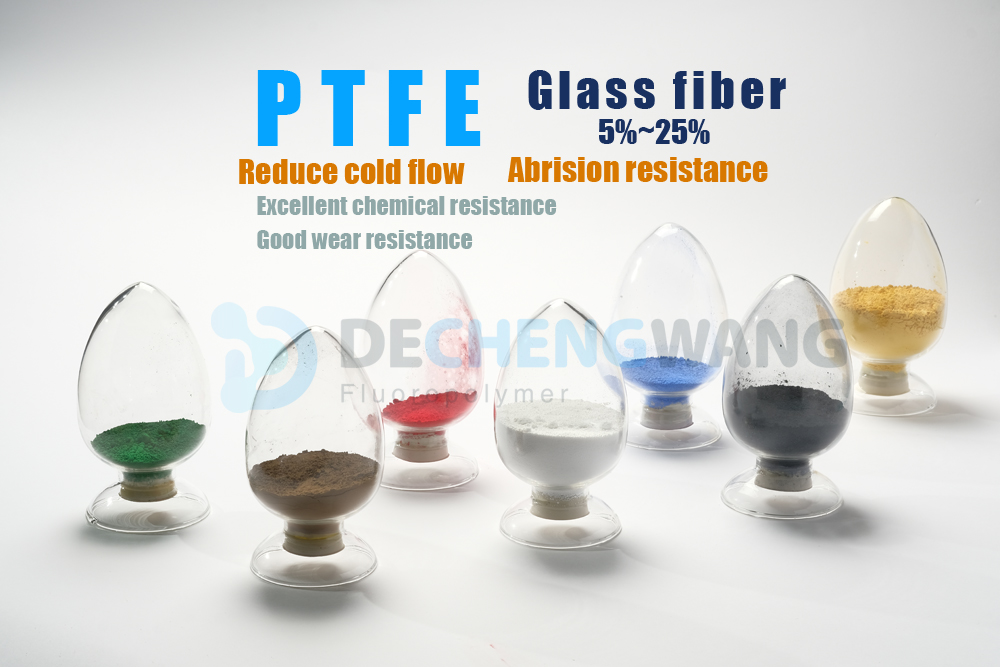
Glass Filled PTFE (also call glass fiber filled PTFE, glass reinforced PTFE) is manufactured from a base of virgin PTFE or midified PTFE which is strengthened by the addition of glass fiber.
PTFE or know as Teflon, polytetrafluoroethylene is a synthetic fluoropolymer with attractive characteristics, such as a very low friction coefficient, wide range of service temperatures, high flammability resistance, low dielectric constant and high chemical resistance.
In most situations, PTFE is the perfect fluoroplastic for a wide range of applications. However, PTFE has disadvantages of high linear coefficient of thermal expansion (CTE = 109 ppm∙˚C−1) , low thermal conductivity and low mechanical strength. One of the efforts to overcome it weakness is to add inorganic fillers such as micro-fiberglass particles into the PTFE. In today’s blog, we will introduce glass filled PTFE, what performance does it improve, it manufacturing process, and applications.
Glass filled PTFE – What it’s made of?
Glass fiber is a composite material comprising various oxides such as SiO2, Na2O, MgO, and others. It is an inorganic non-metallic substance known for its exceptional performance, including corrosion resistance and abrasion resistance. When utilized as a filler for PTFE compound, the most prominent characteristic of glass fiber is its ability to enhance compression and wears properties.
In the PTFE compound, the addition of physically filled glass fibers results in a composite material with dimensional stability, cold flow resistance, creep resistance, heat resistance and better electrical properties of the material. Furthermore, it reduces the expansion coefficient of the material and helps prevent cracking.
It is important to note that glass filled PTFE also have certain drawbacks. For instance, the exposed glass fibers can give the product a rough surface. Additionally, mechanical processing equipment may experience significant wear when working with glass fiber materials.
