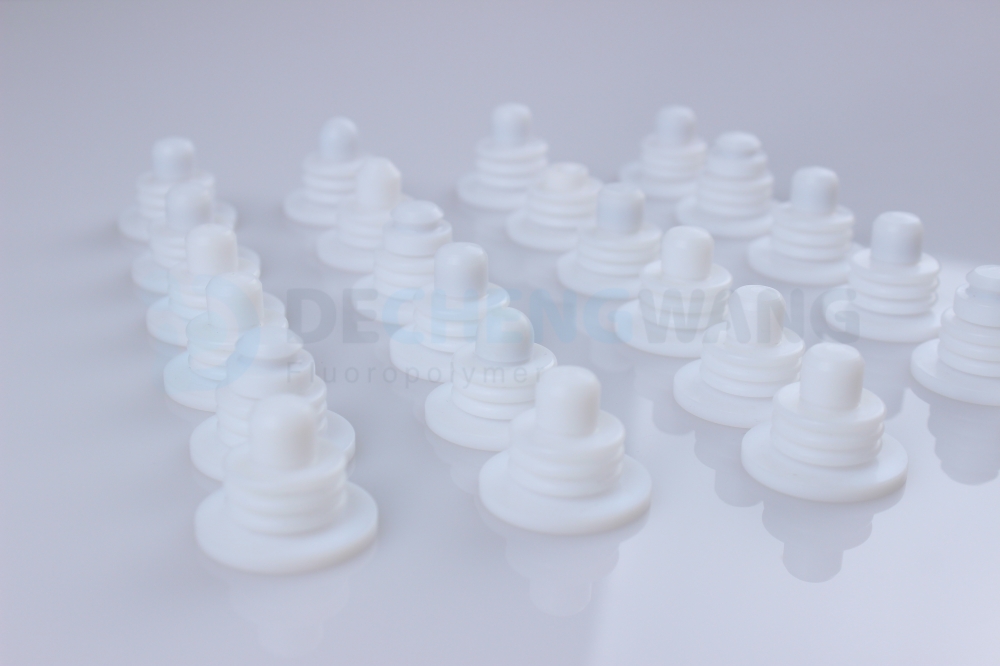
Applications: PTFE Bellows seals for valves
Bellows Mechanical Seal are a type of mechanical seal where the spring element is a bellows. They are a critical component in preventing fluid or gas
Teflon is a spectacular and amazing material used to coat products to preserve and raise their standards. Teflon is a unique and important element used in nonstick cookware coatings. It also has extensive applications in other industries such as automobiles, medicine, and power for similar reasons.
Speaking of Teflon, when you search the term on Google, you will also be met with the term PTFE. Getting results for PTFE products when you were searching for the term Teflon sure confuses you, doesn’t it?
Well, now it won’t since we have dedicated this whole article for you to easily understand the difference between them and why they are coined the same term.
The synthetic polymer PTFE, or polytetrafluoroethylene, comprises two essential elements: carbon and fluorine. It’s made from tetrafluoroethylene (TFE) and has some unique characteristics that make it beneficial in a wide range of applications.
It is a ubiquitous element found on everyday items such as cookware pans, personal care goods, etc.
Like many other revolutionary polymers, PTFE was discovered by accident in a lab. Roy J. Plunkett, a DuPont chemist, devoted his precious time to developing non-toxic refrigerants. Due to unavoidable errors in scientific calculation, he instead invented PTFE which is still used by many industries.
The reason behind the popularity of PTFE parts is that the product is used as a coating element on various products across a multitude of industries.
Here are some of the properties possessed by PEEK materials:
PTFE has a high chemical resistance; the coating does not react with other chemicals when it comes into proximity with them.
PTFE is completely impervious to temperature fluctuations, both high and low. The coating will not melt even if subjected to extremely high temperatures.
Because PTFE has a melting point of 325-335 °C, it can withstand high temperatures without being damaged.
Because of its excellent dielectric qualities, PTFE is the material of choice for coating electric equipment and wires. Electric discharges are prevented by the use of PTFE in the apparatus.
PTFE is used to coat heavy-duty machinery because it can withstand and resist high levels of stress while maintaining the integrity of the material it is applied on.
PTFE has minimal friction, allowing items to slide down without being caught in the middle in manufacturing gear.
The PTFE coating ensures that the product will last for a long time. UV radiation, oxidation, discoloration, or embrittlement do not affect it.
The anti-adhesion qualities of PTFE, which prevent other materials from clinging to it, are among the main and most common reasons it is highly recommended and utilized in cookware products.
PTFE is a hydrophobic component that repels water and is used in coating equipment and materials that need to avoid getting wet.
PTFE materials have specific common grades which are worth looking for:
“Virgin PTFE” refers to PTFE that hasn’t been filtered. It’s one of the most chemically inert materials on the market, and it’s employed in a variety of applications and industries.
Virgin PTFE with a 25% glass fiber filler boosts compressive strength and reduces deformation under load considerably.
Bronze added to PTFE improves dimensional stability and reduces creep, cold flow, and wear.
Carbon Fiber added to PTFE increases compressive strength and wear resistance. It has high thermal conductivity and low permeability.
