One of the leading forces that deteriorate the functionality of mechanical components is heat. Hence, the importance of resistant components like high temperature o-ring to provide perfect sealing solutions in extreme temperature conditions.
From aerospace, automotive, chemical processing, oil & gas, and many other industries, heat resistant o-rings play a critical role in ensuring safety, efficiency, and optimal performance of equipment and systems.
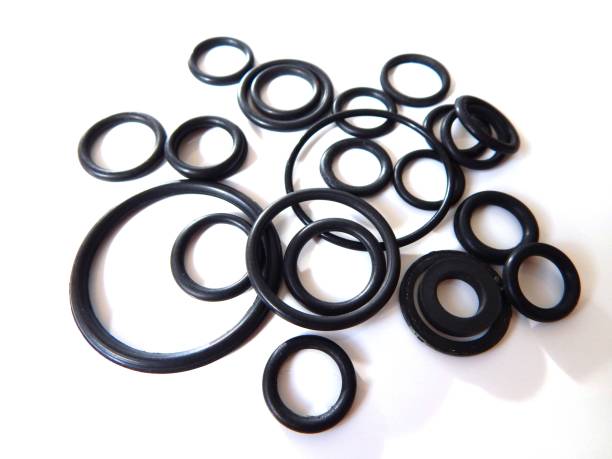
In this article, we will explore everything you need to know about O-rings high temperature, including the definition, properties, materials used for the production, applications, and the most reliable high temp o-rings service provider to meet your customers’ specific needs.
What is a High Temperature O-ring
A high-temperature o-ring is a circular sealing device designed to create a tight seal between two or more components under high temperature and pressure conditions.
These O-rings are typically made of specialized fluoropolymer materials that can withstand extreme temperatures ranging from -50°C to over 300°C. They can be used in various industrial applications, especially where traditional o-rings would fail due to their limited temperature range.
Requirements for High Temperature O-rings
O-rings come in various materials to accommodate different needs, such as chemical resistance or pressure tolerance. However, when it comes to high temperatures, certain factors need to be considered carefully to prevent premature failure or even disaster.
If you’re dealing with high temperatures in your industry, choosing the right O-rings is crucial. This article will cover the specific requirements for O-rings that will operate effectively and safely at elevated temperatures. By understanding these factors and selecting the proper O-rings accordingly, you can avoid costly downtime and ensure optimal performance of your equipment.
Physical & Chemical Inertia: High-temperature o-rings must have excellent physical and chemical inertia to prevent any unwanted chemical reactions with the materials they are in contact with and resist degradation caused by harsh environments. This ensures that the o-ring does not degrade, crack, or swell, leading to a failure of the seal.
High Temperature & Cryogenic Resistance: They must be capable of withstanding temperatures, both high and low (ranging from -50°C to +300°C or higher), hence maintaining their seal integrity.
Moisture Resistance: Moisture can cause o-rings to swell, deteriorate, or lose their sealing properties, causing the sealing surface to be penetrated, which could lead to equipment failure. High-temperature o-rings must be made with materials that are non-porous and have a low water absorption rate.
Low Friction Coefficient: High temp o-rings should have a low coefficient of friction, which ensures that the o-ring does not create excessive heat or cause wear on the materials it is sealing. This also ensures that the o-ring can be easily installed and removed without causing damage to the equipment.
Flexibility: They should be flexible to accommodate the expansion and contraction that occurs as a result of temperature changes. The o-rings must be able to maintain their sealing properties even when subjected to extreme temperatures and pressure fluctuations.
Durability: They must be able to withstand repeated exposure to high temperatures, pressure, and chemical exposure without experiencing significant wear or damage. The o-rings must be made of materials that are strong and resistant to mechanical stress, abrasion, and fatigue.
Fluoropolymer Materials Selection for High Temperature O-rings
Fluoropolymer materials are known for their excellent chemical and thermal stability, making them suitable for use in harsh environments. Major fluoropolymers used by high temperature o-rings manufacturers include PTFE, PEEK, PVDF, PCTFE, and PFA. They have outstanding features that make them appropriate for manufacturing heat-resistant o-rings.
Discussed below are the properties possessed by these materials and their functionality in extreme temperatures.
