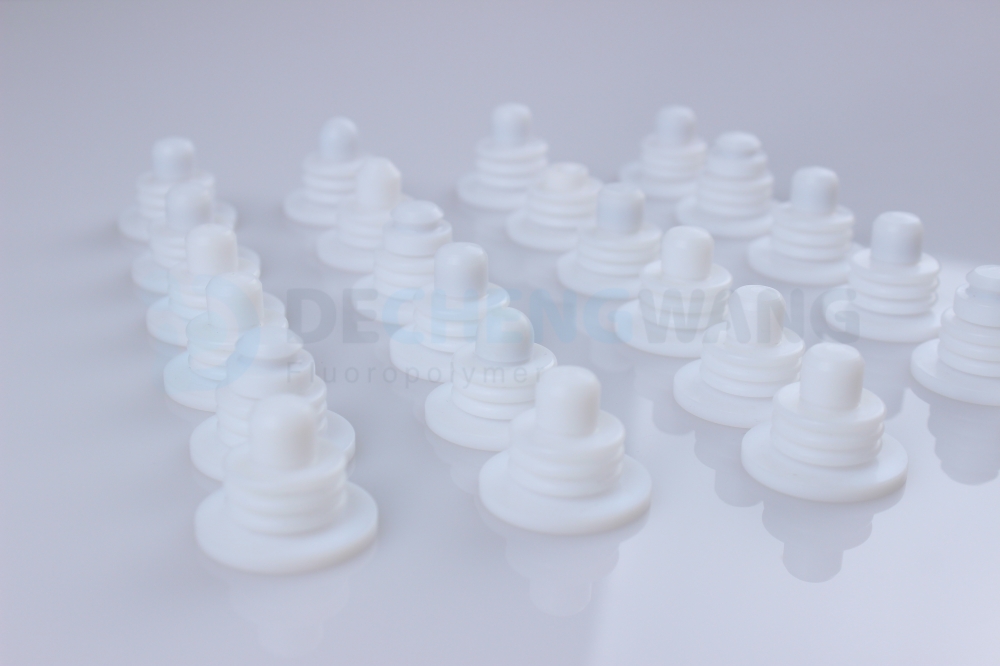
Applications: PTFE Bellows seals for valves
Bellows Mechanical Seal are a type of mechanical seal where the spring element is a bellows. They are a critical component in preventing fluid or gas
An O ring is a mechanical gasket with the shape of a torus and is also referred to as a packing or a toric joint. It is a coil of elastomer with a circular cross-section. The O ring is constructed to be placed in a hole and flattened while assembling between two or more elements, establishing a seal at the interface.
An O ring avoids leaks by sealing a system with a strong barrier that keeps pressured gas and water within and shows resistance to moisture. O rings lock the system by compressing between two linked fittings, which deters any outer air or moisture from arriving.
From the time of their invention at the end of the nineteenth century, O rings have been an integral feature of a variety of machinery. Because of their capacity to seal and hold gases and liquids, they have become a necessary component of equipment design.
The fundamental O rings and their uses have developed and thrived to a great level. They are available in different sizes, designs and are made from various materials to fit the application needs of various fields.
O rings have round mountings that resemble the shape of donuts and are condensed between two parts to create a sturdy, tighter seal. In principle, they are relatively identical to a typical type of gasket. However, the only exception is that O rings are particularly intended for use in industrial applications where severe temperatures, chemicals, or pressures will be encountered.
As O rings are able to bear the tension in different situations, they have become a simple yet productive answer to a problem that has plagued many industries for decades. Also, the availability of O rings in different materials makes it easy to use the ideal one depending on the requirements of the application.
O rings are made of more robust elastomers that have the potential to endure the harsh circumstances to which they are exposed. They function when inserted into a tunnel or gland between two separate pieces of equipment, which can be static or dynamic.
The O ring is made to mold to the specific measurements of the surfaces clasping against it when two parts are compressed together. As a result, it leads to the development of an impenetrable barrier that will not permit air or water to pass through.
When high pressure is indicted on the O-ring, it will develop a more tighter seal. On the other hand, it is critical not to apply too much pressure to the O ring since it has the capacity to destroy itself and compromise to the seal.
One more appealing feature of O rings is that they will get back to their original round shape after the two compressed elements of the equipment are disengaged and the pressure imposed on the O ring is relieved.
