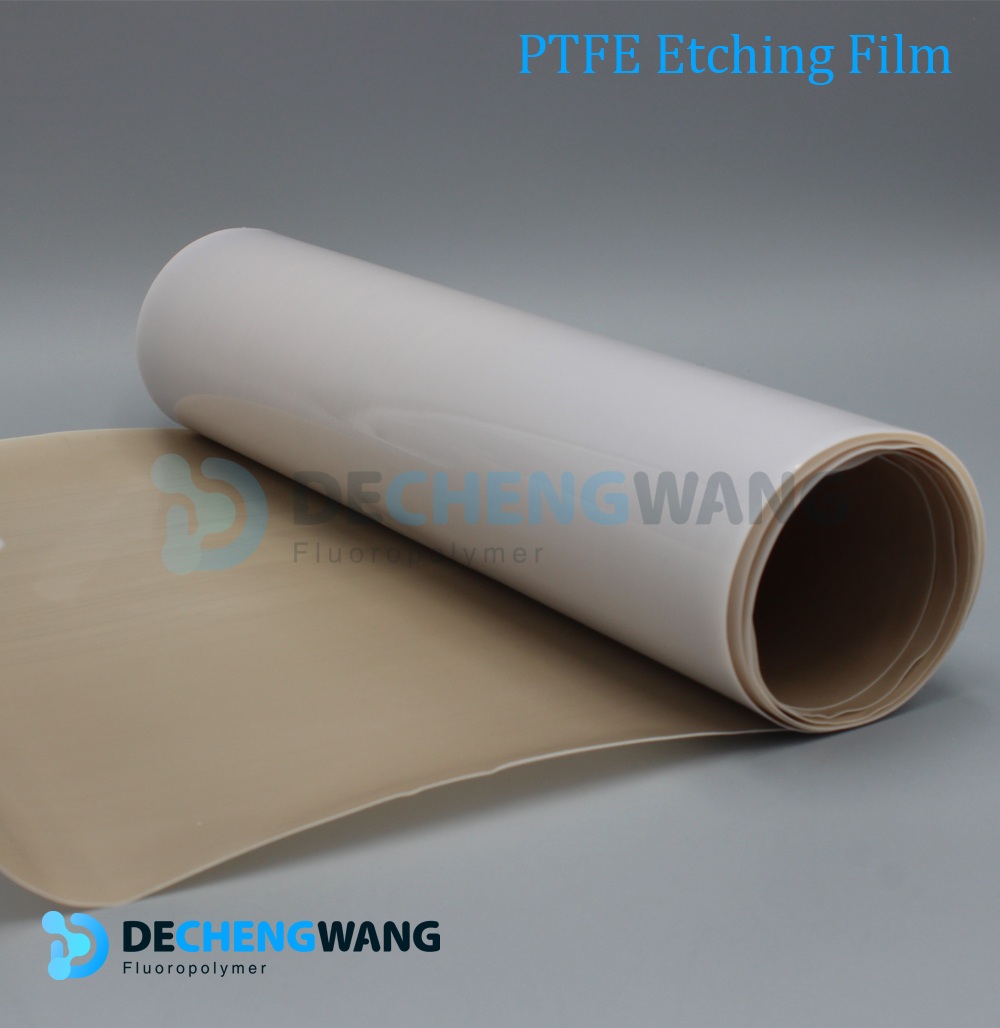
PTFE etching is a chemical process method of surface treatment, it is not a individual method to process PTFE parts.
PTFE (Polytetrafluoroethylene) is widely recognized for its exceptional non-stick properties. The non-stick characteristics of PTFE arise from its unique molecular structure. PTFE is a fluoropolymer that consists of carbon and fluorine atoms arranged in a highly stable and tightly bonded structure. This molecular arrangement creates a surface with very low surface energy, resulting in excellent non-stick properties. However, these same properties make it difficult to bond or coat the material with other substances.
Etching is a chemical procedure used to enhance the bondability of PTFE films, sheets, or finished parts with various substrates and materials. After etching treatment, the bondable side (acidated surface) of the PTFE can be readily distinguished due to its characteristic dark brown color.