PTFE – Polytetrafluoroethylene
PTFE (Polytetrafluoroethylene) is an o-ring material for high temperatures that has a unique molecular structure that gives it a low coefficient of friction, which means that it resists sticking and sliding. This property, combined with its excellent chemical resistance, makes it an ideal material for use in harsh environments.
It has a melting point of around 327°C and can withstand temperatures of up to 260°C (500°F) without undergoing any significant degradation. This makes it suitable for o-rings used in extreme temperature applications such as aerospace, automotive, and chemical processing industries.
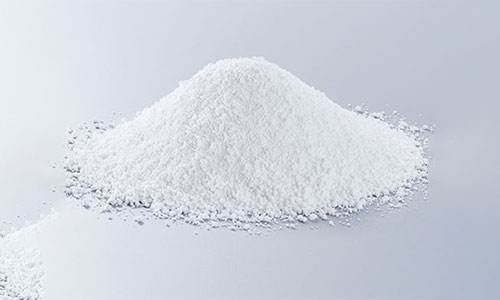
Moreover, PTFE is highly resistant to chemical attacks from acids, bases, and organic solvents, which can degrade many other types of materials. This makes PTFE o-rings suitable for use in harsh chemical environments, where other materials may not be able to withstand the conditions.
PEEK – Polyetheretherketone
PEEK (Polyetheretherketone) is a high temperature o-ring material often used in extreme environments due to its exceptional thermal, mechanical, and chemical properties. It has a high melting point of around 343°C (649°F) and can maintain its mechanical properties at temperatures up to 250°C (482°F) without undergoing any significant degradation.
This makes it a suitable material for o-rings used in high-temperature applications such as in the aerospace, oil & gas, and automotive industries.
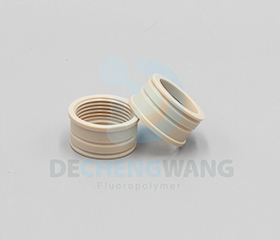
It has excellent resistance to chemicals, making it ideal for use in harsh environments where exposure to chemicals is expected. It is also highly resistant to abrasion and has excellent dimensional stability, meaning it can maintain its shape and size even in high-temperature environments.
Moreover, PEEK material has great mechanical properties, including high strength and stiffness, and it is resistant to wear and fatigue.
PVDF – Polyvinylidenfluoride
PVDF (Polyvinylidenfluoride) is a thermoplastic o-ring material for high temperatures known for its excellent chemical resistance, heat resistance, and good mechanical properties. This makes it a popular choice for manufacturing o-rings used in extreme temperature environments.
PVDF material has a high melting point of around 177°C (350°F), which means it can withstand temperatures well above the boiling point of water. It also maintains its mechanical strength and dimensional stability even at high temperatures, making it ideal for use in extreme temperature applications.
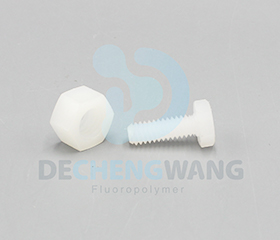
In addition to its high-temperature resistance, PVDF is highly resistant to chemicals, including acids, bases, and organic solvents. It is also resistant to UV radiation, making it suitable for outdoor applications.
When used as a material for manufacturing o-rings, PVDF provides excellent sealing performance in high-temperature environments. It can withstand continuous exposure to temperatures of up to 150°C (302°F) and intermittent exposure to temperatures of up to 180°C (356°F).
PCTFE – Polychlorotrifluoroethylene
PCTFE (polychlorotrifluoroethylene) is a top-performance high temperature o-ring material that exhibits excellent heat resistance and is often used in applications where high-temperature and chemical resistance are required, such as in aerospace, oil and gas, and semiconductor industries.
One of the key properties of PCTFE is its exceptional heat resistance. It has a melting point of around 215°C (419°F) and can maintain its properties even at temperatures as high as 300°C (572°F) for short periods. This makes it an excellent material for use in high-temperature applications such as o-rings, where it can withstand extreme heat and pressure.
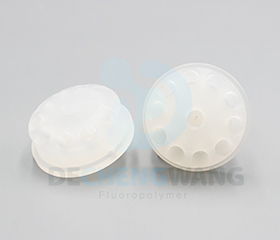
PCTFE is also resistant to a wide range of chemicals, including acids, bases, and solvents, making it an ideal material for use in harsh chemical environments, where other materials may degrade or fail. Additionally, it’s highly resistant to abrasion, making it ideal for use in applications where wear and tear are a concern.
