Fluoroplastics are a class of high-performance plastics that are known for their exceptional chemical resistance, low coefficient of friction, and excellent electrical insulation properties. They are widely used in a variety of industries, including chemical processing, electronics, automotive, aerospace, and medical devices.
There are six main types of fluoroplastics, each with its unique set of properties and applications. These include polytetrafluoroethylene (PTFE), fluorinated ethylene propylene (FEP), perfluoro alkoxy (PFA), ethylene tetrafluoroethylene (ETFE), polychlorotrifluoroethylene (PCTFE), and polyvinylidene fluoride (PVDF).
In this detailed introduction, we will explore each of these types of fluoroplastics in-depth, discussing their properties, application areas, advantages, as well as their disadvantages. Whether you are a materials scientist, an engineer, or a product designer, this guide will provide you with valuable insights into the world of fluorinated plastic.
What is fluoroplastics and Fluoroplastics’ Properties
This subsection provides an overview of fluoroplastics, a type of high-performance plastic. It explains their unique features and properties, including their resistance to heat, chemicals, and friction. Let’s begin by looking at what fluoroplastics are and their industrial properties.
The Definition of Fluoroplastics
Fluorinated plastic is a group of synthetic materials that are known for their unique combination of properties, including their non-stick and low-friction properties, high resistance to heat, chemicals, and corrosion, as well as excellent electrical and thermal insulation properties. They are made up of long-chain molecules containing carbon and fluorine atoms, which provide their exceptional properties.
Fluoropolymers have a low coefficient of friction, and a high melting point, and are generally inert and non-toxic. Due to their excellent properties, they are widely used in various industries, such as chemical processing, electronics, aerospace, and medical devices. Despite being relatively expensive and difficult to process, the exceptional properties of fluoroplastics make them a highly desirable material for many applications.
Common Properties of Fluoroplastics
Now, let us look at the general properties of different kinds of fluoroplastics:
General Properties
Fluorinated plastic is known for its excellent chemical resistance, low coefficient of friction, and high melting point, which allow them to withstand a wide range of temperatures, typically from -200°C to 260°C. They are non-combustible and have low absorption rates for most chemicals, making them ideal for use in harsh environments and applications that require high purity.
Thermal Properties
With a high melting point, typically above 327°C, they exhibit low coefficients of thermal expansion, which allow them to maintain their dimensional stability over a wide temperature range. They have low thermal conductivity, which makes them excellent insulators, and their thermal properties are largely unaffected by exposure to chemicals or moisture.
Mechanical Properties
They exhibit remarkable mechanical properties, such as high tensile strength and excellent hardness. They are known for their exceptional resistance to wear, deformation, and fatigue, making them ideal for use in demanding applications where durability is critical. Their unique molecular structure also allows them to maintain their mechanical properties in extreme temperatures and harsh chemical environments.
Electrical Properties
Fluoro plastics possess exceptional electrical properties that make them highly sought after in the electrical and electronics industries. They exhibit low dielectric constant and high dielectric strength, which means they can withstand high voltages without breaking down or losing their insulating properties. Their high purity and chemical resistance also make them ideal for use in high-performance electrical applications where reliability and safety are critical.
Most Common Fluoroplastic Materials and Their Characteristics
Having discussed the general characteristics of fluoropolymers, let us dive into the specific characteristics of the six types of fluoroplastics that exist.
PTFE – Polytetrafluoroethylene
PTFE, or polytetrafluoroethylene, is a synthetic fluoropolymer that is renowned for its unique combination of properties. It is highly resistant to chemicals, UV radiation, and extreme temperatures, with a melting point above 327°C. It is also non-stick, non-toxic, and has a low coefficient of friction, making it ideal for use in applications where easy release is required. It is commonly used in the manufacturing of industrial gaskets, seals, bearings, and other critical components.
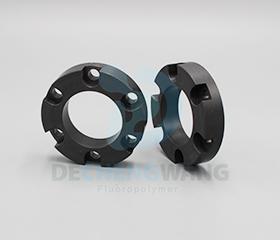
Also, it is also used in the production of non-stick cookware and as a coating for medical implants. Its high purity and chemical resistance make it suitable for use in semiconductor manufacturing and in the chemical and pharmaceutical industries. PTFE is a versatile material that can be molded, machined, or extruded into a wide range of shapes and sizes to suit various applications.
PTFE Compounds
PTFE compounds are specialized formulations of PTFE that have been modified to enhance specific properties or add new ones. They can be combined with other materials such as glass, carbon, or bronze to create composites with unique mechanical or thermal properties. PTFE compounds can also be blended with fillers such as graphite, molybdenum disulfide, or carbon fibers to enhance their lubricating properties, wear resistance, or thermal conductivity.
