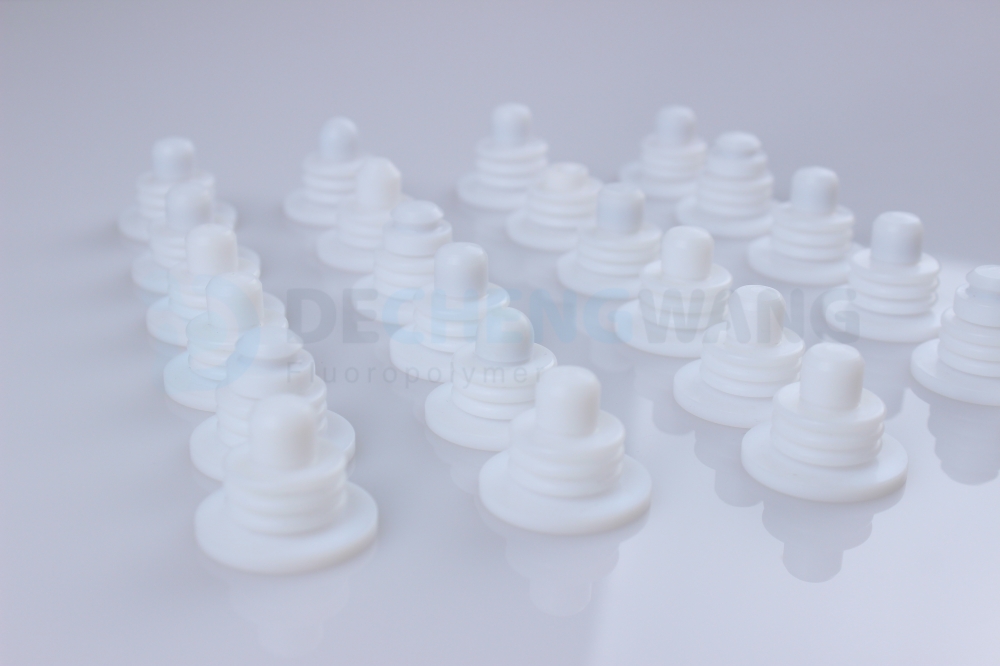
Applications: PTFE Bellows seals for valves
Bellows Mechanical Seal are a type of mechanical seal where the spring element is a bellows. They are a critical component in preventing fluid or gas
PTFE, which is also known as “Teflon” is a very odd material because it’s a thermoplastic material, but functions as a thermoset. While other thermoplastics can be recycled after initial molding, PTFE cannot. Also, while PTFE temperature range is -400 to +550 degrees Fahrenheit, it begins transitioning at several points, meaning that the PTFE material moves as a result of thermal changes.
With PTFE temperature limit being -400 and the maximum temperature at +550, it can maintain structural integrity and perform perfectly at extreme temperatures. The only thing is that you need to keep an eye out for possible shrinkage. When the Teflon temperature limit is too low, the PTFE parts can shrink beyond your dimensional tolerance.
Teflon’s maximum temperature is 500 degrees Fahrenheit, which makes it one of the most popularly used fluoroplastic materials, even though its mechanical properties are low compared to some notable engineering plastics. However, the Teflon temperature range makes it suitable for many applications.
PTFE is amongst the best thermally stable plastics. It does not decompose easily, not until it’s put under a very high temperature. The temperature affects the linear thermal expansion coefficient. Due to the orientation of the working process, the expansion coefficient varies with respect to direction.
However, the thermal conductivity does not change with temperature. It is quite high, which is why PTFE is considered an effective insulator. And the thermal conductivity can be improved by adding suitable fillers.
PTFE is very strong and resistant to other elements and compounds. However, it can be attacked by alkaline metals in their elementary condition, Chlorine trifluoride, and elementary Fluorine at high pressure. High-energy radiation is capable of breaking PTFE molecules, which makes the plastic material resistance against radiation quite weak.
The permeability of PTFE is comparable to that of other plastics. The permeability of a material is determined not only by its thickness and pressure but also by the methods used in its manufacturing process.