Moreover, this PCTFE o-ring is resistant to compression, which is the tendency of an o-ring to become permanently deformed when compressed over time.
PFA – Perfluoroalkoxy Resin
PFA (Perfluoroalkoxy) is a premium o-ring material for high temperatures that can withstand continuous exposure to temperatures up to 500°F (260°C) and can tolerate intermittent exposure to temperatures as high as 600°F (315°C). This makes PFA o-rings an ideal choice for use in extreme temperature environments such as those found in aerospace, automotive, and chemical processing industries.
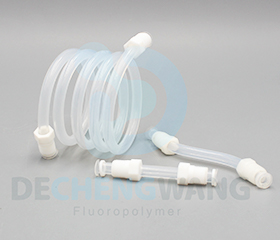
In addition to its high-temperature resistance, PFA material exhibits excellent chemical resistance, low permeability, and good mechanical properties, which make it suitable for use in a wide range of applications. PFA o-rings can resist a variety of chemicals, including acids, bases, solvents, and oils, without degrading or losing their sealing properties.
Also, PFA o-rings are highly resistant to compression, meaning they can maintain their shape and sealing properties even after being compressed for extended periods. This makes them an ideal choice for use in dynamic sealing applications, such as those found in pumps, valves, and other mechanical systems.
Applications of High Temperature O-rings
High temp o-rings are used in many industries for several applications to ensure the smooth operation of mechanical systems. Discussed below are some of them.
1. Aerospace Industry
In the aerospace industry, high-temperature o-rings are crucial components in jet engines, fuel systems, and hydraulic systems. Jet engines operate at extremely high temperatures, and o-rings must be able to withstand these temperatures without breaking down or losing their sealing properties.
Similarly, fuel and hydraulic systems also operate at high temperatures and pressures, and high-temperature o-rings are necessary to prevent leaks and ensure the proper functioning of these systems.
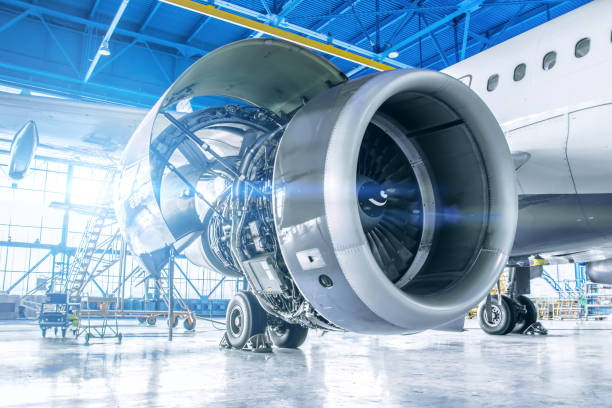
O-rings used in the aerospace industry meet stringent safety and performance standards set by regulatory bodies, such as the Federal Aviation Administration (FAA) and the European Aviation Safety Agency (EASA).
2. Automotive Industry
In the automotive industry, high-temperature o-rings are used in a variety of applications, such as engines, transmission systems, and exhaust systems. A vehicle engine generates a significant amount of heat and o-rings are used to seal its various components, such as cylinder heads and oil pans.
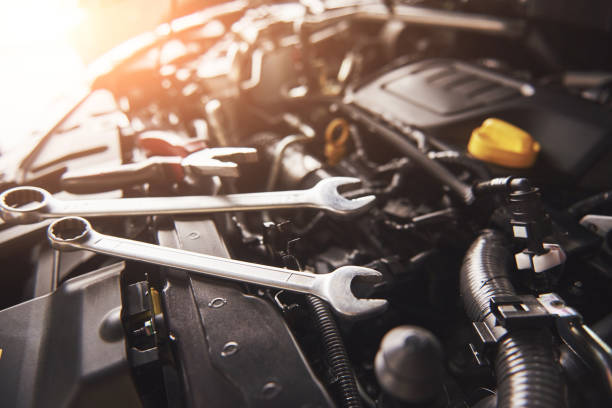
Transmission systems require o-rings to seal fluid passages, while exhaust systems require o-rings to prevent leaks and maintain proper pressure.
The o-rings used for this application help to withstand high temperatures without losing their elasticity or becoming brittle.