These compounds are commonly used in applications that require high wear resistance, low friction, or excellent chemical resistance. Examples include bearings, seals, and PTFE bushings used in the automotive and aerospace industries, as well as components used in chemical processing equipment, medical devices, and semiconductor manufacturing. The properties of PTFE compounds can be tailored to suit specific application requirements, making them a versatile option for a wide range of industries.
PEEK – Polyetheretherketone
PEEK, or polyetheretherketone is a high-performance thermoplastic that is known for its excellent mechanical, thermal, and chemical properties. It has a high melting point of around 343°C and can withstand continuous use at temperatures up to 250°C. It is highly resistant to wear, fatigue, and chemicals, and has a low coefficient of friction, making it ideal for use in applications that require high durability and reliability.
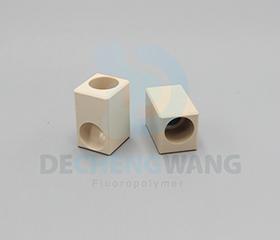
It is commonly used in aerospace, automotive, and medical applications, such as bearings, seals, pumps, and electrical components. In addition, it is used in the oil and gas industry, as well as in chemical processing, due to its resistance to harsh chemicals and corrosive environments. PEEK is a versatile material that can be easily machined or molded into complex shapes and sizes, making it a popular choice for a wide range of applications.
PFA
PFA, or perfluoroalkoxy, is a type of fluoropolymer that shares many of the same properties as PTFE, such as excellent chemical and thermal resistance. However, PFA is a more flexible and transparent material that can be melt-processed and has better electrical insulation properties. PFA has a high melting point of around 302°C and can withstand a wide range of chemicals, making it ideal for use in harsh environments.
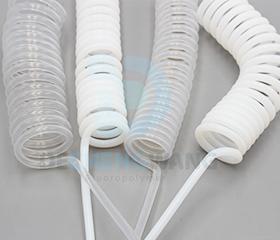
In the semiconductor industry, it is used for manufacturing processes involving high temperatures and corrosive chemicals, as well as in the production of medical tubing and components due to its high purity and biocompatibility. PFA is also used in the chemical processing industry for manufacturing equipment, such as lined pipes, tanks, and valves, due to its resistance to harsh chemicals and high temperatures. It is a versatile material that can be molded, extruded, or coated to suit a wide range of applications.
PVDF
PVDF, or polyvinylidene fluoride, is a high-performance thermoplastic that exhibits excellent chemical and UV resistance, as well as high mechanical strength and toughness. It has a high melting point of around 177°C and can withstand continuous use at temperatures up to 150°C. PVDF is highly resistant to abrasion, impact, and weathering, making it ideal for use in outdoor applications.
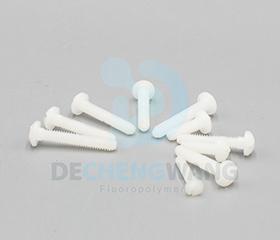
The chemical and petrochemical industries use it for manufacturing equipment such as pipes, tanks, and valves due to its resistance to harsh chemicals and solvents. PVDF is also used in the electrical and electronics industries for insulation and wiring applications due to its high dielectric strength and low dielectric constant. It is a versatile material that can be easily fabricated and welded, and its unique properties make it a popular choice for a wide range of applications.
PCTFE – Polychlorotrifluoroethylene
PCTFE, or polychlorotrifluoroethylene, is a highly crystalline thermoplastic that exhibits excellent chemical resistance, low permeability to gases, and high dielectric strength. It has a high melting point of around 215°C and can withstand continuous use at temperatures up to 150°C. PCTFE is highly resistant to a wide range of chemicals, including acids, bases, and solvents, making it ideal for use in chemical processing applications.
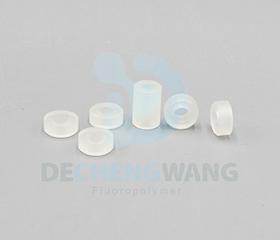
In the aerospace industry, it is used for manufacturing components such as valves, gaskets, and bearings due to its high strength and low friction coefficient. It is also used in the electrical and electronics industries for insulation and wiring applications due to its high dielectric strength and low dielectric constant. It is a versatile material that can be easily fabricated and welded, and its unique properties make them suitable for many applications that require excellent chemical resistance to gases.
Advantages of Fluoroplastics
Fluorinated plastic offers a wide range of advantages over other materials, including excellent chemical resistance, high-temperature stability, low friction, and good electrical insulation properties. These properties make them ideal for use in a variety of applications, from chemical processing and aerospace to medical and electronics.
Durable
They are highly durable materials that can withstand harsh environments and extreme temperatures without breaking down or deteriorating. They have a low coefficient of friction, which means they are less likely to wear out or become damaged due to friction or abrasion. They are also highly resistant to impact and deformation, making them ideal for use in high-stress applications.
