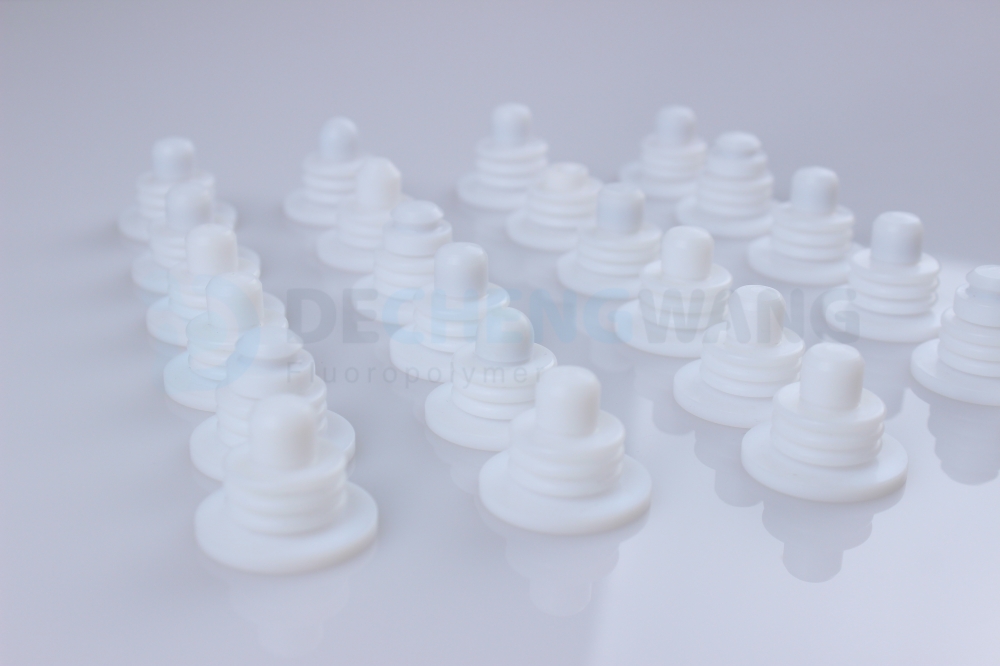
Applications: PTFE Bellows seals for valves
Bellows Mechanical Seal are a type of mechanical seal where the spring element is a bellows. They are a critical component in preventing fluid or gas
An O-ring is a mechanical gasket in the shape of a ring, typically made of elastomer, used to seal fluid or gas leaks in devices and systems. O-rings are one of the most common seals used in industry and can be found in everything from faucets to aircraft engines.
When choosing an O-Ring, there are several factors to consider, such as temperature, chemical resistance, and size. However, one of the most important considerations is the o ring material types. This is because the material can have a significant impact on the performance of the O-Ring. In this blog post, we will provide a selection guide for o ring material guide so that one can make the best decision.
Nitrile o ring material is a synthetic rubber commonly used in industrial and medical applications. They are known for their resistance to chemicals, heat, and wear and can be used in various settings. One of the key benefits of nitrile O-rings is their temperature range. They can be used in both low and high-temperature applications. Nitrile O-rings can withstand temperatures as low as -65 degrees Fahrenheit and as high as 250 degrees Fahrenheit.
Nitrile O-rings should not be used with automobile brake fluid ketones, phosphate esters, hydraulic fluids, halogenated and nitro hydrocarbons. Be aware that nitrile’s weather and ozone resistance are not 100% reliable; however, it is enhanced by compounding. Nitrile can be used in situations that have low-temperature requirements and resistance requirements.
Silicone O-rings are great for steam, water, or petroleum fluids. They are often employed in high-temperature ports for fuel injection. Silicone o ring temperature range from -84 to 232 deg celsius. However, silicone O-rings have been demonstrated to withstand temperatures as high as just 115° Celsius in short exposure. However, silicone has weak wear resistance, abrasion resistance, and Tensile strength. This makes it better for static, not dynamic applications. They can be used with steam, water, or petroleum fluids.
The material is synthetic rubber with outstanding chemical resistance as well as thermal resistance. The EPDM high temperature o rings are between -65 degrees Fahrenheit to 300 degrees Fahrenheit, which is suitable for applications that require exposure to sunlight and ozone weathering, hot water streams, aviation and automobile brake fluids, certain bases and acids, ketones, alcohols, and ketones for plumbing applications. EPDM is not suitable for use with petroleum oils or fuels.
One of the most important properties of PTFE is its density. PTFE is very dense, with a specific gravity of 2.2. This means that it is almost twice as dense as water. This property makes PTFE compounds an ideal material for applications where weight is a concern, such as in aircraft components.
PTFE O-rings are seals with a PTFE composite material construction. The PTFE material provides superb chemical resistance and low friction properties. O-rings made of PTFE can be used in various applications, from food processing to automotive manufacturing. They can also operate in the temperature range between -73 to 265 degrees Celsius. Pure PTFE products are stiff and difficult to apply and remove, making them better appropriate for static applications. O-rings made of PTFE are typically used in steering devices for automobiles and paint guns.
