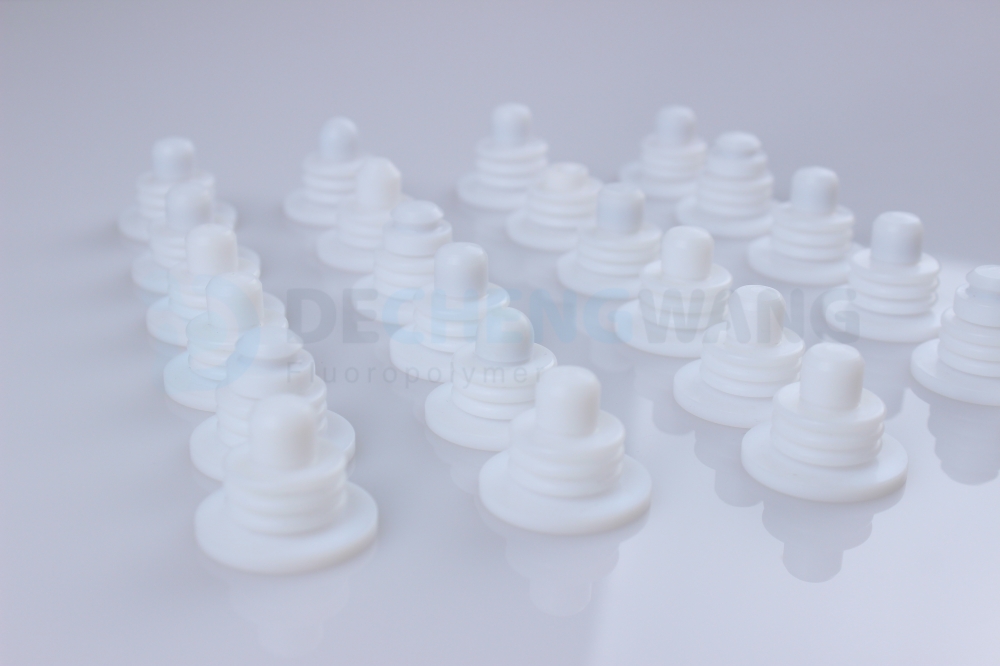
Applications: PTFE Bellows seals for valves
Bellows Mechanical Seal are a type of mechanical seal where the spring element is a bellows. They are a critical component in preventing fluid or gas
Home » O-Rings VS Guide Rings: What Is Their Difference?
Pressure sealings are indispensable for engine operations, refrigerators, boilers, and many other mechanical systems. These seals must prevent pressurized leakages and have a longer lifespan for optimal operations load. One of the most reliable materials that all manufacturers look for is an outstanding fluoropolymer named polytetrafluoroethylene (PTFE). However, what many people don’t realize is that PTFE is an umbrella term for various forms- PTFE bellows, O-rings, guide rings, etc.
Their versatility led to several forms of utilization. The two primary forms of PTFE include O-rings and guide rings. The latter is primarily made of elastomeric compounds which cater to resiliency and heavy leakage prevention. O-rings are inelastic materials and, as such, cannot be used for multiple-sealing purposes. On the other hand, PTFE guide rings are extraordinarily wear-resistant and prevent the piston components from instability. This blog aims to understand these two indispensable components and the aspects where they differ.
O-rings are a form of PTFE material in the shape of a doughnut. They are primarily made of elastomers and related compounds. They are made of rubber and thermoplastics in the form of a hollow structure. Their structure is an essential piece of functionality that prevents leakages and escaping of fluids during operations and protects against foreign particles from potentially damaging the machine. PTFE O-ring seals are compressed into the groove, thereby sealing the products. As it utilizes high pressure, there is little chance for passages.
O-rings are compressed against two solid surfaces, which maintains the seal. As it uses PTFE, a flexible, adaptive polymer, it retains its original shape with lesser pressure.
These ring-shaped materials are compressed against two pressure-induced surfaces to form an immovable seal. Its operations mimic that of a domestic gasket. Their requirements are on a different level, especially in thermal and chemical abrasion aspects, so the exposure is towards high-end pressure and abrasion, and thus, is sturdy in their requirements for withstanding.
The sealing tightness is directly related to the pressure it absorbs. There is a limit to how much pressure PTFE seals can take before it loosens. O-rings can be reutilized a limited number of times. They are not recyclable and become looser with each use.
This is a primary drawback of PTFE O-rings. They cannot be used repeatedly for long as their efficiency will decrease. Hence, their replacement becomes imperative after repeated compression.