3. Mechanical Engineering
In mechanical engineering, high temperature o-rings are used in a variety of applications, ranging from pumps and valves to seals and gaskets. In pumps and valves, o-rings are used to create a seal between moving components, preventing leaks and ensuring that fluids are properly contained.
In seals and gaskets, o-rings are used to prevent the leakage of fluids or gases under high-pressure and high-temperature conditions.
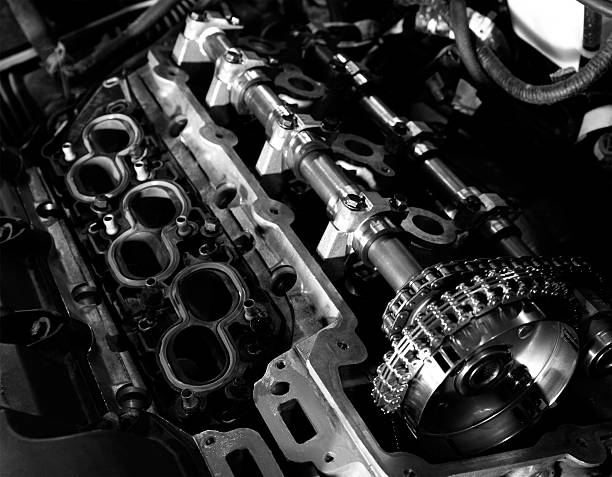
O-rings used for this application are resistant to harsh chemicals, heat, wear, and tear.
4. Electronics & Semiconductors Industry
In the electronics and semiconductors industry, high-temperature o-rings are essential components in various applications such as vacuum chambers, wafer processing equipment, and furnace tubes.
In vacuum chambers, o-rings are used to maintain a vacuum seal and prevent leaks. In wafer processing equipment, high-temperature o-rings prevent contamination of wafers and ensure proper containment of process gases. In furnace tubes, o-rings seal off the high-temperature furnace environment from the external atmosphere.
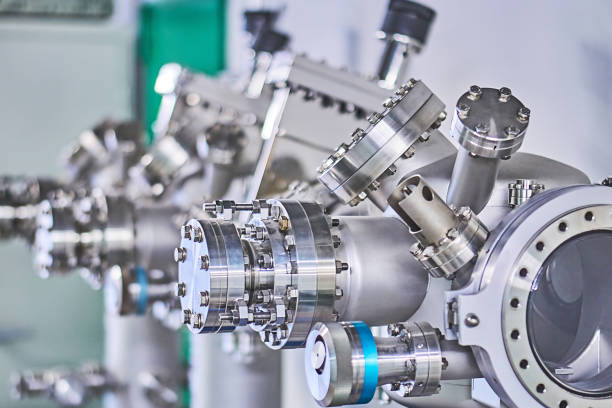
O-rings used for this application can withstand high temperatures, pressures, and chemical exposure, and maintain their elasticity and sealing properties over time.
5. Oil & Gas Industry
In the oil and gas industry, high-temperature o-rings are used in various applications, such as in downhole tools, wellheads, and valves. Downhole tools are used in drilling operations, and o-rings are used to seal various components, such as the drill bit and the drill string.
Wellheads and valves also require o-rings to maintain a proper seal and prevent leaks, which can be costly and dangerous in the oil and gas industry.
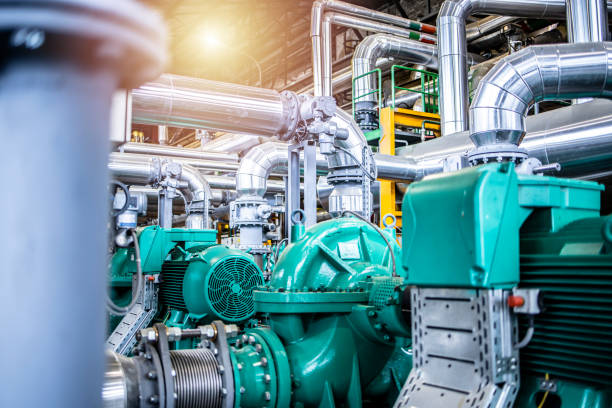
O-rings used for this application can withstand high temperatures and pressures, extreme chemical exposure, and are resistant to abrasion, erosion, and compression set.