PTFE manufacturing process 6 – PTFE skiving:
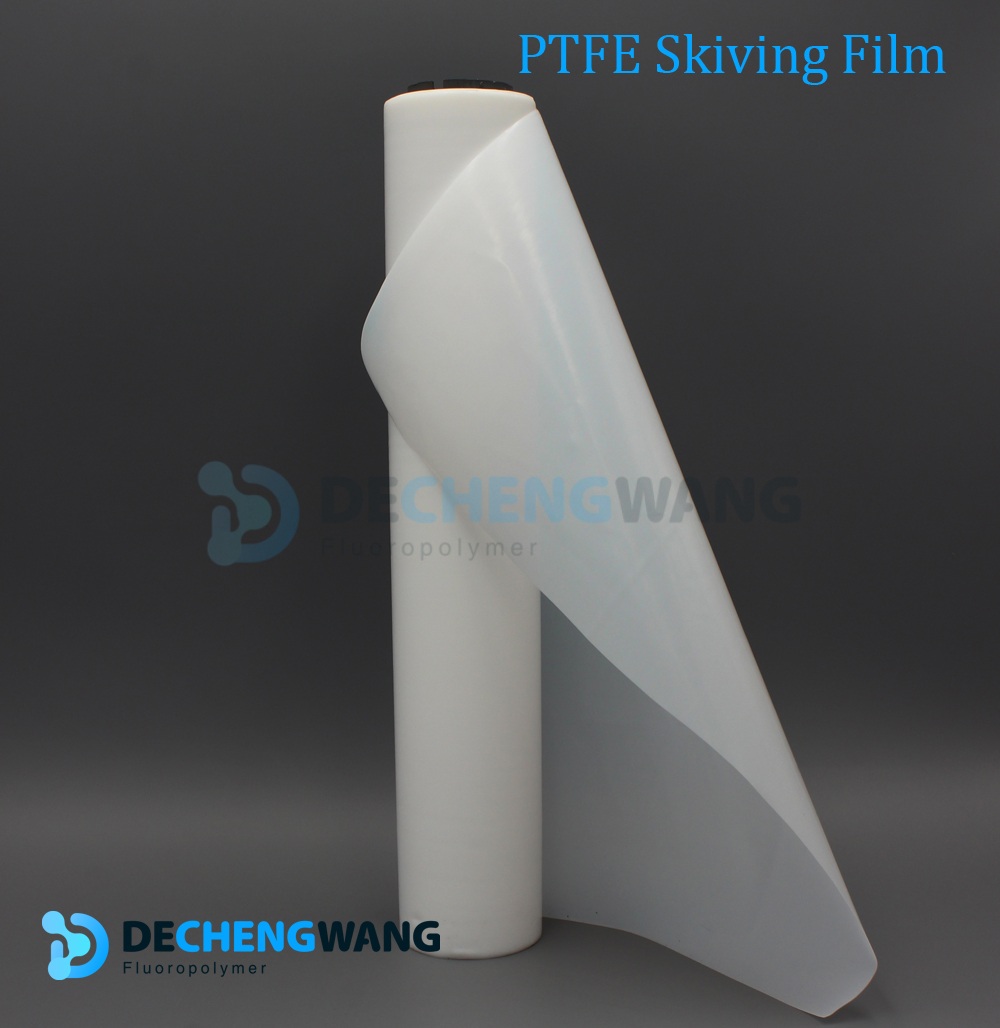
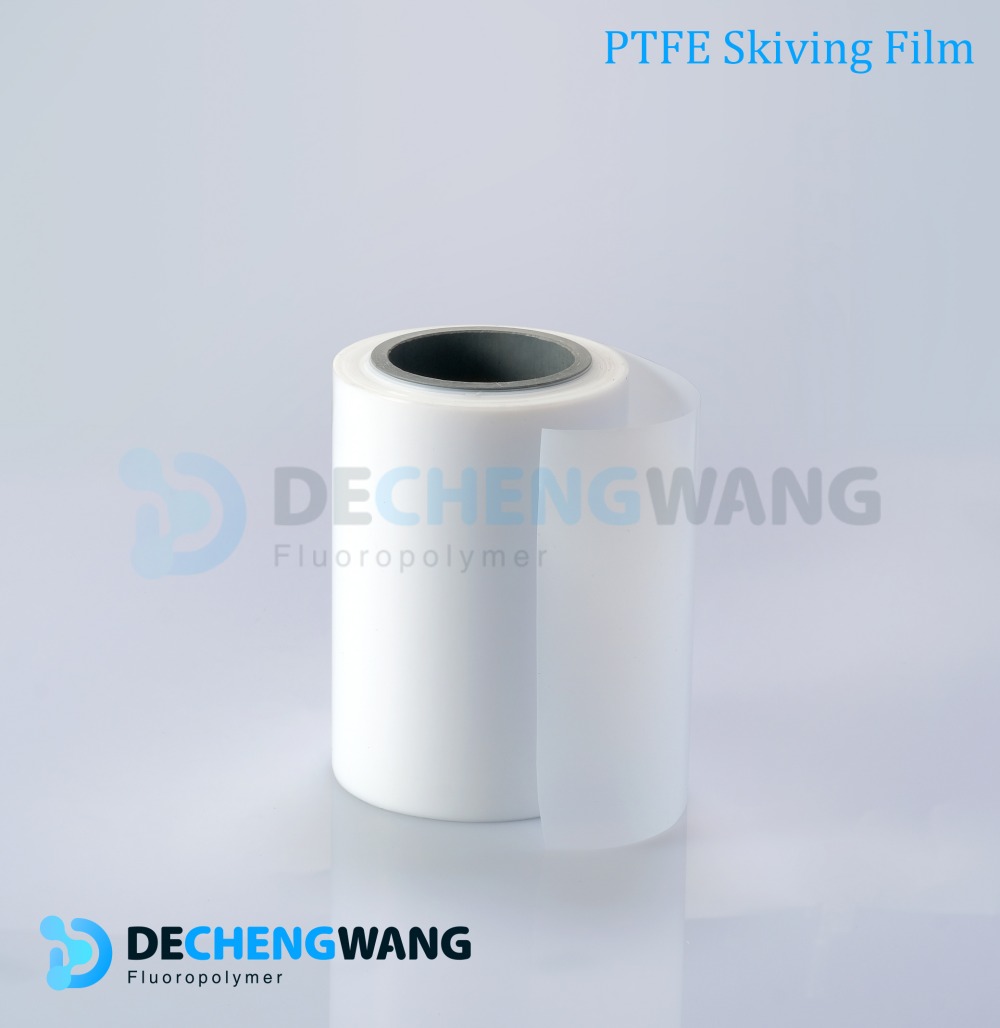
Skiving is the method used to manufacture continuous-length PTFE films in a flexible roll form. This process involves working with a sintered PTFE billet. A splined steel arbor is inserted into the PTFE billet, and the assembly is mounted on a rotary lathe, specifically designed for skiving. The lathe rotates at a speed of approximately 20-30 RPM.
To initiate the skiving process, a cutting blade is mounted on a rigid cross slide, which is then advanced towards the billet at a consistent speed. This advancement peels off a continuous PTFE film of uniform thickness. By adjusting the speed of the advancing cross slide on the rotating PTFE billet/steel arbor assembly, films of varying thicknesses ranging from 0.03mm to 4mm can be skived off.
This skiving method allows for the production of PTFE films with different thicknesses, providing flexibility and versatility in meeting various application requirements.