PTFE is a thermoplastic polymer with a white solid at room temperature, and it has a melting point as high as 500 degrees Fahrenheit. It is capable of maintaining its high strength, hardness, and self-lubrication at a low temperature like -400 degrees Fahrenheit and suitable flexibility at temperatures over -110 degrees Fahrenheit.
All fluorocarbons, including PTFE, get their properties from the combined impact of carbon-fluorine bonds. And the only chemicals that can affect these carbon-fluorine bonds are highly reactive metals, such as alkali metals.
PTFE properties are maintained unless the temperature is extremely increased, which can result in melting. Also, it depends on the nature of the fillers used. For instance, at normal temperature, virgin PTFE has a tensile strength of 4075 psi, but once the temperature is increased to 500 degrees Fahrenheit, the tensile strength reduces to just over 1000 psi.
As an analogy, a carbon graphite-filled material possesses a tensile strength of 3300 psi at normal temperature, but when the temperature is increased to 500 degrees Fahrenheit, the tensile strength will reduce to 990 psi.
At the same time, elongation numbers will be affected. At normal temperature, virgin PTFE has an elongation of around 330 percent, but it becomes just 210 percent when the temperature is increased to 500 degrees Fahrenheit.
Before deciding on the Teflon operating temperature, you need to consider the benefits of placing your temperature at that rate, as well as the part you are trying to make and the required temperature.
The Teflon temperature range is very crucial for a PTFE products manufacturer in the design of high-temperature seals, bearings, and even structural components. The set temperature range determines if your manufactured part will be what you desired or way beyond your dimensional tolerances.
When you consider the thermal conductivity and thermal expansion of Teflon material, you will realize how important it is to have the right temperature before the start of your manufacturing process.
Below are examples of parts made from PTFE and the requirements.
Bellows: PTFE bellows are usually used in chemical, food, and medical applications as balancing elements between engineering parts. The different geometries of the folds can be designed and fabricated in extremely flexible or pressure-resistant variants to provide higher flexibility or compressive strength.
The number of runs, external and internal pressure, and all-closed/all-opened lengths are all important aspects to consider while building a bellow.
Ball valve seats: PTFE ball valve seat is frequently used as the raw material for valve seats and inserts, which are crucial components in the valve industry. PTFE has a low friction seat and is compatible with a wide range of media. Filled grades offer more wear resistance and can support heavier weights of the higher class of valves.
O Ring & Back-up Ring: PTFE O rings are commonly used for static sealing purposes in pipes, cylinders, bushings, flanges, stems, and connectors. Some important factors to consider here are chemical and physical inertia, friction resistance, temperature, and aging.
Back-up rings, on the other hand, are not seals, but they are used in high-pressure applications together with O-rings or other seals. They are usually put on the gland’s downstream side, although they can be put on either side of the O-ring for a high-performance double-acting seal.
Insulators: PTFE is frequently used as insulation material due to its exceptional dielectric properties, particularly at high radar and microwave frequencies. PTFE can also withstand temperatures ranging from -180 degrees Celsius to +260 degrees Celsius.
Labware: Because Teflon max temperature can reach 260 degrees Celsius and the remarkable technical features it possesses, such as chemical resistance, it is used in laboratories. Its anti-adhesive, smooth surface together with its hydrophobic behavior guarantees low cross-contamination and cleaning ease.
Seals: PTFE seals make the difference in every closure as it has ultra-high strength, which is suitable for providing sealing solutions to even the most demanding applications.
Bushings: Bushings made with PTFE provide maintenance-free solutions for heavy load and medium speed applications. These bushings have very good frictional properties and high operating temperatures.
PTFE is a very strong plastic material that must be put under a very high temperature for it to decompose. It has a temperature range of -400 to 500 degrees Fahrenheit. However, the needed temperature might vary depending on your applications, so you need to put your needs into consideration and tune the temperature to the best.
Bellows Mechanical Seal are a type of mechanical seal where the spring element is a bellows. They are a critical component in preventing fluid or gas
In the world of engineering and manufacturing, where precision and efficiency are paramount, the role of wear resistance plastic has evolved far beyond their conventional image.
PTFE is a versatile polymer with outstanding properties like chemical resistance, low friction coefficient (self-lubricating), non-stick nature, and excellent electrical insulation. However, it also has some