Seals are one of the most important components of mechanical systems used for covering fluids and gases. They are used in a wide variety of applications, from simple devices like O-rings used in everyday objects to complex seals used in industrial machinery and equipment. Seals are typically made from a variety of materials, each with its own unique properties and advantages.
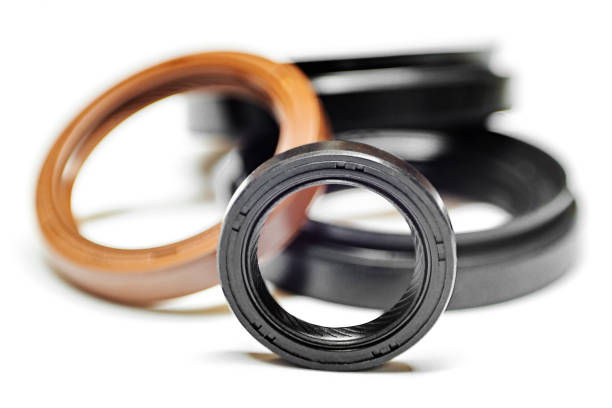
In this article, we will explore the world of seals and delve into the various materials used to make them. We will discuss the factors to consider when choosing seal types and the different types of sealing materials, highlighting their distinct features and preferred applications.
Let’s dive right into it!
What is Seal
A seal is a device used to prevent the leakage of fluids or gasses between two surfaces. Seals are designed to create a barrier between two parts of a machine or system to prevent the escape of fluids or gases, or to prevent the entry of contaminants into the system.
They can take many forms, including O-rings, gaskets, packings, lip seals, and mechanical seals, and they are used in a wide variety of applications, from automobiles and appliances to heavy machinery and industrial equipment. The type of seal used depends on the application and the operating conditions, such as temperature, pressure, and the type of fluid or gas being sealed.
What are the Requirements for Choosing Sealing Materials
When choosing seal materials, there are several factors to consider to ensure that the seal is capable of functioning optimally, even when exposed to extremely harsh conditions. Below are the requirements for evaluation.
Good Air-tightness and Water-tightness
Choosing a sealing material with good air-tightness and water-tightness is essential for preventing the leakage of fluids and gases in a mechanical system. The material must be strong and tough to resist the inflow and outflow of air or water. The main factors to consider when selecting a material with good air-tightness and water-tightness are its physical properties, such as hardness, flexibility, and resilience.
A good type of seal material that possesses these characteristics is fluorocarbon rubber. It’s highly resistant to oils, fuels, solvents, and harsh chemicals, making it ideal for use in applications that require resistance to air and water.
Excellent Bonding Performance
The bonding performance of a seal material is crucial for ensuring that the seal remains in place and does not become dislodged during operation. The material must be able to bond well to the surfaces it is sealing against, as well as any adhesives or coatings used to secure it in place.
Factors that influence bonding performance include the surface finish of the sealing surfaces, the type of adhesive used, and the curing conditions. The surface finish should be clean and free of contaminants, and the adhesive used should be compatible with both the sealing material and the surfaces being bonded. Furthermore, curing conditions must be properly controlled to ensure that the adhesive cures completely and that the bond strength meets the requirements of the application.
A seal material such as acrylonitrile-butadiene-elastomer is commonly used for its excellent bonding properties and ability to adhere to a wide variety of surfaces. It’s an oil seal material that’s highly resistant to oils, solvents, and fuels, which makes it ideal for sealing applications in which the seal must remain in place under extreme conditions.
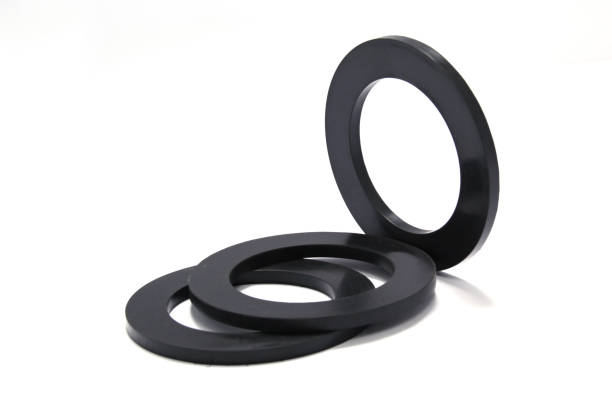
Heat Resistance and Aging Resistance
Another requirement that must be met is the capability to withstand high temperatures and resist degradation over time to ensure reliable and long-lasting seals. Factors that influence this include the chemical composition, molecular structure, and the operating conditions of the system in which they are used.