O-rings carry the following properties:
O-rings carry the following disadvantages:
Those O-rings made of PTFE will suffer PTFE molding limitations with unconventional methods.
O-rings seals have a wide range of applications, from agricultural machinery to automobile manufacturing. Apart from the general applications in these industries, additional users can be attributed to the difference in materials used. Industrial O-rings are further divided into the following types based on the material in use:
PTFE O-rings: Machine components made of PTFE enjoy a handful of benefits when sealed with PTFE -rings. They are renowned for their durability and optimal functioning. They have excellent wear and tear resistance and are characterized by inertness to chemical abrasion. They are non-permeable and have low absorption capacity, which is incredible in automotive industries and paint gun applications. They can effectively work in temperatures ranging from -73 degrees to 260 degrees Celsius. O-ring installation is extremely simple, making it a viable choice for small businesses.
PFA O-rings: PFA O-rings are excellent substituents compared to other fluorocarbons due to affordability and melt processing capacities. Their resilience is higher than FEP. Their applications are the same as other fluorocarbons.
Selection of an O-ring material type requires adequate knowledge of each of them:
FEP O-rings: Another widely used fluoropolymer seal in FEP. Their characteristics can be considered a fusion of silicone and other fluorocarbons. They expanded from fluorinated ethylene propylene. They are known for their high-temperature range of -20 degrees to 204 degrees Celsius. Fluorocarbons are chemically inert due to the negative charges of fluorine atoms. When the core is substituted with silicon, its temperature range broadens. Their Coefficient of friction and flexibility is outstandingly remarkable. It is hydrophobic due to the loss of London dispersion forces.
Their applications are limited to static mechanisms or short-dynamic ones. They are indispensable in the food, beverage, pharmaceutical, and petrochemical industries.
Nitrile O-rings: Their second name is Buna-N or NBR, and their utility ranges broadly. With an effective temperature range between -50 degrees to 120 degrees Celsius, nitrile rings are incredibly resistant to abrasion, atmospheric conditions, and tear. Though they can withstand brake fluids like ketones and halogens, their resistance towards oils and hydraulic liquids is remarkable. Their application is not only limited to general agricultural sectors but also the following:
Neoprene O-rings: Neoprene is another material used in general and primary applications. It’s an all-purpose elastomer compound with exceptional resistance to petroleum-based materials. Its specialty lies in the resistance towards UV, ozone, and oxygen. As such, O-ring types in applications are also used on special occasions where other o-rings are not viable.
It has the same temperature range as NBR and incredible cracking resistance. Their resilience makes them great contenders for refrigeration coolants. They are used in seals in air conditioning units as well.
Silicone O-rings: with the broadest temperature range, these O-rings steal the market. Silicone rings are a worthy asset for industries where they are exposed to extreme thermal highs and lows. Their temperature range is from -100 degrees to 300 degrees, and sometimes their resistance is reported to be higher than this. They are flexible and are used in static applications like water, steam, and petroleum-based industries.
O-rings are used in the following applications:
As in the name, guide rings provide guidance and direction to hydraulic mediums, cylinders, and pistons. They are also known as wear rings or bearings and play an essential role in absorbing lateral forces between metal surface contacts. An example of these surface contacts is the interaction between pistons, cylinders, rods, and heads. All the forces acting against the cylinder are absorbed and regulated, thereby guiding pistons in the hydraulic medium. They prevent perpendicular contact with the medium and enhance seal performance.
Guide rings carry the following properties:
Guide rings are used in the following applications:
Guide rings are advantageous in the following manners:
Guide rings are made of either metallic or non-metallic materials, depending on their applications. Typically, they are preferred to be non-metallic due to wide applications and stringent benefits. Some of them include PTFE rods as well. They are available in the following materials:
PTFE-based guide rings: Their low coefficient of friction makes them worthy contenders for all hydraulic systems. They are suitable for dry air operations and are typically coated with steel or cast iron aluminum. They generate little to no abrasion. Their inexpensiveness is an excellent benefit for small-scale industries as well. They are highly resistant to thermal pressure with low stick-slip. The most resilient semi-finished forms are PTFE tubes.
Thermoset guide rings: They are widely used for their strong yet lightweight properties and extreme resistance to environmental abrasion. They are durable and portable, with little chance of damage. Thermoset rings manage heavier loads at low degrees of speed and are denser than metal ones.
Thermoplastic guide rings: Their application revolves around internal valves and compressors, thus called workhorses of all industries. Their benefits include inexpensiveness and high resistance to thermal and chemical conditions.
