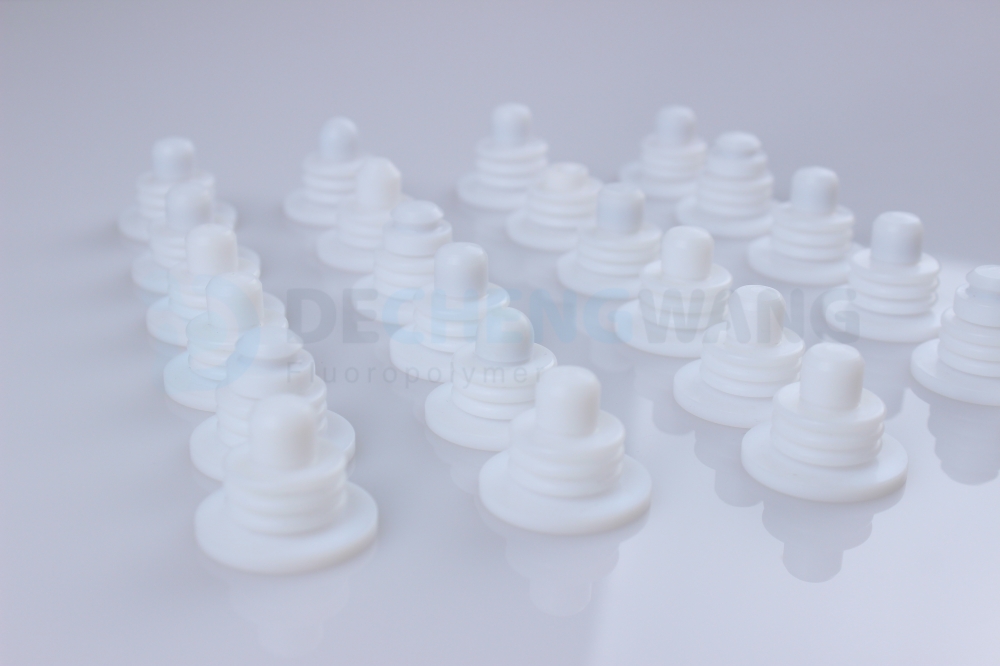
Applications: PTFE Bellows seals for valves
Bellows Mechanical Seal are a type of mechanical seal where the spring element is a bellows. They are a critical component in preventing fluid or gas
Polymer ball valve seats are one of the most popular materials used in the oil and gas industry. They are known for their strength, durability, and high temperature resistance to chemicals. This blog post will discuss the different factors to consider when selecting a polymer ball valve seat for several applications.
Polymer ball valve seats are increasingly being used in a variety of industries due to their many advantageous properties. Here take a look at five of the most important properties of these seats:
Polymer ball valve seats are made from a variety of materials, including nylon, polycarbonate, and polytetrafluoroethylene (PTFE). These materials are chosen for their resistance to wear and tear and their ability to withstand high temperatures. Polymer ball valve seats are also often treated with special coatings to improve their wear and tear resistance.
Polymer ball valve seats are a newer innovation with many advantages over traditional seat materials. One of the most significant advantages is that polymer seats are much more resistant to corrosion and chemicals. This is because the polymer material is non-reactive and does not break down in the presence of corrosive substances. This makes polymer seats an ideal choice for use in industries where corrosive chemicals are present. In addition, polymer seats are also less likely to seize up or wear down over time, making them a more durable option.
Polymer ball valve seats offer excellent resistance to temperature extremes, making them ideal for use in a wide range of industries. Here are just a few of the reasons why polymer ball valve seats are a good choice for applications that require high temperatures:
One of the most important properties of PTFE is its density. PTFE is very dense, with a specific gravity of 2.2. This means that it is almost twice as dense as water. This property makes PTFE compounds an ideal material for applications where weight is a concern, such as in aircraft components.
One of the most notable benefits of this product is its lightweight. Polymer ball valve seats are much lighter than their metal counterparts, making them easier to install and remove. Additionally, the light weight of these seats makes them less likely to wear out over time or become damaged. In addition to being light in weight, Polymer Ball Valve Seats are also strong and durable. These seats are designed to withstand various conditions, including high temperatures and pressures.
Most industrial ball valves have polymer seats. There are several reasons for this, but the two most important are that polymer ball valve seats are easy to install and require little maintenance. Polymer ball valve seats are also less likely to leak than metal seats. This is because the polymer material is more pliable and can create a tighter seal. As a result, polymer ball valve seats are often used in high-pressure applications. Another advantage of polymer ball valve seats is that they are less expensive than metal seats. This makes them a good choice for budget-conscious buyers.