Proper selection among the types of seal materials with excellent heat resistance and aging resistance can significantly extend the life of the seal and improve overall reliability. Commonly used materials for sealing applications requiring heat resistance and aging resistance include silicone elastomer, fluorocarbon rubber, and polytetrafluoroethylene (PTFE).
Silicone rubber is used for high temperature sealing and UV radiation, which makes it ideal for outdoor sealing applications that are exposed to sunlight. Fluorocarbon rubber offers excellent heat resistance and chemical resistance, making it ideal for sealing applications in harsh chemical environments. PTFE is highly resistant to high temperatures and chemical attacks, making it ideal for sealing applications in which the seal is exposed to aggressive chemicals or high temperatures.
Certain Elasticity and Plasticity
Sealing materials must have a certain degree of elasticity and plasticity to allow them to conform to irregular surfaces and maintain a reliable seal over time. Materials with low elasticity and plasticity are more likely to fail due to cracking, tearing, or deformation, which can compromise the integrity of the seal.
Rubber materials such as nitrile rubber, silicone rubber, and neoprene are commonly used for sealing applications due to their high elasticity and plasticity. These materials can withstand a wide range of deformation and can maintain their shape and seal effectively over long periods. Additionally, these materials have a high degree of flexibility, which allows them to conform to irregular surfaces and maintain a reliable seal even in high-stress applications.
Superior Tension-compression Cycling Performance
Lastly, the seal materials must be able to withstand repeated cycles of tension and compression without experiencing significant degradation or failure. Factors that influence this include the chemical composition, molecular structure, and operating conditions of the system in which they are used. Materials that have this requirement can maintain their sealing properties over many cycles, ensuring that the sealed system remains leak-free and operates effectively.
Materials such as silicone rubber and fluorocarbon elastomers are known for their superior tension-compression cycling performance, as they can withstand a high degree of deformation and are highly resistant to fatigue. Additionally, these materials offer excellent chemical resistance, which allows them to maintain their shape and seal effectively even in harsh chemical environments.
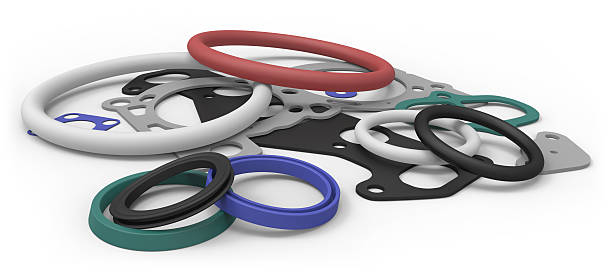
What are the Different Types of Sealing
Depending on the specific applications, sealing material manufacturers make use of various materials in producing high-quality seals that are capable of functioning optimally under severe conditions.
FKM/FPM – Fluorocarbon Rubber
Fluorocarbon rubber, also known as FKM or FPM, is a synthetic elastomer with excellent chemical resistance and high-temperature performance. FKM materials are highly resistant to oils, fuels, oxygen, ozone, solvents, and chemicals, making them ideal for use in applications that require resistance to aggressive media. Additionally, FKM materials have a wide operating temperature range of -20°C to +200°C, making them suitable for high-temperature applications.
These types of seals are commonly used in sealing applications for the automotive, aerospace, and chemical processing industries. They are also highly resistant to compression sets and have good tensile strength, making them ideal for dynamic sealing applications.
EPDM – Ethylene-Propylene-Diene-Rubber
Ethylene-Propylene-Diene-Rubber, or EPDM, is a synthetic rubber with excellent weathering resistance, good electrical insulation properties, ozone resistance, and low-temperature performance.