Wide Effective Range of Temperatures
Fluoroplastics are able to operate in a wide range of temperatures, from cryogenic temperatures to high-temperature environments. They exhibit excellent thermal stability, which means they can withstand exposure to high temperatures without melting or degrading. This makes them ideal for use in high-temperature applications such as aerospace, automotive, and chemical processing.
Corrosive Resistant
They are highly resistant to corrosive chemicals, such as acids, bases, and solvents. They do not react with these chemicals, which makes them ideal for use in harsh chemical environments, such as chemical processing plants and laboratories.
Inert, Non-toxic, and Bio-compatible
Fluoroplastics are inert materials that do not react with other substances, making them ideal for use in applications where purity is critical, such as in the pharmaceutical and medical industries. They are also non-toxic and bio-compatible, meaning they can be safely used in contact with human tissue and fluids, making them ideal for use in medical devices and implants.
Overall, the advantages of fluoroplastics make them a valuable and reliable material for a wide range of demanding applications. Their combination of durability, thermal stability, corrosive resistance, and inert, non-toxic, and bio-compatible properties make them a popular choice for industries such as aerospace, automotive, chemical processing, and medical.
Disadvantage of Fluoroplastics
While fluoroplastics offer many advantages, there are also some disadvantages associated with their use.
Relatively High Cost
They are more expensive than many other materials, which can be a disadvantage for some applications. The high cost is due to the complex manufacturing process and the high-performance properties of the materials.
Difficult to Mass Produce
Fluoroplastics are difficult to mass-produce due to their unique properties, which can make it challenging to achieve consistent quality in large-scale production. This can result in higher production costs and longer lead times.
Unweldable
They are generally unweldable, which means that they cannot be easily joined using traditional welding techniques. This can make it challenging to create large or complex structures using these materials.
Despite these disadvantages, fluoroplastics remain a popular choice for many industries due to their unique properties and benefits. With advances in manufacturing and fabrication techniques, the challenges associated with these materials are being addressed, making them more accessible and affordable for a wider range of applications.
A Trustworthy Fluoroplastics Provider: DECHENGWANG
DECHENGWANG is a reputable and reliable manufacturer of high-quality fluoroplastics. With over 30 years of experience, DECHENGWANG has built a strong reputation for providing custom solutions and high-quality products to meet the specific needs of its clients.
One of the primary goods and services provided by DECHENGWANG is the fabrication of custom fluoroplastic components. Using advanced manufacturing techniques and state-of-the-art equipment, DECHENGWANG is able to produce custom parts and components that meet the unique requirements of its customers through fluorination. This includes everything from small, precision parts to large, complex assemblies.
In addition to custom fabrication, DECHENGWANG also offers a range of standard fluoropolymer lab supplies, including sheets, rods, tubes, and films. These products are available in a variety of materials, such as PTFE, PFA, and PVDF, and can be used in a wide range of applications.
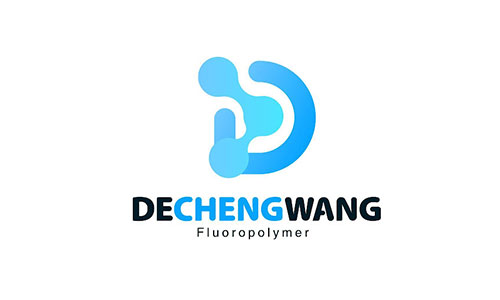
Another key service provided by DECHENGWANG is its compression molding capabilities. With a team of experienced engineers and technicians, DECHENGWANG is able to design and produce compression-molded parts and components using fluorination to meet the specific requirements of its customers.
DECHENGWANG also offers a range of value-added services, including machining, bonding, and welding. These services enable DECHENGWANG to provide complete solutions for its customers, from design and prototyping to production and finishing.
Overall, DECHENGWANG is a trusted and reliable provider of high-quality fluorinated plastic products and services. With a focus on customer satisfaction and a commitment to quality, DECHENGWANG is well-positioned to serve the needs of a wide range of other industries that rely on its unique properties of.
Conclusion
As a businessman, understanding the properties and applications of different materials is essential to making informed decisions for your business. This comprehensive guide on fluoroplastics has provided a wealth of information on the six types of fluoroplastics, their properties, and their applications. By carefully considering the properties and benefits of each type of fluoroplastic, businesses can select the most appropriate material for their specific needs, ensuring reliable and long-lasting performance.
If you’re in need of fluoro plastics components for your business, we encourage you to get in touch with DECHENGWANG to discuss your specific requirements and get a quote. Their team of experienced engineers and technicians can work with you to design and produce custom solutions that meet your unique needs. Contact DECHENGWANG today to learn more about how they can help your business.