Viton is a kind of all-rounder material that can handle a wide range of applications, including sealing jobs that involve movement. It can be used to seal silicone fluids, gasses, oils, acids, and some halogenated carbons. Viton(r), O-rings can be used in chemical processing, automobile, and instrument applications. It cannot be used with Skydrol, amines, esters, low molecular weight ethers, or hot hydrofluoric acids.
HNBR, an acronym for Hydrogenated Nitrile Butadiene Rubber, has rapidly grown in popularity over the past years because of the high temperature o ring material and outstanding balance of cost/performance and can be used for favorably challenging applications like automotive, industrial, and other applications that need high-performance. The temperature range of the HNBR O–ring is -30degC up to +150degC (-20degF up to +302degF).
They are known for their high resistance to wear and tear and ability to withstand high temperatures. HNBR o rings are an excellent choice for many sealing applications, but there are some limitations to consider before using them.
HNBR o rings are not chemically compatible with all materials. Before using them, it is important to check that the material they will be contacting is compatible with HNBR. Additionally, HNBR o rings should not be used in applications with a risk of them coming into contact with strong acids or bases.
Polyurethane is a thermoplastic material with an operating temperature of 60 degrees F up to 200 degrees F. It’s renowned for its overall toughness and resistance to extrusion and abrasion. It is in gasoline oils and oxygen/ozone chlorinated solvents. Polyurethane O-rings are used in hydraulic fittings, valves, cylinders, firearms, and pneumatic tools. It’s not recommended for acid, ketones, and water-based products.
Rubber o-rings are small, elastomeric components that are used to create seals in a variety of applications. Commonly used in plumbing and automotive applications, o-rings provide a simple yet effective way to prevent leaks. O-rings are available in various sizes and material compositions to suit the application’s specific needs. The temperature range for rubber O-rings is -55 to 300 degrees Fahrenheit. That means that these seals can be used in various applications, from cold weather to high temperatures. As for limitations, rubber O-rings can be susceptible to damage from chemicals and other substances. They also have a limited lifespan and will eventually need to be replaced.
Carbon steel o rings are strong and durable. They’re also resistant to corrosion and can withstand high temperatures. However, carbon steel o rings are not as flexible as stainless steel o rings and may not seal as effectively. Stainless steel o rings are more flexible than carbon steel o rings and provide a better seal. They’re also less likely to corrode. However, stainless steel o rings are not as strong as carbon steel o rings and may not withstand high temperatures as well.
Carbon steel and stainless steel O-rings have different temperature ranges and limitations. Carbon steel O-rings can be used in a temperature range of -20 to +85 degrees Celsius, while stainless steel O-rings can be used in a temperature range of -50 to + 315 degrees Celsius. There are also different pressure limitations for each type of O-ring. Carbon steel O-rings can withstand up to 40 MPa, while stainless steel can withstand high pressure o rings of up to 100 MPa.
Carbon steel rings are often used in heavy-duty applications where stainless steel might not be able to withstand the wear and tear. On the other hand, stainless steel rings are often used in food-related applications where contamination is a concern.
AFLAS o-rings are made of a fluoroelastomer copolymer and are used in a variety of applications where resistance to high temperatures, compression set, and chemical compatibility are required. AFLAS o-rings have a temperature range of -30°F to 400°F (-34°C to 204°C) and are suitable for use in a variety of fluids, including oil, water, and air. They are also resistant to a variety of chemicals, including most acids, bases, and solvents. However, AFLAS o-rings are not recommended for use in highly corrosive environments or in applications where high mechanical stress is expected.
Neoprene o-rings are one of the most versatile types of o-rings on the market, with a wide temperature range and good chemical resistance. However, they are not suitable for all applications.
Neoprene o-rings are made from a synthetic rubber compound, giving them good resistance to various chemicals. They can also withstand a wide range of temperatures, from -40°C to 120°C. However, neoprene o-rings are unsuitable for applications with a lot of friction, as they can be damaged by abrasion.
O-rings are an important part of many machinery applications. They help to seal connections and prevent leaks. There are many different types of o-rings made from different materials. The choice for o-ring material should be based on the application it will be used for. To do this, consider the operating conditions, such as temperatures and pressures, and compatibility with the fluids that will be present.
Dechengwang has provided high-performance PTFE O Rings and custom-made PTFE components for many years. Available in standard sizes from stock or custom cut, these Oring and other specific seals are offered in a range of materials. Contact our experts to get more information and free quotes.
Bellows Mechanical Seal are a type of mechanical seal where the spring element is a bellows. They are a critical component in preventing fluid or gas
In the world of engineering and manufacturing, where precision and efficiency are paramount, the role of wear resistance plastic has evolved far beyond their conventional image.
PTFE is a versatile polymer with outstanding properties like chemical resistance, low friction coefficient (self-lubricating), non-stick nature, and excellent electrical insulation. However, it also has some