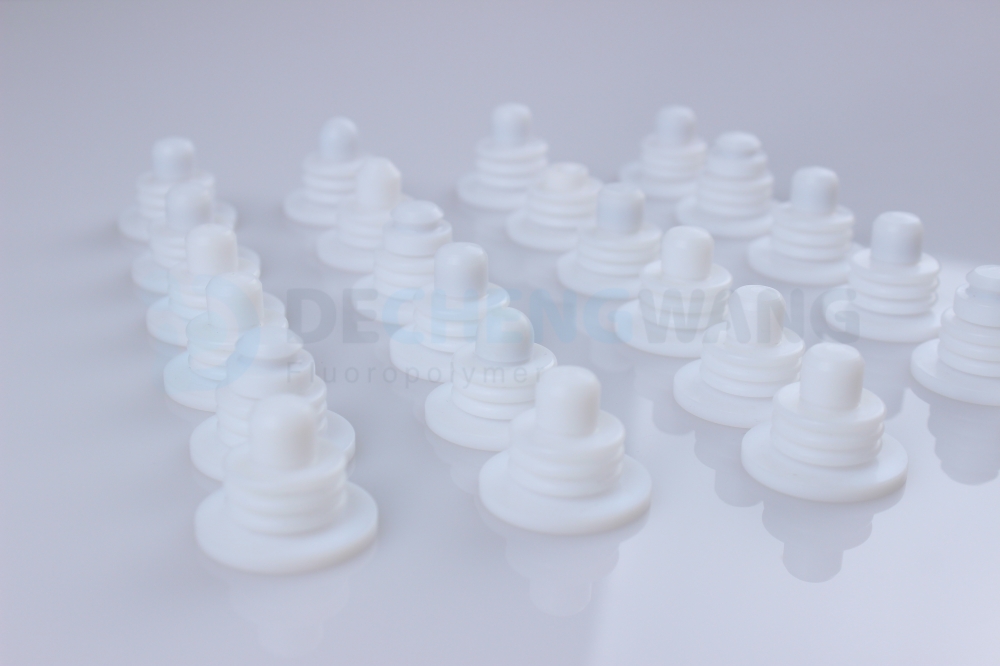
Applications: PTFE Bellows seals for valves
Bellows Mechanical Seal are a type of mechanical seal where the spring element is a bellows. They are a critical component in preventing fluid or gas
Most mechanical systems, especially engines, refrigerators, boilers, and many more require seals to function optimally for a long period of time. However, the type of material used to make the seals determine how effective they will operate. This is why reliable seals like PTFE seals are promoted because they are made of PTFE polymers that provide 100% functionality and have a long lifespan.
While there are different materials used in making seals, there are several types of seals of which the most common one is O-Ring. Just like other seals, O-ring prevents leakage in machinery. But there is more to it. In this post, we will tell you all you need to know about O-Ring, starting from what it is, how it works, its merits & demerits, the types, and so on.
An O-ring is a doughnut-shaped ring that’s made from different types of materials, including elastomers, rubbers, compounds, and other thermoplastic material.
This hollow and solid shape device is used to close the path that could let gas or liquid escape, and also to prevent foreign components from entering the machinery. The O-ring is inserted into a groove to hold them in place, after which they are compressed between two surfaces. When you squeeze the O-ring, it becomes stuck, thereby sealing the passageway the liquid and gas are trying to pass through.
When the machinery is under high pressure, the O-ring is squeezed against the opposing wall of the groove, thus maintaining a perfect seal. When the pressure is reduced, the O-ring, which is commonly made of flexible materials, returns to its default size, thereby providing a tight seal regardless of the amount of pressure.
An O-ring seal is a device used to prevent the loss of fluid and gas. It’s made up of an O-ring and a gland.
The O-ring is a round cross-sectional ring made from different materials (polymers and compounds). The gland, on the other hand, is a cutout metal or another hard material that’s used to embody and support the o-ring.
Other properties and performance include low friction, great dimensional stability, good insulating qualities, outstanding sterilization resistance at high temperatures, biocompatibility, durability, and inherent purity.
As earlier said, O-rings are doughnut-shaped devices that are inserted between two different components to form a tight seal. They can be likened to a standard gasket, although O-rings are specifically designed for industrial applications where they will be exposed to harsh temperatures & pressures, abrasive substances, and other foreign substances. O-rings are made of strong materials, which make them capable of enduring extreme conditions.