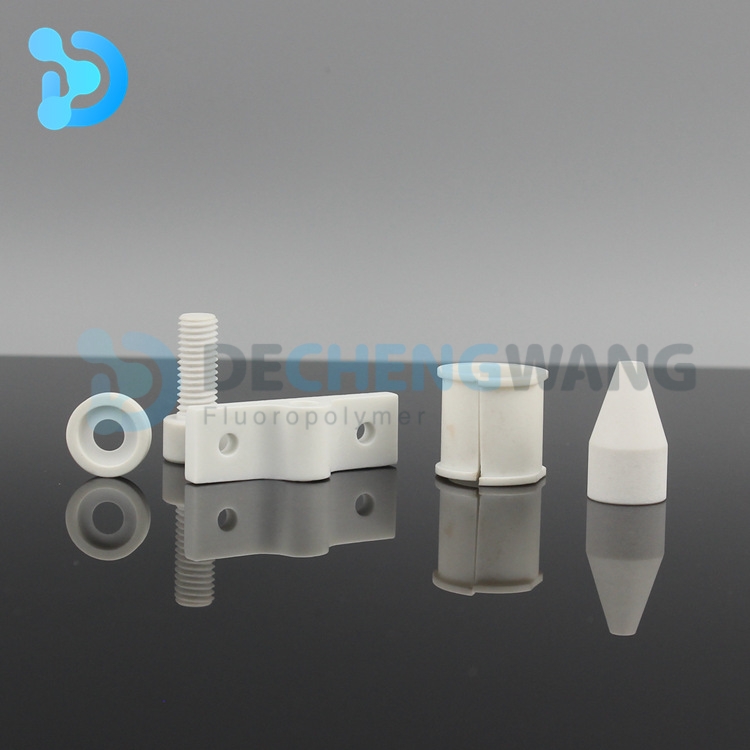
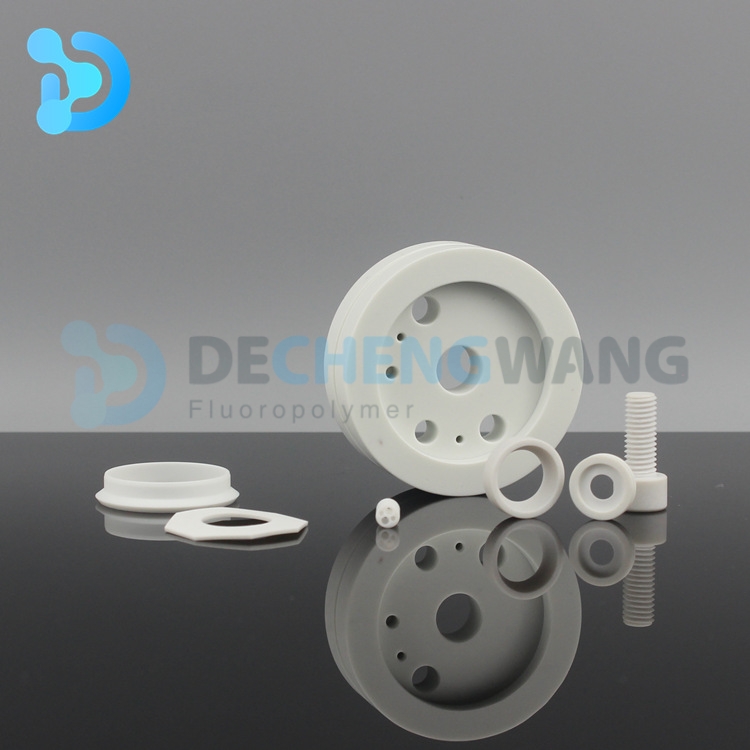
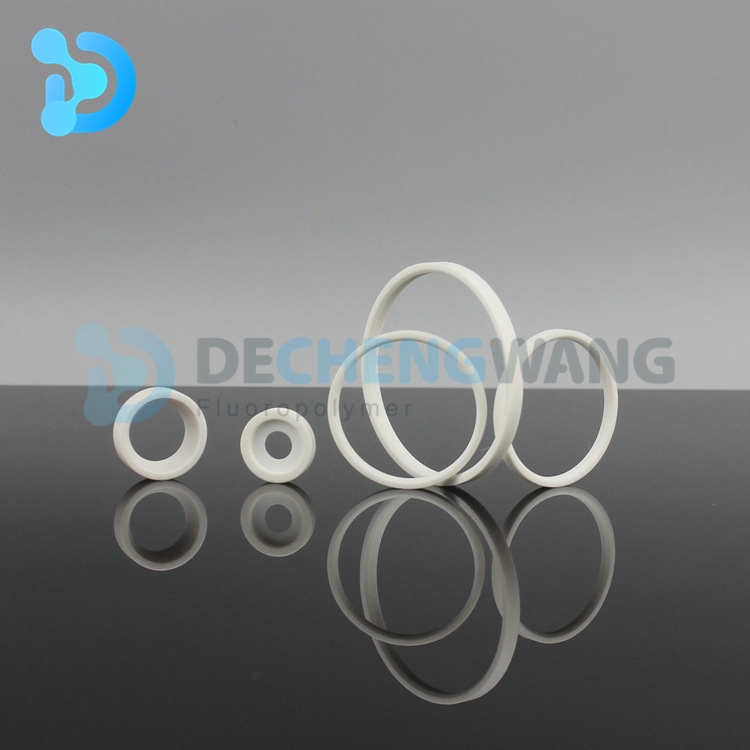