It means that manufacturers can reuse O rings for a variety of industrial applications. However, it is vital to keep in mind that they cannot be recycled constantly. The tension that is put on it will eventually degrade the O-ring’s
consistency and durability. Thus, it will need to be replaced with a new one if an acceptable seal is to be used.
O rings come in a wide range of metric and inch standard sizes. The interior diameter and cross-section diameter are used to define the sizes (thickness) of the O rings. Extrusion, pressure molding, injection molding, and transfer molding are all options for making O rings.
Even though the O ring was given its name due to its round cross-section, it currently comes in a variety of shapes and sizes. The form can have a range of profiles, including a Q-ring, or Quad Ring, an x-shaped profile, which is also known as the X-ring. Square cuts, tabular cuts, Square rings, and lathe cuts are examples of rings that have a square profile.
Different O ring types are employed in a variety of industries, such as: Food and dairy, Aerospace, Fluid power and motion control, Medical, OEM custom parts manufacturing, industrial hydraulics and pneumatics, oil and gas, Marine, Pharmaceutical, and more.
Here is the outlined list of different types of O rings.
Polytetrafluoroethylene (PTFE) has a high friction and water resistance along with decent thermal insulation. O rings made of polytetrafluoroethylene, or PTFE, are a common choice. They are white and are prized for their resistance to several oils, chemicals, steam, and acids. They can work in severe temperatures ranging from -100 to 500 degrees Fahrenheit.
The pure PTFE O rings are relatively rigorous and difficult to apply. However, PTFE encapsulated O rings can deal well with surface wear and are resistant to abrasion. Since PTFE is rigid, it is better suited to static applications. The PTFE O rings are employed in paint funds, mechanical steering devices, and the making of various PTFE products.
The silicone rubber O rings can work between -120 degrees Fahrenheit and 450 degrees Fahrenheit. However, these O rings have the capability to survive -175 degrees Fahrenheit for a short duration of exposure. The fuel injection ports with heavy temperature needs typically use silicone rubber O rings.
Silicone displays low resistance to flow, tensile strength, and abrasion. Due to the bad abrasion resistance, these O rings are ideal for static applications compared to dynamic ones. On the other hand, Silicone O rings do conduct adequately with steam, water, or petroleum.
The nitrile O rings are highly suitable for industrial applications where there are limited prerequisites related to resistance and temperature. These O rings maintain the temperature range of -65 degrees Fahrenheit to 300 degrees Fahrenheit. They are the best options as typical purpose seals like water, petroleum oils, and hydraulic fluids.
Buna-N or acrylonitrile butadiene is another name for NBR. It is a butadiene and acrylonitrile-based synthetic rubber copolymer. NBR features strong mechanical qualities and shows resistance to wear, which are affected by the ratio of different compounds used to make it.
If the nitrile content is high in O rings, it means that they present more resistance to oil and gasoline impacts. It comes in a variety of hues and is best for applications with dilute acids, salt solutions, and alkalis.
Fluoroelastomer is well-known for its strong resilience to heat and a broad range of chemicals. Other major advantages include incredible aging and ozone resistance, relatively low gas permeability, and self-extinguishing substances. The fluoroelastomer O ring type can operate in temperature conditions between 5 degrees Fahrenheit to 625 degrees Fahrenheit.
These O rings are ideal for applications with a high maintenance or downtime cost. They are also used where high-temperature resistance, strong chemical resistance, and low outgassing are essential. Some industries that use fluoroelastomer O rings are food and beverage, oil and gas, medical, and more.
The applications of O rings are relatively vast, and many industries employ them for different reasons. Check out this brief information about the most common applications of O rings.
The most prevalent application for O-rings is in high-pressure applications, and the tension on the O-ring causes distortion in the gland. The O-surface ring is subjected to even mechanical pressure. The most critical aspect is that the pressure slope does not exceed the O-stress ring’s rating.
When O-rings are put under heavy pressure, seepage or leakage is virtually impossible. In the case of a mechanical failure, extrusion and O-ring devastation can happen in some cases. By selecting the appropriate O-ring material for the application, it can be prevented.
O-rings must be pressure, temperature, and chemically compatible for an engine seal. Several rubbers and plastics are not strong enough or resistant enough to be employed in engine applications. In such circumstances, hybrid substances that are particularly created for the application are employed.