O-rings work by being inserted into the groove (which in industrial terms is called the gland) between two components of machinery, which can either be static or dynamic. When the two components are pushed against each other, the O-ring conforms to the shape formed, thereby creating a tight seal that won’t allow water or even air to pass through. The higher the pressure exerted on the O-ring, the tighter the seal becomes.
However, it’s important that the pressure put on the O-ring is not too much, else it will become damaged and the seal will be loosened.
O-rings can also return to their original round shape after the two compressed components of the machinery have been detached and the pressure applied on them are released. Thanks to this, they can be reused. But they cannot be recycled forever; they will become weak after several uses. Eventually, the pressure applied on them will negatively affect their efficiency, necessitating their replacement in order to maintain an impeccable seal.
O-rings have so many features and characteristics. Here are the most important ones.
For static and cylinder cases, O-rings can seal up to 5,000 psi of fluid pressures. The pressure can either be constant or fluctuating.
Also, at any fluid pressure up to 5,000 psi, they can properly seal between reciprocating pistons and cylinders. However, there might be minor running leakage depending on the hydraulic medium’s capacity to produce films.
A single O-ring will seal when pressure is alternately exerted to one side and then the other. In cases where it’s used in unfavorable environments or with heavy loading, the seal life can be prolonged by designing it in such a way that each seal is exposed to pressure on one side only.
For perfect sealing, the O-ring should be squeezed in-between the cylinder wall and the bottom of the seal groove.
The major reason for seal failure is extrusion of the seal material into the piston-cylinder clearance. The primary causes for this are seal hardness & strength, fluid pressure, and the piston-cylinder clearance.
Some O-rings tend to fail due to abrasion against the piston walls or the cylinder. To ensure long seal life, the contacting surfaces should be polished.
It doesn’t matter how the seal groove is shaped as long as it's properly compressed between the under of the groove and the cylinder wall, as well as provide space for the compressed material to flow.
Without altering the seal design limitations, it can be installed in a groove that has been carved into the cylinder wall as opposed to the piston surface.
The chemical interaction that exists between the seal and the hydraulic medium can have a positive or negative impact on the seal’s durability. However, this depends on the combination of the seal material and fluid.
O-rings can seal under various pressure, temperature and tolerance conditions.
Simple to use; no need to retighten.
No complex torque is applied while tightening, making structural damage unlikely.
O-rings are lightweight, portable, and require little space.
An O-ring has the benefit of being re-used unlike non-elastic flat seals.
The lifespan of the O-ring when used for the appropriate application is the same as the normal aging period of the O-ring material.
O-ring failure occurs gradually and it’s visible, thereby alerting the user.
O-rings are cost-effective.
Despite the wide range of benefits that O-rings offer, they have some limitations. Here they are:
Rotary speeds of more than 1,500 feet per minute.
An unconducive environment for the O-ring material.
Chemical, temperature, and pressure incompatibility.
Whether you need an O-ring seal for heavy-duty agricultural machinery, the cogs & pistons of the automotive industry, or in any other industry, there are definitely options perfect for your application. Below, you will find the different types of O-ring seals and their possible applications.
Nitrile O-rings, which is otherwise called Buna-N or NBR, is a general-purpose type of seal. It provides a decent range of temperature, which is within -50oC and 120oC, as well as an outstanding resistance to tears and abrasion. Also, nitrile has good resistance to fluid, oils, and some hydraulic liquids. However, it can’t withstand automotive brake fluid, ketones, halogenated hydrocarbons, and nitro hydrocarbons.
As a result, it can be used for a limited number of applications in the agricultural sector, the automotive sector, as well as the diary, mining, plumbing, and railway industries.
Neoprene, which is a general-purpose elastomer, is quite unusual in the sense that it has a moderate resistance to petroleum oils and weather, including ozone, oxygen, and UV. This is why neoprene O-rings are ideally suitable for some sealing operations that other types of O-rings can’t handle. It’s also resistant to flex cracking, has an excellent resilience and abrasion rating, as well as a relatively low compression set.
Neoprene has the same temperature capability as nitrile and is often used to seal refrigerants in air-conditioning systems and refrigeration units.
