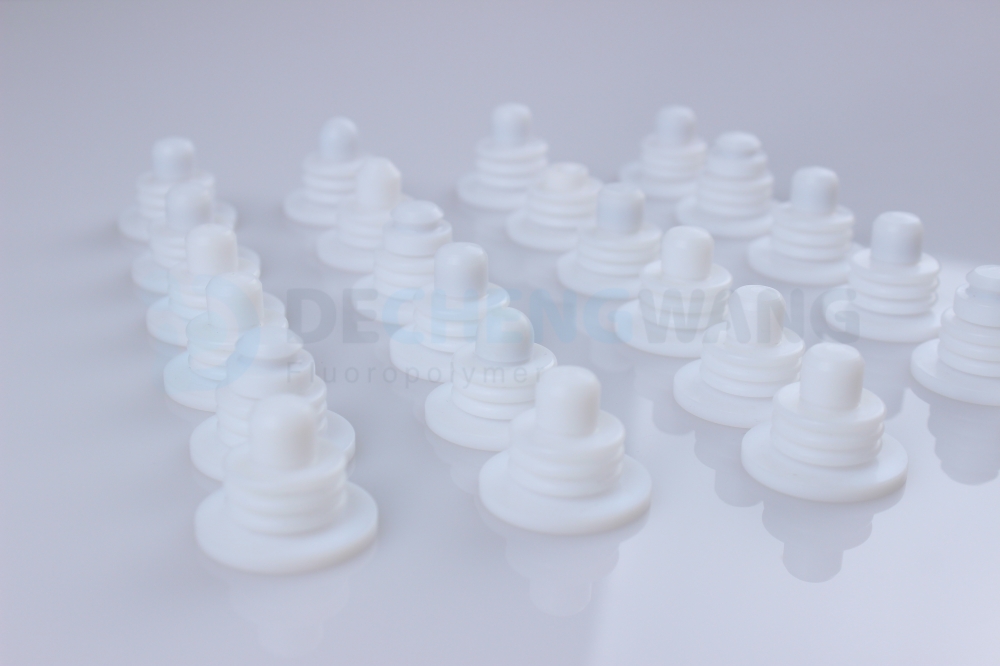
Applications: PTFE Bellows seals for valves
Bellows Mechanical Seal are a type of mechanical seal where the spring element is a bellows. They are a critical component in preventing fluid or gas
Three main fluoropolymers are available for various industries- PTFE, FEP, and PFA materials. PTFE, an abbreviated form of polytetrafluoroethylene, is the first-ever fluoropolymer manufactured. This creation is attributed to the freezing polymerization process. These polymers contain repeating units of fluorine and carbon bonds and are characterized by their immense resistance to extreme chemical and thermal conditions.
Another variety of PTFE is RPTFE, which is also another indispensable fluoropolymer that makes use of different fillings for additional properties. Read further to know about the histories, properties and applications, along with the similarities and differences between these chemically essential fluoroplastics, PTFE and RPTFE.
Expanded form: Reinforced Polytetrafluoroethylene
Definition: RPTFE is essentially defined as a filled PTFE, where several materials are added to exhibit specific molecule characteristics. Their insulation properties are put in practice in products like PTFE insulators. PTFE is a weaker material that deforms when exposed to heavy loads and pressure. While these filler components enhance the sturdiness of the plastic, not all of them are food-grade and safe for food storage.
The common materials are standard glass fiber, carbon, bronze, and other substances. Glass fiber reinforcement is the most usual filling used due to minor variations in properties retaining PTFE’s unique resistance.
These reinforced substances decrease the rate of wear and tear and may have different percentages based on requirement and material use. While glass fiber ranges from 5-40%, carbon fillings usually range from 10-35%. The features of these fillers are as follows:
Many fillers can be substituted with their mechanical properties. Some notable fillers include molybdenum disulfide fillings, graphite (carbon), stainless steel, and glass fiber. Sometimes unneeded properties of these fillings get combined. For this reason, two or more fillers are added to set off one another. Their characteristics are as follows:
RPTFE, where glass fiber is the reinforced component, reduces the wear and tear of the fluoropolymer. It is also responsible for increased load capacity and performance to a certain extent. As they leave the chemical, electrical, and thermal properties unaffected, their reactivity increases when exposed to alkalis and reduces resistance to hydrofluoric acid. RPTFE plays a significant role in initiating and facilitating the use of fiber-reinforced plastics.
Graphite is a common filling material used with these fibers due to the slight hike in friction coefficient.