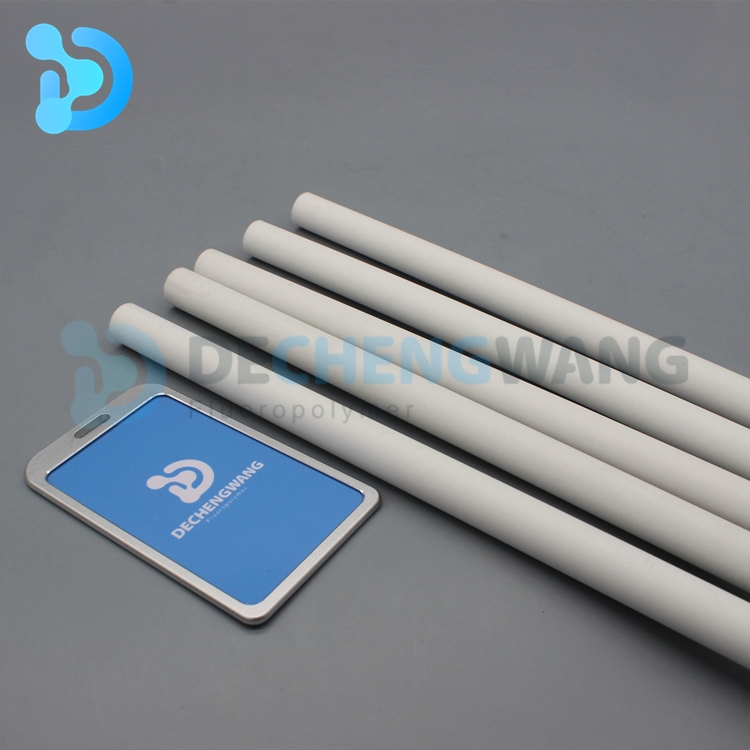
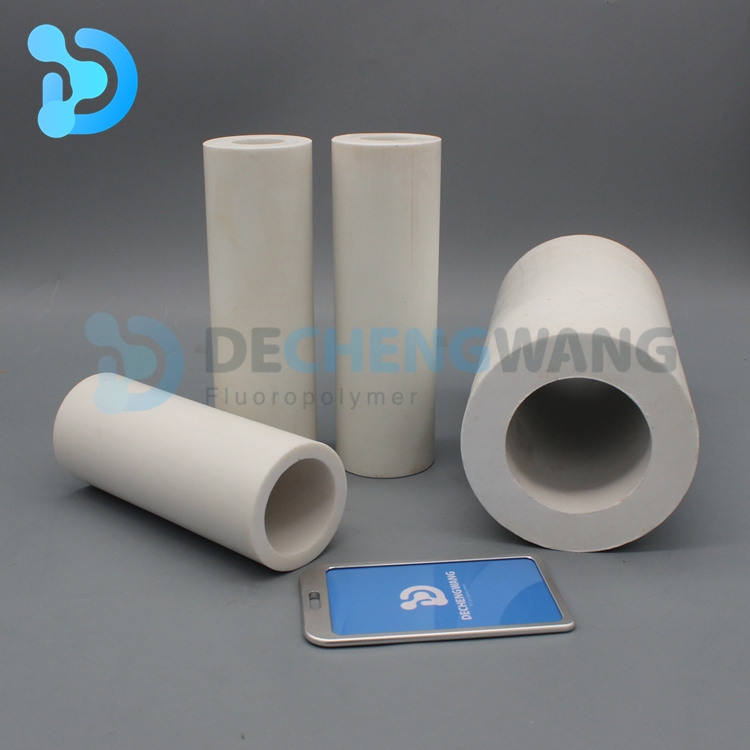
Glass filled PTFE – What performance does it improve?