Compressors and UHV pumps both utilize vacuum O-rings. Vacuum O-rings are made of an impermeable substance that distorts into the sealing surface and outgasses. The sealing surface must be rough, flat, and smooth in order for the O-ring to adequately disfigure into the gland.
Based on the type of gas, each O-ring has a varied penetration rate. Silicone is very permeable to air, but FKM and Viton are not. Vacuum seal O-rings may adjust to the imbalance of the vacuum’s surface. Grease can be added to soften the O-ring and the surface. Static O-rings are employed in vacuum applications.
High-temperature applications necessitate O-rings that can endure higher temperatures and also conserve their seal. O-rings might have to be installed in a tangentially compressed nature in a few high-temperature applications. Chemical processing plants, turbo engines, refineries, and aerospace industries demand O-rings that can tolerate extreme temperatures.
O rings can be found in a wide variety of industrial applications which are listed below.
Depending on the type of industry and the O ring applications, some businesses reach out to the O ring manufacturer to order bulk custom O rings as per their application requirements. A few businesses order O rings that need to be compatible with their customized products. Dechengwang, as a experienced PTFE components manufacturer, supplies O rings and other custom PTFE parts for your industry application.
The FDA has cleared the materials used to make O rings for the food and beverage industries. These O rings must meet the exact rules that are set for any material that gets in contact with food. The food and beverage businesses can check these requirements in the “White List” in Title 21 of the Code of Federal Regulations. Due to the restrictions on curing substances, several materials listed are built for high compression.
O rings are better at protecting liquids and gases from shifting around. Due to that, they are frequently used in mechanical components and procedures, especially if the temperature or pressure extremes are present. A few of the mechanical engineering applications of O rings include refrigerators, boilers, compressors, and engines.
O rings are used to seal the different types of liquids found in buses, automobiles, and trucks. Fuels, lubricating oil, and refrigerants are some of the various types of fluids present in automobiles. In addition, each one has its own set temperature and speed of use. O rings are used as a sealant and leak prevention in braking systems and lubricants for engines and transmissions. For instance, automotive steering devices use PTFE O rings.
The O ring elastomers manufactured to withstand a spectrum of ohms (7 cm to 0.002 cm) are utilized in the electronics field to protect against electromagnetic interference (EMI). Telecommunications, industrial electronics, military, and consumer electronics employ these O rings. They deliver a potential interface for different applications and are available in a variety of sizes to accommodate the application needs of electronics and semiconductors.
O rings are highly significant in aircraft construction as they conserve jet engines from high-temperature swings and dangerous circumstances. Plenty of O rings are utilized in the commercial aerospace industry. In addition, each one is engineered to fulfill a specific purpose, such as adjusting to high and low pressures, forceful lubricants and fluids, and extreme temperature fluctuations.
Changes in aircraft design have necessitated the development of new O ring compositions in order to satisfy the growing demand for the new conditions. O rings’ operating temperatures have exceeded +275 degrees Fahrenheit in the latest designs due to the development of more lasting compounds.
O rings are critical components in the exploration, processing, and passage of oil products in the petroleum, oil, and gas sectors. Mining and taking out fuel products are usually performed in difficult locations.
So, the biggest issue for O rings in the oil and gas sector is the extreme conditions under which they should work. These O rings must withstand all regular temperature and pressure circumstances, but to higher standards than those used in other fields.
Dechengwang is a china based leading company in the fluoropolymer field with an experience of over 16 years. We produce several products with high-performance fluoropolymer material, like PTFE, PFA, PEEK, and PCTFE. Our range of manufacturing products includes O rings, bellows, ball valve seats, guide rings, insulators, bushings, and some semi-finished products.
We supply these products to various fields, including oil and gas, automotive, aerospace, food and beverage, medical, electronics, chemical, and more. For any O ring needs, make sure to reach out to a decent O ring manufacturer to get free quotes and acquire high-quality, sturdy O rings for your market needs.
Bellows Mechanical Seal are a type of mechanical seal where the spring element is a bellows. They are a critical component in preventing fluid or gas
In the world of engineering and manufacturing, where precision and efficiency are paramount, the role of wear resistance plastic has evolved far beyond their conventional image.
PTFE is a versatile polymer with outstanding properties like chemical resistance, low friction coefficient (self-lubricating), non-stick nature, and excellent electrical insulation. However, it also has some