EPDM materials are highly resistant to water, steam, and oxidation, making them ideal for use in outdoor applications that are exposed to weathering and environmental factors. Additionally, EPDM materials have a wide operating temperature range of -40°C to +160°C, making them suitable for low-temperature applications.
EPDM sealing type materials are commonly used in sealing applications for the automotive, construction, and marine industries. They also have good resistance to compression sets and excellent sealing performance in water and steam environments.
FFKM/FFPM – Perfluoroelastomer
Perfluoroelastomers, also known as FFKM or FFPM, are synthetic elastomers with excellent chemical resistance, high-temperature performance, and low compression set. FFKM materials are highly resistant to aggressive chemicals, acids, and solvents, making them ideal for use in harsh chemical environments. Additionally, these sealing types have a wide operating temperature range of -20°C to +320°C, making them suitable for extreme high-temperature applications.
It is similar to Polytetrafluoroethylene (PTFE), as it’s a combination of the elasticity and sealing strength of an elastomer with the chemical resistance of PTFE. However, this type of seal does not have creep behavior or permanent deformation like PTFE seals.
FFKM materials are commonly used in sealing applications for the semiconductor, chemical processing, and aerospace industries. They also have excellent mechanical properties, including high tensile strength and low compression set, which makes them ideal for dynamic sealing applications.
VMQ – Silicone-Elastomer
Silicone elastomers, also known as VMQ, are synthetic elastomers with excellent high-temperature performance, low compression set, and good electrical insulation properties. Silicone materials are highly resistant to extreme temperatures, UV radiation, and ozone, making them ideal for use in outdoor applications that are exposed to environmental factors.
They are easily recognized by their broad range of thermal application. The good cold flexibility, ozone resistance, and dielectric properties are additional properties that set them apart from the other different types of seal materials. Additionally, VMQ materials have a wide operating temperature range of -60°C to +250°C, making them suitable for extremely high-temperature applications.
VMQ materials are commonly used in sealing applications for the automotive, aerospace, and medical industries. They also have good resistance to compression sets and are highly resistant to aging and weathering, making them ideal for long-term sealing applications.
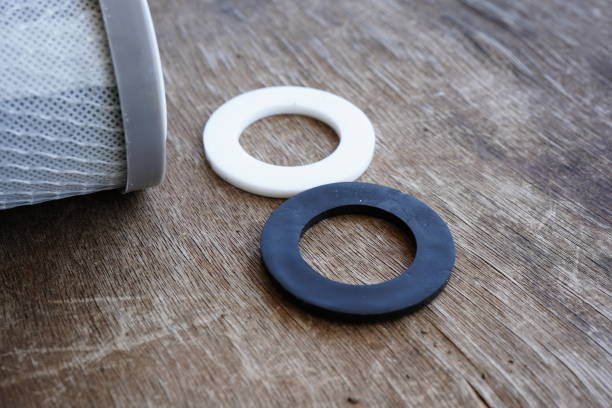
NBR – Acrylonitrile-Butadiene-Elastomer
Acrylonitrile-Butadiene-Elastomer, which is also known as NBR, is a synthetic elastomer with excellent oil and fuel resistance. NBR materials are highly resistant to hydraulic oils, oil in aqueous emissions, mineral oils, animal & vegetable oils, benzene, water glycols, fuels, and other hydrocarbons, making them ideal for use in sealing applications in the automotive and oil & gas industries. The working temperature range is between -40°C to +100°C, making them suitable for moderate temperature applications.
NBR sealing materials are commonly used in sealing applications for engines, pumps, and hydraulic systems. They are known for their excellent oil and fuel resistance, good tensile strength, resistance to compression set, and good abrasion resistance.
PTFE – Polytetrafluoroethylene
Polytetrafluoroethylene (PTFE), which is otherwise known as Teflon, is a synthetic material with excellent chemical resistance and low friction properties. Teflon sealing is highly resistant to almost all chemicals, making them ideal for use in sealing applications that require resistance to aggressive media. Additionally, these seal materials have a wide operating temperature range of -200°C to +260°C, making them suitable for extreme temperature applications.