- Improved Wear resistance
The main advantage of glass filled PTFE is that it can significantly increase the wear resistance of the seal. Compared with unfilled PTFE materials, the wear resistance performance is increased by nearly 500 times. The abrasion resistance is greatly improved.
- Improved dimensional stability
Increased compressive strength and the creep resistance of PTFE over all temperature ranges, while still allowing some compression required for sealing in both gaskets and valves.
Filler | Specific gravity | Tensile strength (cross direction) Mpa | Elongation (Cross direction)% | Hardness Shore D | Shrinkage rate % | Other possible combination |
Non-filler | 2.17 | 31 | 310 | 57 | 3.0 | MoS2/carbon/ Graphite |
15% Glass | 2.22 | 23 | 300 | 62 | 2.4 | MoS2/carbon/ Graphite |
25% Glass | 2.25 | 18 | 270 | 64 | 2.1 | MoS2/carbon/ Graphite |
It manufacturing process
Generally, the diameter of the glass fiber filled into PTFE is 10-13 microns, the average length is 80 microns, the aspect ratio is min. 10. Glass Filled PTFE is reinforced with glass fibers with the percentage varying between 5% and 25% depending on the needs of the application.
15 glass filled ptfe, 25 glass filled ptfe is regular use. Even though small percent (like 5%) of glass filled PTFE can be process with extrusion, but We do recommend process glass filled PTFE with Compression Moulding.