Polymer ball valve seats are made from a variety of materials, including PEEK, PVC, CPVC, PVDF, and more. Here we will discuss all ball valve seat material.
PTFE, or polytetrafluoroethylene, is a type of fluoropolymer often used in ball valve seats. PTFE seat ball valve is known for its superior chemical resistance and low friction properties, making it an ideal material for valves. PTFE seats are often used in valves that handle aggressive chemicals, as they are resistant to a wide range of chemicals. PTFE valve seats are also self-lubricating, which helps to reduce wear and tear on the valve components.
PTFE seat material is offered in various FDA-approved grades and is deemed non-contaminating. The PTFE range is wide in temperatures, from cryogenic to 555degF. It can be used even after reprised exposure to hot and steamy water.
Glass-filled PTFE seats are even more durable than regular PTFE seats, and they can handle even higher pressures. Glass-filled PTFE seats are especially well-suited for high-pressure and high-temperature applications. The addition of glass fibers strengthens the seat material and helps resist wear. Glass-filled PTFE products are also FDA-approved for use in food and beverage applications. This ball valve seat material can handle demanding applications.
They are chemically resistant, have a low friction coefficient, and are durable. Glass-filled PTFE seats also have several other benefits. They are non-wetting, which means they will not absorb liquids or gasses. They are also self-lubricating, which reduces the need for lubricants and makes them easier to maintain.
Carbon-filled PTFE ball valve seats are made from a composite of PTFE and carbon. The carbon filling gives the PTFE greater strength and rigidity, making it an ideal material for ball valve seats. The PTFE also provides excellent chemical resistance and low friction, making it an ideal material for valve seats.
PEEK seat material is chemically resistant and has low friction on the same scale as PTFE; however, it can handle slightly higher temperatures, between -70degF and 560degF. It is extremely adept at handling nuclear applications and those involving extreme loads and high temperatures. The PEEK parts are also very resistant to flames and are ideal for steam and hot water exposure.
PEEK ball valve seats are designed for use in various industries, from food and beverage processing to pharmaceuticals and more. Peek ball valve seats are also easy to clean and provide excellent corrosion resistance, making them a perfect choice in hygiene-critical industries.
PFA materials ball valve seats are made from a proprietary blend of PFA and other polymers. This blend of materials provides superior performance in demanding applications. PFA seats are available in various shapes and sizes to meet the specific needs of applications.
PVDF ball valve seats are used in ball valves made of polyvinylidene fluoride. PVDF is a fluoropolymer that offers high chemical resistance and thermal stability. PVDF seats are used in high-temperature and corrosive applications where other materials are unsuitable. PVDF seats are also known for their low friction coefficient, making them ideal for use in valves that require a tight seal. PVDF is often used in processes involving hydrofluoric acid, sulfuric acid, and other acids that would quickly erode most other materials. PVDF is also used in processes with strong alkalis, such as caustic soda.
A metal ball valve seat is a type of valve seat that is made out of metal. It is usually made of stainless steel, but it can also be made of other materials. The metal ball valve seat is a type of valve seat used in many different industries, such as the food and beverage industry, the chemical industry, and the oil and gas industry. The metal ball valve seat is a type of valve seat designed to be durable and to last for a long time.
A ball valve seat is an important component of a ball valve. The seat provides a surface for the ball to contact and seal against. The seat also helps guide the ball in the proper position to ensure proper valve operation. Ball valves are used in various applications, including oil and gas production, chemical processing, and water treatment.
There are several reasons why a ball valve seat is important. First, the seat helps guide the ball in the proper position for proper valve operation. Second, the seat provides a surface for the ball to contact and seal against. Third, the seat helps prevent the ball from vibrating and potentially causing damage to the valve or pipeline. Fourth, the seat helps keep the ball in place when the valve is closed, preventing leakage.
Ball valves are widely used in different industries because of their many advantageous features. They are durable, have a long lifespan, are easy to operate, and offer a tight seal that is perfect for high-pressure applications.
The selection of the right valve seat is critical to the success of any polymer ball valve application. This article provides a brief overview of the ball valve seat material selection guide to help in selecting the right valve seat. For more information, visit our website https://ptfedf.com/. Dechengwang has years of experienced in machining PTFE parts especially PTFE ball valve seats and also other materials for you to select.
Bellows Mechanical Seal are a type of mechanical seal where the spring element is a bellows. They are a critical component in preventing fluid or gas
In the world of engineering and manufacturing, where precision and efficiency are paramount, the role of wear resistance plastic has evolved far beyond their conventional image.
PTFE is a versatile polymer with outstanding properties like chemical resistance, low friction coefficient (self-lubricating), non-stick nature, and excellent electrical insulation. However, it also has some