PTFE manufacturing process 7 – PTFE punching:
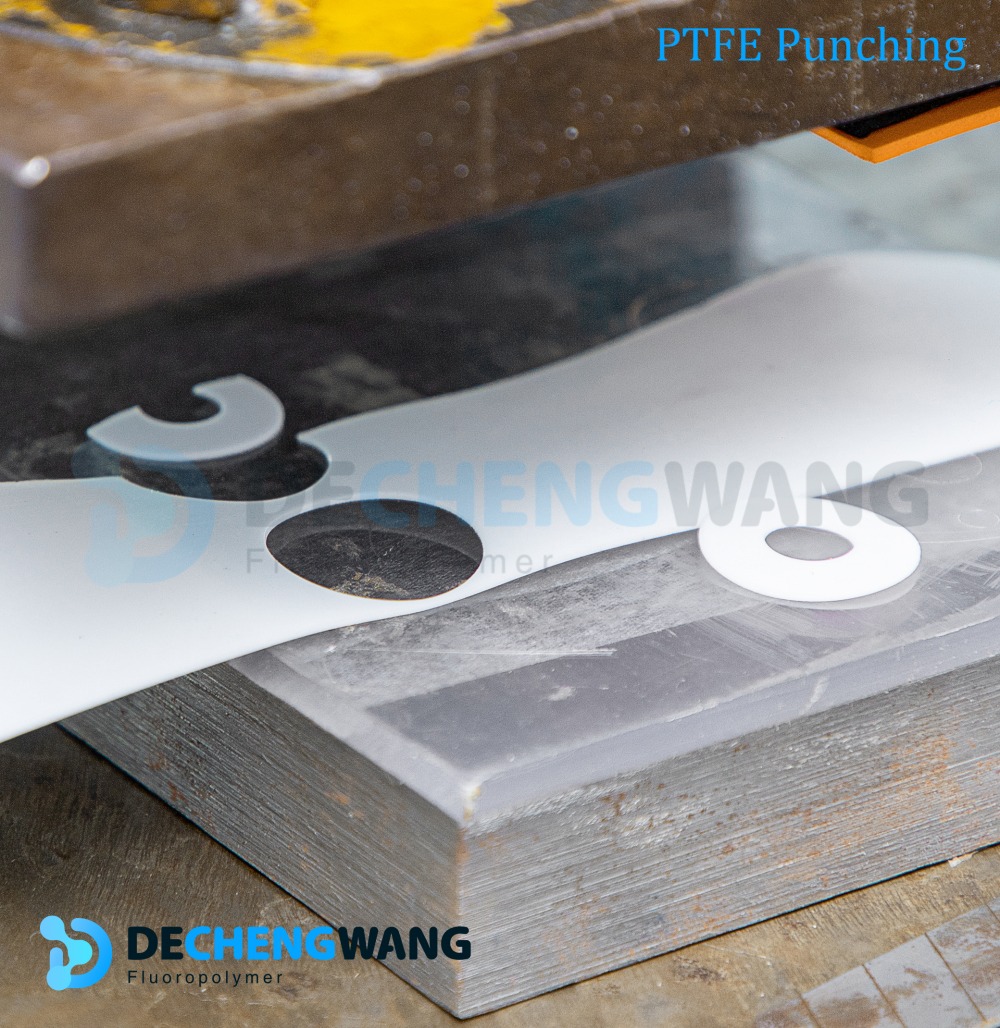
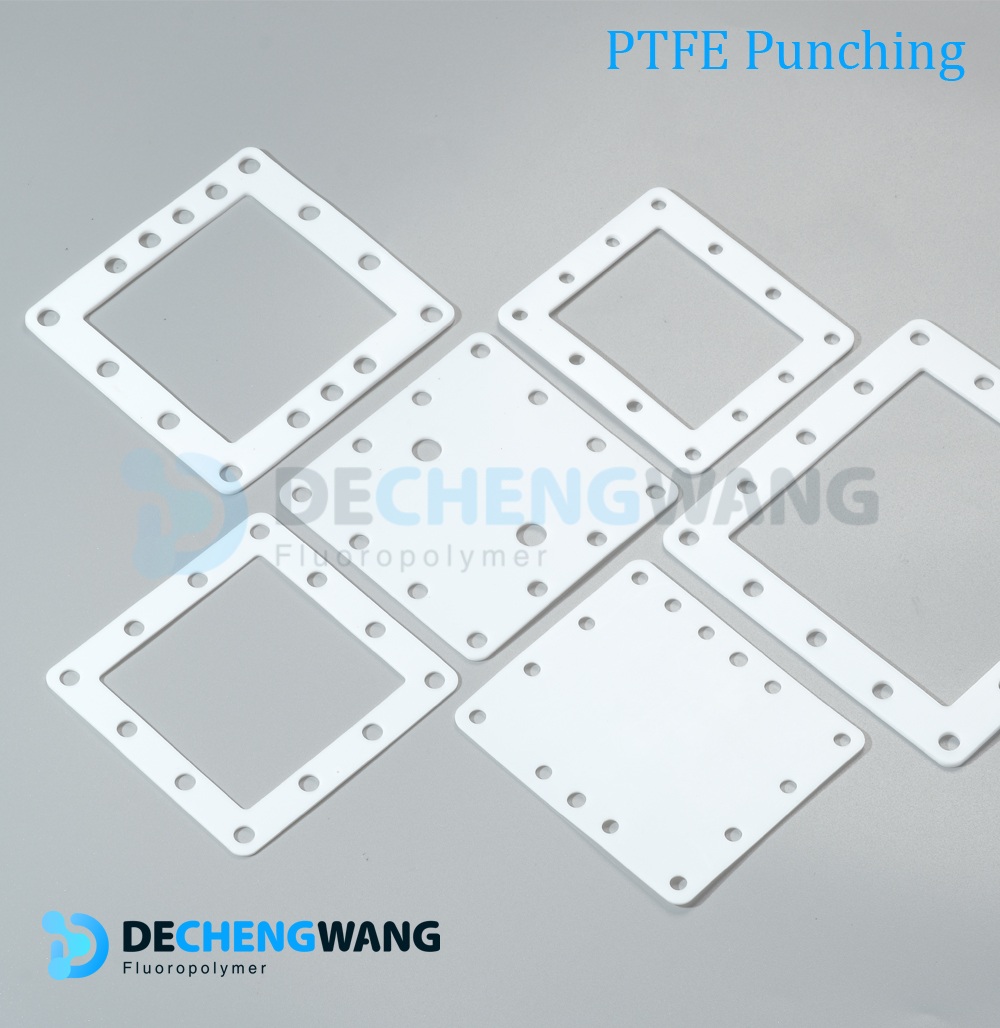
Punched parts are produced from sheet, tape and film in such diverse materials as ePTFE, standard PTFE, FEP, PFA, PVDF. Our punched product portfolio mainly comprises of custom flat round and rectangular gaskets using precision knife tooling to ensure cleanly finished articles.
PTFE manufacturing process 8 – PTFE coating:
PTFE coating refers to the process of applying a layer of PTFE (polytetrafluoroethylene) to various items. This coating typically involves the application of two coats, a primer coat followed by a top coat. The purpose of PTFE coating is to provide the coated surface with desirable properties such as low friction, corrosion resistance, or dry lubrication.
Before applying the PTFE coating, proper preparation of the item is essential. This can involve degreasing or blasting the material, depending on its specific requirements. After preparation, the coating process takes place, followed by heating the coated item in an oven to create a dry and durable coating. The thickness of the PTFE coating typically ranges from 15 to 35 microns, depending on customer specifications and the number of coats applied.
It’s important to note that there are different grades of PTFE coating available, tailored to specific applications. For example, a food-grade coating would have different application requirements compared to an industrial-grade coating.
Conclusion:
The journey from PTFE resin to finished parts involves various manufacturing processes, each tailored to achieve specific shapes, sizes, and properties. Whether it’s compression molding, ram extrusion, isostatic molding, skiving, or surface modification through etching, each technique contributes to the versatility and functionality of PTFE materials. These manufacturing processes enable the production of a wide range of PTFE components, empowering industries with innovative solutions for their diverse applications.
PTFE’s remarkable properties combined with the ingenuity of manufacturing processes make it an indispensable material in countless industries. From sealing solutions and electrical insulation to lubrication systems and medical.