The material is exceptionally durable, has good strength and stability under extreme loads and temperatures, and retains the low coefficient of friction of traditional PTFE.
Material Name | Compound % | Main Properties | Color |
Glass Fiber | Up to 40% | Improved ware resistance, compression strength, creep resistance, chemical resistance. Good performance in oxidising environment, good creep resistance. | White cream |
Carbon | Up to 35% | Improved electrical and termal conductivity, resistance to load, low coefficient of friction in dry, water, steam applications, chemical resistance. Superior ware resistance increase and low friction properties. | Black |
Graphite | Up to 25% | Improve wear resistance, decrease friction and increase sliding properties against soft metals- chemical inertness. Improve the temperature resistance in some way.
| Black |
Bronze | Up to 60% | Improved compression strength, wear resistant, high thermal conductivity, resistance to abrasion. Reduced chemical resistance.
| Dark Brown |
Molybdenum disulphide(MoS2) | up to 5% | Increased PTFE properties of hardness and wear resistance. Increased sliding properties and decrease friction.
| Blue azure |
PEEK | Up to 20% | Increased thermal resistance, sliding properties, surface hardness. Superior properties on dynamic applications.
| Beige |
PTFE is used in many industries, including the automotive, chemical, electrical, aerospace, and medical fields.
PTFE sheets and thin films are primarily used in the packaging industry. Compared to other commodity packaging materials, a chemically inert substance such as PTFE is worth the extra expense in packing chemical equipment, pharmaceuticals, and cosmetic products.
PTFE can also be used as a machine lubricant. PTFE decreases friction, energy consumption, and equipment wear when utilized in this manner. The lubricant used on bicycle chains is one example of this.
PTFE is frequently utilized to insulate cables and connector assemblies because of its high electrical insulation qualities. It’s perfect for connection wire, coaxial cable, and printed circuit boards because of this.
PTFE is used in industrial coatings around the world. It has a low friction coefficient and is resistant to high temperatures. PTFE coatings and non-stick wear are used on kitchenware to keep food from sticking to pots and pans. PTFE is also used in machining O rings.
Because it is anti-corrosive and non-reactive, PTFE is utilized to build containers and pipes. This is helpful in laboratories where highly corrosive chemicals must be stored in glass containers. PTFE bottles and parts are used in laboratories.
PTFE can be used to cover carburetor parts, ball valve seats, automobile plungers, bypass shafts, and sleeves. PTFE is also utilized as a coating for auto parts and machines. This is due to the parts’ ability to protect themselves from harm even when exposed to extreme heat.
Paste extrusion of fine PTFE powder into usable shapes such as tapes, wires, and tubes is possible. Typical applications are wire and cable insulation, tubing, pipelines, and films. For some materials, PTFE powder can be used as a powder coating to provide a more attractive finish.
PTFE is nonstick and prevents things or food particles from sticking to it. This also makes it easier to clean. PTFE is used in
It is resistant to extremely high and low temperatures.
PTFE is chemically inert to other chemicals, meaning the coating won’t react with them, which is why it’s used in cookware and artificial medical components.
Because of its dielectric qualities, PTFE is a poor heat conductor, which is likely an advantage because it lowers electrical leakage.
Because PTFE coating increases durability and endurance, PTFE-coated products last longer than those that are not.
It has a low refractive index, which means that the product’s appearance will not alter when exposed to light.
Because of its high melting point and auto-ignition temperature, PTFE offers exceptional resistance to high temperatures and flames.
Because PTFE is a polymer or a plastic component, it does not biodegrade quickly, allowing the product to stay longer.
The polymer is often used as a graft material in surgery and as a coating on catheters to prevent bacteria and infections.
Because PTFE is a plastic component, the all-in-one polymer has another crucial advantage: it is water-resistant or water-phobic.
Though PTFE has a plethora of advantages, it also has a significant number of disadvantages that one should look out for:
Teflon is also the same as PTFE. In fact, they are the same product but have different names.
DuPont invented and registered the new fluorinated material under the name Teflon in 1945.
As a result, Teflon is a trademarked brand name for the polymer that is still widely used. Although hardly everyone understands what PTFE is, everyone recognizes Teflon.
Teflon is a form of plastic used in various sectors to coat machinery or equipment to protect the material’s quality and ensure its long-term durability.
When telling your manufacturers that you can use either Teflon or PTFE, they will understand both words. Between PTFE and Teflon, there is practically nothing to compete with because they are both the same. The only difference is the moniker that is used to distinguish them.
Only the name distinguishes PTFE from Teflon, which are both the same material. Though most people may be perplexed by the terms at first, we hope you were able to clear up any ambiguities you had about PTFE and Teflon. If you have, please visit Dechengwang since we offer PTFE materials at reasonable costs that can be negotiated based on your needs and satisfaction.
Bellows Mechanical Seal are a type of mechanical seal where the spring element is a bellows. They are a critical component in preventing fluid or gas
In the world of engineering and manufacturing, where precision and efficiency are paramount, the role of wear resistance plastic has evolved far beyond their conventional image.
PTFE is a versatile polymer with outstanding properties like chemical resistance, low friction coefficient (self-lubricating), non-stick nature, and excellent electrical insulation. However, it also has some