Silicone O-rings have one of the broadest ranges of temperature amongst other types of O-rings. It can withstand temperatures ranging from -100oC to 300oC. This resilient O-ring is the perfect option for situations where extremely high or low temperatures will be used. In fact, it has been reported to withstand as much as -115oC to 315oC for a short period of time.
Although it is very flexible and works well with water, steam, and petroleum, it is vulnerable to tears and abrasions. As a result, it is preferably used for static applications instead of dynamic ones.
They are also called FKM O-rings. They are made from fluorocarbons, and boast of a temperature resistance range of -40oC up to 250oC, excellent mechanical properties, low gas permeability, and a low compression set. Viton O-rings can be used with acids, petroleum & silicone fluids or gasses, as well as halogenated hydrocarbons. But they aren’t suitable with anime, esters that have a low molecular weight, skydrol, and hot hydrofluoric acids.
Their application cut across many industries, such as the aviation, automotive, chemical processing, and mechanical engineering plants industries.
PTFE machined parts with corresponding O-rings enjoy a lot of benefits, which make them perform their functions optimally and last long. Some of the benefits the O-rings offer are good wear, corrosion and abrasion resistance, non-permeability, chemical inertness, and low absorption. They can also function at a wide range of temperatures, from -73oC to 260oC.
PTFE O-rings are usually used for making paint guns, and in the automotive industry for steering devices.
These types of O-rings are formed from the combination of a silicone or fluorocarbon core with a coating of Fluorinated Ethylene Propylene (FEP). These O-rings can withstand temperatures ranging from -20oC to 204oC for fluorocarbon cores, and -60oC to 260oC for silicone cores. Also, they provide exceptional flexibility and low friction levels.
Even though they are most preferably used for static operations, they can also be used for dynamic operations where the movement is slow and short. This is why they are commonly used in the chemical, food & beverage, petrochemical, and pharmaceutical sectors.
Perfluoroalkoxy (PFA) O-rings are a desirable substitute for PTFE and FEB O-rings. PFA O-rings are more affordable than PTFE, and they offer stronger resilience with temperatures above 250oC than FPE. It’s perfect for use in the food industry, pharmaceutical industry, and the chemical & petrochemical industry.
These are the basic materials used in making O-rings.
In simple terms, a polymer is the outcome of a chemical linking of molecules in a long chain-like structure. Both plastics and elastomers are classified as polymers. Examples of O-rings made from polymers are nitrile, neoprene, and PTFE O-rings.
The term, “synthetic rubber” was initially used to describe rubber-like compounds that were produced from sources other than rubber trees. This sets them apart from natural gum rubber. However, since then, rubber has been defined to cover both synthetic and natural materials with rubber-like properties.
The word “elastomer” is being used interchangeably with the word “rubber.” However, they are quite different. Elastomer is described as any rubber material that’s composed of long chain-like polymers that can go back to their original shape after being stretched to a great extent.
A compound is defined as the mixture of base polymer and other chemicals to produce a finished rubber material. It can also be referred to as a unique combination of chemical elements designed with some specific properties to maximize performance of operations.
These are some of the several industries where O-rings are used.
Transportation industries like automotive, aerospace, and heavy duty trucking require the use of extremely high temperatures, exposure to chemicals, and vibrations, which can be contained by O-rings. They are also used for the engines, brake systems, fuel systems, liquid rocket propellants, etc.
In the medical industry, several equipment require o-rings to function. Some of them are syringes, pumps, filtration devices, and connectors.
Applications in the oil and gas industry are usually challenging due to the consistent contact with aggressive media, high pressures, wide range of temperatures, chemicals and additives, etc. Thus, the use of o-rings to resist all challenging elements.
The Food and Drug Administration (FDA) has a list of materials that can be used for preparing and processing food & beverages, of which O-rings materials are enlisted. They are non-cancerous and don’t harm the human body in any way. Also, they help to prevent wastage and prolong the lifespan of cooking items.
The way an O-ring is installed determines its functionality in the machinery. Therefore, knowing the proper way to install an O-ring without causing any damage to it or any part of the machine is beneficial. If O-rings are not installed properly, it’s only a matter of time before they start tearing, thus an avenue for leakages and foreign materials to enter the machine.
There are a few basic approaches you need to take to install an O-ring properly. They are discussed below.
Despite the fact that O-rings are mostly made to be flexible and elastic, it is pertinent that you have the correct size that will fit into the groove. This is not only important, but necessary if you want your application to be successful. If the O-ring is smaller, it will tear as a result of stretching, and if it’s too large, it won’t provide a tight sealing.