Carbon (not in the form of graphite) is typically added for its deformation strength properties much needed in PTFE material plastics. They are measured and filled by weight, and the proportions range from 10-35%. It significantly reduces wear and tear and induces electrical characteristics by a considerable degree. As it does not change the chemical properties and resistance, a small percentage of graphite is added.
Bronze fillers range from 40-60% and mark the highest percentage range among all filling materials. It is an excellent reinforcing material for its wear characteristics. It increases deformation strength to substantial degrees and improves thermal conductivity at a remarkable rate. However, bronze is a limiting substance regarding electrical and chemical reactivity. Most PTFE product manufacturers prefer filling products with bronze.
Graphite materials are typically used in small quantities, ranging from 5-15%. As mentioned, a small percentage of graphite is added to glass fiber and carbon fillings to lower friction properties. It is considered the jack of all fillings- It increases load pressure resistance and improves deformation resistance, strength, and wear properties.
Other common filling materials include soft metals in powder form- like steel, titanium, and nickel. Molybdenum sulfide forms a similar alternative to graphite by decreasing the slippery property and friction coefficients. However, most manufacturers prefer graphite reinforcement. Metal powders are inferior to metal oxides in terms of wear and tear properties.
A variety of sectors make use of RPTFE products, which include, but are not limited to:
Fluid Handling: RPTFE products are widely used in pharmaceutical industries for their excellent resistance. Fluid handling applications require heavy exposure to abrasive substances like strong acids, bases, and other aggressive solvents. They have a considerable potential to affect pipelines and tank liners. RPTFE’s additional thermal resistance and protection make it a great contender for chemical-based industries and petroleum sectors. They are also used as fluoropolymer lab equipment.
Mechanical engineering: RPTFEs are indispensable fluoroplastics in the mechanical industries and civil engineering. Filled RPTFE is applicable in solid sealants, bridge bearing, and air compressing processes. Their excellence in this industry is attributable to their surface friction flexibility among fillings and extraordinary wear characteristics.
Electrical sector: When switching gears and capacitors, RPTFE products and materials are extensively used. Their electrical insulation makes them great performers in traction motor generation applications. They are used in nozzles and tubing for aircraft as well.
Reinforced PTFE has added advantages over standard PTFE, which can be attributed to the adaptability of the filling used. Their role in engineering sectors is crucial, and their unique and flexible lubricity makes them second to none. They carry the following benefits:
Reinforced PTFE has a lot of stake in the industry. However, they are disadvantages to the following subject:
Expanded form: Polytetrafluoroethylene
Definition: Widely known under the brand name Teflon, manufactured by DuPont Co. PTFE, is a synthetic form of fluoroplastic with multiple bonds between fluorine and carbon molecules. Its chemical formula is (C2F4)n, n being the number of molecules in the repetitive chain. It is a virgin PTFE where no filling components are reinforced other than the atoms of carbon and fluorine. Its molecular weight is higher, keeping its form solid under thermal room conditions. It does not mix with water or water-containing substances. In other words, it is hydrophobic due to the loss of London dispersion forces.
Domestic households usually own and recognize them in the form of non-stick pans due to their reduced reactivity and hydrophobic stickiness. Its low coefficient of friction makes its slippery nature act as a lubricant in mechanical industries. It’s a poor solvent that’s manufactured through a process called free-radical polymerization. Syncolon and Fluon are also referred to as PTFE but are mainly identified as Teflon. They are often used in the form of PTFE O-rings.
It is interesting to know that PTFE was an accidental creation of a worker named Roy Plunkett. Its discovery happened on the 6th of April, 1938, when Roy worked on improving certain refrigerants. They were required to make an eco-friendly variant of such coolants that used non-flammable characteristics. This required a specific tetrafluoroethylene sample to be frozen.
When the sample was taken out of the freezer, he and his associates found the tetrafluoroethylene sample to be polymerized due to low temperatures. The model underwent free-radical polymerization, responsible for its waxy white solid texture.
In 1947, the trademark made its appearance. Chemours initiated the patent process under the brand name Teflon, and its commercial value increased with its variants.
The following properties characterize PTFE:
Discovered as a mistake, PTFE products have become a crucial asset in every domestic household and industrial manufacturing unit. Their applications ensue but are not limited to:
Liners in engineering: Its inert capabilities make PTFE great for tube lining in manufacturing sectors. Such non-reactive properties are weighted through the fluorine atoms and thus make it perfectly safe for abrasive fluids to travel through PTFE-coated pipelines. Ball valve seatings often require various aggressive fluids to travel through channels and containers. PTFE applications are not limited to handling solvents like these but also serve as an effective coating alternative (which is often the budget-friendlier option).