6. Medical Equipment Making
In the medical equipment industry, high-temperature o-rings are used in various applications such as sterilization equipment and medical pumps. Sterilization equipment requires o-rings to maintain a proper seal and prevent leaks during the sterilization process. Medical pumps require o-rings to create a seal between moving components, ensuring the proper functioning of the pump.
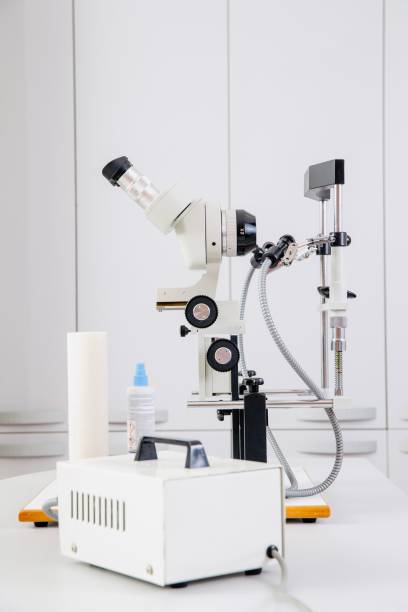
The o-rings used for this application can withstand high temperatures and pressures and are resistant to chemical exposure and sterilization processes.
7. Food & Beverage Production
In the food and beverage industry, high-temperature o-rings are used in various applications, such as in processing equipment, valves, and seals. Processing equipment requires o-rings to prevent contamination of the food or beverage and ensure that the process gases are properly contained. Valves and seals also require o-rings to prevent leaks and maintain proper pressure, ensuring the safety and quality of the food or beverage being produced.
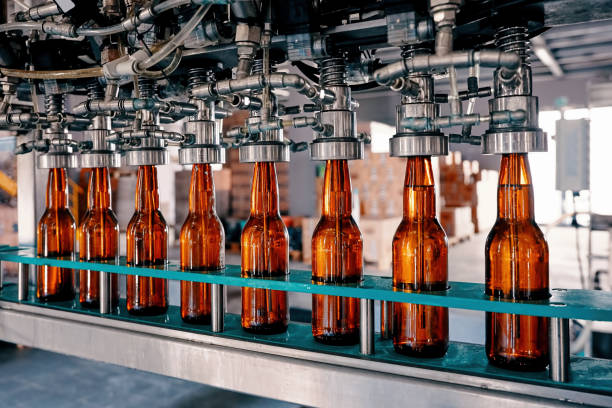
O-rings used for this application are compliant with the Food and Drug Administration (FDA), resistant to chemical exposure, and can withstand high temperatures and pressures.
A Reliable High Temperature O-rings Services Provider: Dechengwang
With over a decade of experience as a leading manufacturer of high temperature o-rings, Dechengwang serves as an all-around solution provider to heat-resistant o-rings needs, including custom designs and precision specifications.
Having a professional R&D team with expertise in bringing all ideas and concepts to life, and a fully-equipped production base with state-of-the-art machinery, we make use of the best high-temperature o-ring materials to suit each demand.
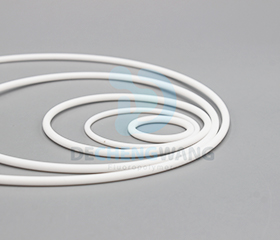
Our capabilities extend to the manufacturing of both o-ring and back-up rings. While the o-ring is singularly highly-functional, the backup ring gives an improved performance double-acting seal. They have extraordinary properties like great resistance to high temperatures, chemicals, corrosion, etc.
All production processes starting from the input of the o-ring materials up to the finished products are conducted with strict compliance with quality management standards, including the IATF 16949 and ISO 9001. This ensures that they have unmatched quality and are suitable for use across all applications.
Our expertise cuts across various industries, including aerospace, automotive, mechanical engineering, electronics & semiconductors, oil & gas, medical equipment, and food & beverage.
Conclusion
Having an o-ring installed in mechanical systems is not the perfect solution to ensure smooth functionality. It must be resistant to high temperatures, which is usually the cause of faulty sealing that results in exposing the system to deterioration. Hence, the essence of using a high temperature o-ring.
In addition to the production of quality o-rings and backup rings, Dechengwang offers a wide range of other compression molded and precision-machined fluoropolymer components, which include seals, bellows, ball valve seats, insulators, labware, and bushings. Contact us for all your fluoropolymer component needs, as well as professional advice to boost your business success.