PTFE seals are FDA-compliant and non-toxic in pure form, making them suitable for arguably all industries. PTFE applications include chemical processing, food and beverage, and pharmaceutical industries. They are also known for their excellent electrical insulation properties, making them ideal for use in electrical sealing applications.
You May Also Interest in: >> What is PTFE: Everything You Need to Know
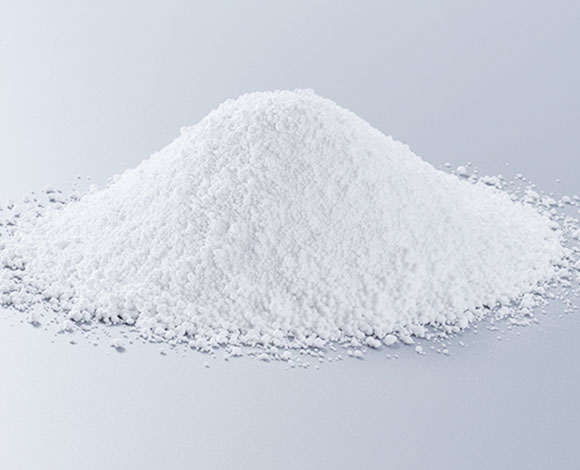
PEEK – Polyetheretherketone
Polyetheretherketone (PEEK), is a high-performance thermoplastic with excellent mechanical and thermal properties. PEEK materials are highly resistant to high temperatures, aggressive chemicals, water vapor, hydrolysis, fuels, alcohols, grease, oils, alkalis, and wear, making them ideal for use in sealing applications that require resistance to extreme environments.
Additionally, PEEK materials have a wide operating temperature range of -60°C to +250°C, making them suitable for extreme temperature applications.
PEEK materials are commonly used in sealing applications for the aerospace, automotive, and chemical processing industries. They also have good dimensional stability and excellent creep resistance, making them ideal for use in high-performance dynamic sealing applications.
At DCW, we specialize in making use of PTFE and PEEK sealing materials, coupled with our unmatched manufacturing capabilities to produce high-quality seals for different applications. With due diligence in making OEM and unique seals that appeal to each need, we design and produce tough and durable seals that function maximally and last the test of time.
Also Read: >> PTFE VS PEEK: What’s The Difference and Which is Better
DECHENGWANG: Fluoropolymer Expert Offers High-quality Seals
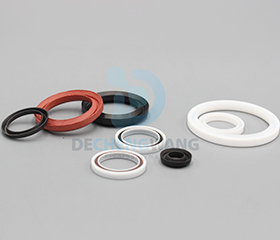
As a leading specialist in the fluoropolymer field, we serve as a one-stop solution provider catering to all seal needs. Having over a decade of professional experience with different industry requirements and continuous in-house research about ultra-high-strength thermoplastic composite materials, we help produce the best sealing material that suits every demand, even those with the most demanding application specifications.
The seals are available in a rich variety and good quality, with outstanding intrinsic properties like corrosion resistance, high purity, high temperature resistance, chemical resistance, etc. They are produced in compliance with quality management standards, including the IATF 16949 and ISO 9001 quality system, combined with various machining techniques that make them suitable with all applications and superior to other options in the market.
Our services are tailored to your requirements and industry, whether aerospace, automotive, mechanical engineering, oil & gas, food processing, medical engineering, and chemical plants. Contact us for all your seal needs, including the right material selection, precise production, reliable supply, etc.
Conclusion
The importance of selecting the right seal material from different types of sealing cannot be overemphasized if the sealing system must work appropriately over a long time. To choose the best among the different types of seal materials, different factors must be considered, which includes good air-tightness & air-tightness, excellent bonding performance, heat resistance & aging resistance, certain elasticity & plasticity, and superior tension-compression cycling performance.
DECHENGWANG provides a wide variety of other compression molded and precision-machined components, such as bellows, ball valve seats, rings, insulators, guide rings, labware, and bushings. These components are highly-functional across several industrial applications, including chemical, food & beverage, aerospace, automotive, electronics & semiconductors, mechanical engineering, and oil & gas.