Compression Moulding has a better physical property than extrusion PTFE, such as Density, Tensile Strength, Compressive Strength, Hardness & Low (Low void content) permeability – longitudinally due to good compaction.
Compression Moulding is processed using metal molds, glass filled PTFE powder is loaded into the mould and compressed under vertical pressure in a hydraulic press for a specified time delivering the desired shape. The preforms need to sintere in electrical ovens after stripped from the mould and then cooled gradually to deliver the finished product. It is the most used processing method for cylindrical, rectangular and sheet shapes of PTFE.
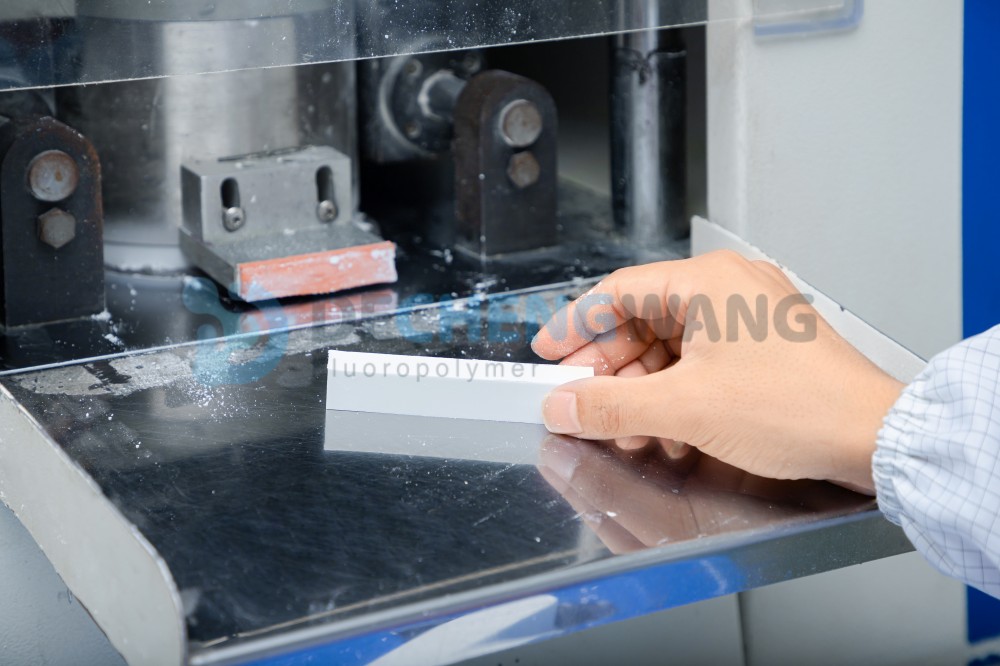
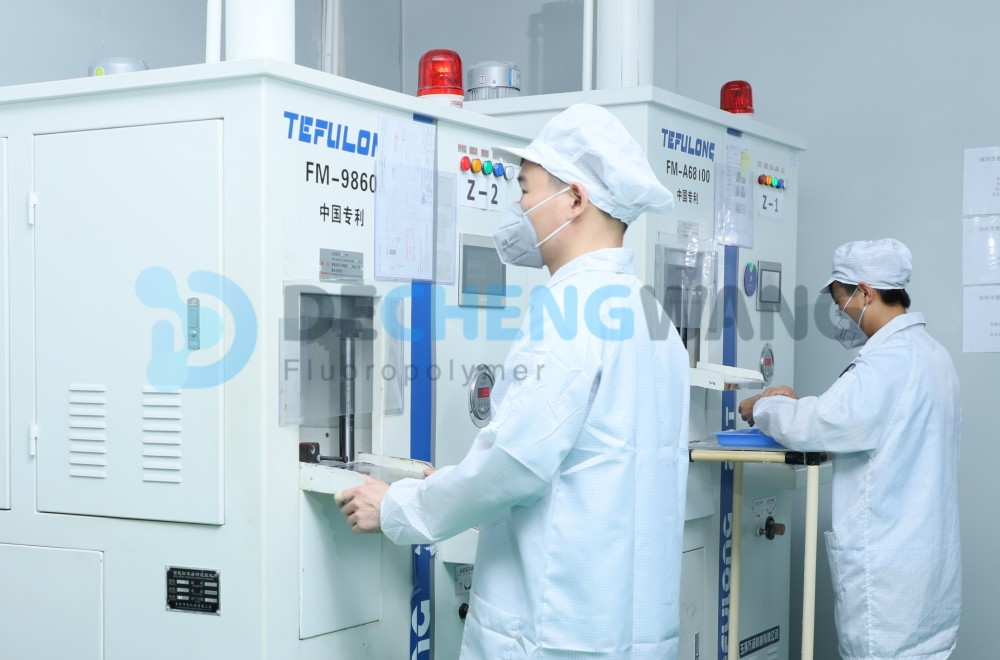
Applications
- Glass Filled PTFE is very commonly used in valve seat applications
- Self-lubricating bearings
- Gaskets (static-dissipating, other
- Seals (all types)
- Compressor rings
- glass filled ptfe rod
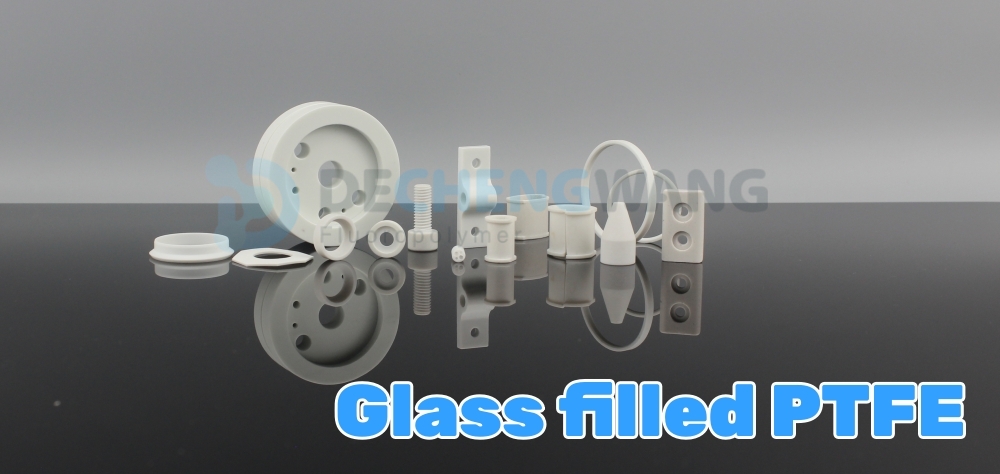
PTFE is an incredibly versatile material with many performance benefits. Adding fillers can help overcome its disadvantages while adding performance properties to the compound.
To learn more about creating the right PTFE compound for your application contact a DCW expert.