Don’t buy the wrong size and try to stretch it to fit into place. Even if it works the first time, the lifespan of the O-ring will reduce, and after a few usage, it will begin to tear.
Even though O-rings are mostly made from elastomeric materials, and they support some degree of stretching, they shouldn’t be overstretched. They become weak and vulnerable when they are elongated above the maximum rate. The stretch shouldn’t exceed 1% to 5%, with 2% being the most appropriate in many cases.
O-rings will perform more effectively and have a longer lifespan when a thin layer of lubricant is applied on them. This simple act helps shield the O-rings from damage. Also, it allows the O-rings to fit easily, avoid drying out, and lower tension between the surfaces.
O-rings should be slid to fit into place, rather than being rolled down. When O-rings are rolled down the shaft, there will be spirals, which will reduce the rate at which they will function. And when an O-ring has a spiral wound, it will easily get damaged, causing further leakage. To prevent this, the O-ring should be properly lubricated so that sliding it into place will be easy.
Sometimes, you would have to install an O-ring into parts with sharp edges that can cause damage to the O-ring if care isn’t taken. In cases like this, you should cover the edges with masking tapes or any other material, and then apply lubricants on them, so that the O-ring will easily slide in.
These are the factors that should be considered in designing and choosing an O-ring type.
The first factor to take into consideration is the compatibility between the O-ring and the fluid(s) that need to be sealed. If this is not ascertained, then there’s no need going on with using the O-ring. You have to know if there will be an immediate negative effect when the O-ring comes in contact with harsh chemicals or if it will be a gradual effect.
In cases where the O-ring will be in contact with more than one fluid, the sequence of exposure and the time of contact should be considered.
The system temperature may require some little changes to the gland design. The gland volume will need to be increased if the operation will only be performed using high temperature. This compensates for the thermal expansion for the O-ring.
On the other hand, for operations that are solely at low temperatures, reducing the gland depth will produce a better seal, thereby ensuring that the contracted O-ring is properly squeezed.
The design of O-ring seals is influenced by pressure as it has an impact on the choice of compound shore hardness. Tight sealing with low durometer hardness can be obtained at very low pressures. While at higher pressures, the maximum clearance that may be safely allowed is determined by the interaction between pressure and material shore hardness.
Extrusion of O-rings can be stopped by using anti-extrusion (back-up) devices. These are tiny rings made of hard materials. They are inserted into the gland between the seal and the clearance gaps, thereby providing no clearance.
Lubrication of O-rings is important to get an appropriate seating of static seals, and the proper installation and operation of dynamic seals. The most beneficial stage to apply lubricants on O-rings is at the installation stage. Using lubricants on O-rings during this stage, protect them from damage that could be caused by cutting, pinching, or abrasion.
Additionally, lubrication facilitates accurate O-ring seating, quickens assembly processes, and enables automated assembly line procedures.
Dechengwang provides custom PTFE O-rings that are customized to suit different applications. The O-rings possess outstanding properties that make them resist all forms of harsh chemicals, and also maintain a tight seal. We have a wide range of manufacturing capabilities, making us to provide O-rings for several industries, including aerospace, automotive, food & beverages, medical, etc.
Asides being one of the best PTFE components manufacturers who provide unique PTFE O-rings products and services, we also produce products with other polymers, such as PEEK, PVDF, PFA, and PCTFE. Some of the other products are insulators, bellows, labware, bushings, tubes, rods, films, and sheets.
O-rings are doughnut-shaped equipment that are used with machines. They are important equipment that are compressed between two surfaces to ensure the optimal functionality and durability of machines. They are used in many industries to boost workflow and ease.
Having enlightened you about all you need to know about O-rings, you can now make an informed decision on how to make your machine last longer and boost your workflow. For more inquiries, you can contact us for more clarity.
Bellows Mechanical Seal are a type of mechanical seal where the spring element is a bellows. They are a critical component in preventing fluid or gas
In the world of engineering and manufacturing, where precision and efficiency are paramount, the role of wear resistance plastic has evolved far beyond their conventional image.
PTFE is a versatile polymer with outstanding properties like chemical resistance, low friction coefficient (self-lubricating), non-stick nature, and excellent electrical insulation. However, it also has some