WAT and WGT Rod Piston Guide Rings: They are the standard guide rings used for general applications. Their operation is primarily dynamic and is well-applicable on either side of the surface. They are made of glass fiber-reinforced polyamide. Customized PTFE guide ring suppliers can also make them with different materials upon request.
RGR Rod Guide Rings: Unlike the above piston guide rings, they operate only on the inner surface. They dynamically guide rods and are made of cotton fabric laminated material. For ease of installation, they are manufactured in a split. Their assembling is a simple process.
PGR Piston guide rings: Their properties are similar to RGR rod guide rings, except that they are manufactured with a closed and narrow split before installation. They are available in a wide range of metric sizes.
Non-metallic gaskets are usually in the form of PTFE seals, CNAF, Leather, or Graphite. They are often used in low pressure and low temperature applications with the exception of graphite gaskets, which can withstand temperatures of up to 460⁰C.
While both O-rings and guide rings play an essential role in industries and work on medium hydraulic principles, they are designed for varied applications. For instance, O-rings are indispensable in engineering for their high-end performance and adjustable applications. They are a versatile breed of sealing that can be used effectively in static and mild-dynamic uses. Semi-finished products like PTFE film and sheet can be used for dynamic uses as well. The sealing configurations, however, require wear rings as an adequate substitute. The essential factor that determines the choice between them is their specifications.
A comprehensive overview of their difference is given below:
Purpose: The primary difference between these two indispensable polymers is their functionality and application. As mentioned, O-rings are special sealants. Though both are used in hydraulic medium cylinders, one is used as sealant while the other guides the components from lateral forces. O-rings are circular and are compressed as seals to prevent leakage. They seal the insides of the cylindrical tube. Guide rings, on the other hand, are used to protect the piston from up and down movements.
O-rings are designed to be pressed for compression seals, which are used for tanks and main body compartments. Pistons, bearings and shaft applications, on the other hand, utilize guide rings.
Materials: Another significant difference to note is the material they are made of. O-rings are typically found in materials like polyurethane, elastomers, PTFE, encapsulations, and metals. These materials function excellently as seals due to pressure resistance and versatility. Guide rings are primarily made from metal, rubber, or plastic. Additionally, guide rings are found in split form or as whole solid. When split, they are called split rings and are essential in various applications.
Applications: O-rings are invaluable for pressure-maintaining applications. Aerospace and chemical-based industries use them in components like pipes, pumps, and other valves. When talking about PTFE O-rings, however, they serve as cleaning maintainers in applications due to their lubrication and low coefficient of friction. Guide-rings’ primary objective is to guide the components and place them in influential positions. As such, they are required in automobile industries and electrical applications.
O-rings are power transmitters that are essential in the aerospace and petroleum industries. Since guide rings align components into their designated path, they support the function of gears and pulleys for optimal functioning.
Guide rings can also be used as anti-rotation devices where axial movement must be restricted.
Assembly: Their shape is another aspect where they differ. O-rings are cylindrical shaped. At the same time, guide rings have a unidirectional lip that prevents and corrects the movement of machinery. O-rings concern sealing between parts, and guide rings direct bearing shafts and pipelines.
In terms of assembly, O-rings differ from guide rings in terms of groove placement. Grooves are placed on PTFE guide rings due to ease of installation. These grooves enable manufacturers for simple tool usage.
Both O-rings and guide rings are two fundamental pieces of hydraulic cylinders. They regulate different areas and ensure optimum functional efficiency in operations. They contribute to enhanced workflow. O-rings eradicate the possibility of leakages and mishaps in machine operation. They are indispensable faucets for aircraft and aerospace applications. On the other hand, guide or wear rings are excellent regulators of such functions and guide the rods.
Dechengwang is a Chinese specialty organization that produces reliable PTFE O-rings and guide rings. We have been in the industry operations for several years and offer our clients customization services. We make several products with high-performance fluoropolymer material, like PTFE, PFA, PEEK, and PCTFE. Our range of manufacturing products includes O rings, bellows, ball valve seats, guide rings, insulators, bushings, and some semi-finished products. Our experts handle fluoropolymers with over 16 years of experience. Contact us to request a quote today!
Bellows Mechanical Seal are a type of mechanical seal where the spring element is a bellows. They are a critical component in preventing fluid or gas
In the world of engineering and manufacturing, where precision and efficiency are paramount, the role of wear resistance plastic has evolved far beyond their conventional image.
PTFE is a versatile polymer with outstanding properties like chemical resistance, low friction coefficient (self-lubricating), non-stick nature, and excellent electrical insulation. However, it also has some