Non-stick equipment: From the popular domestically used non-stick pans to screws and bearings in industries, PTFE coating makes even chameleons prevent themselves from sticking. Their hydrophobic property is responsible for these characteristics. They were widely used to keep insects away.
Prevention of bacteria: This fluoropolymer is a carrier in the medical industry to prevent bacteria. They are coated against catheters and other surgery equipment to prevent external infections.
Rainwear and other coats: PTFE is what most people see when they wear raincoats that allow breathability. Its paper-thin membrane allows such porous properties, widely found in medical wear, PTFE sealants, and insulation for wires.
Lubricants: This fluorocarbon compound’s low friction makes it slippery. Thus, PTFE enhances the smooth operation of machinery and reduces weathering away of parts and components.
PTFE’s strong point lies in its versatility in a plethora of applications. This fluoro compound is an indispensable factor for chemical flow and mechanical engineering. They have the following advantages:
The similarities can be attributed to their family of fluorocarbons, where RPTFE is just a reinforced variant of virgin PTFE. While their similarities are susceptible to change through different reinforcing substituents, there are quite a few broad similarities. They are mentioned below:
Resistance to corrosivity: Aggressive fluid movement is expected in valve manufacturing industries. There are several instances when devices that measure the fluid levels are exposed to corrosivity and cause deterioration. Especially in viscous and aggressive fluids, a lot of product build-up can easily corrode the substance. Both PTFE and its reinforced variant offer excellent resistance to such corrosion, and their coating can prevent this to a substantial extent. PTFE temperature resistance makes it second to none.
Hydrophobic properties: While reinforcing material keeps varying, the fundamental ability of a PTFE to act against water and water-based solvents remains. Such hydrophobic characteristics make them anti-contaminated and serve as lubricants in engineering sectors. In areas where aggressive solvents condense the antenna of the level-measuring device, this property is a savior. When made with these fluorocarbons, the measurement will remain accurate and reduce the build-up.
Teflon branding: Teflon widely refers to PTFE products but is an umbrella term for the three main fluorocarbons- PTFE, PFA, FEP, and RPTFE. All products made of PTFE and PFA materials are identified under the branding Teflon, invented by DuPont Co.
While both PTFE and reinforced PTFE are crucial fluoropolymers in the manufacturing sector that come from the same form, they have a plethora of differences and applications. The notable differences are mentioned below:
Definition: PTFE stands for polytetrafluoroethylene, while RPTFE adds additional fillings or ‘reinforcements.’ As far as the foundation is concerned, RPTFE is derived from PTFE and has many similarities. However, the existence of reinforcements alters specific grounds like chemical and thermal resistance, wear properties, and electrical conductivity.
Strength superiority: RPTFE is a superior alternative to virgin PTFE which can be attributed to the number of reinforcements. This strength is not limited just to deformation but also thermal, chemical, and electrical resistance. PTFE films and sheets exhibit weaker tensile strength.
Structural differences: While PTFE consists of nothing more than just fluorine and carbon bonding, RPTFE consists of reinforcing materials that are not just limited to polytetrafluoroethylene units. The most common reinforcement is the glass fibers, mixed with a tiny amount of graphite for friction. The PTFE valve seat is mostly white, while the RPTFE valve seat is chalky white.
In fact, PTFE’s properties are heavily attributed to the compositional structure. It is made of helical linear bonds between fluorine and carbon atoms, where the chain is secured by the fluorine atoms. RPTFE, however, has atoms of different fillings protecting the chain.
Reactivity: PTFE is inert and non-reactive to alkalis and other aggressive substances. This is attributed to their negative fluorine atoms and pure structure. However, RPTFE can induce some reactions due to reinforcing materials.
While RPTFE may seem like a derivative of PTFE, it has several additional properties that can be altered with filling materials. PTFE has outstanding cost-beneficial advantages and flexibility in the application; however, it lacks sturdiness under load pressure and is susceptible to deformation.
PTFE is highly regarded as the king of all fluoroplastics. This thermoplastic has outstanding capabilities that are indispensable in the industries mentioned. It has left its mark on a high stance in sectors like pharmaceutical, medical, aerospace, mechanical engineering, and even domestic households. If you are interested in PTFE and RPTFE-based projects, contact us to get a wide range of quality PTFE components and learn more about our excellent services!
Bellows Mechanical Seal are a type of mechanical seal where the spring element is a bellows. They are a critical component in preventing fluid or gas
In the world of engineering and manufacturing, where precision and efficiency are paramount, the role of wear resistance plastic has evolved far beyond their conventional image.
PTFE is a versatile polymer with outstanding properties like chemical resistance, low friction coefficient (self-lubricating), non-stick nature, and excellent electrical insulation. However, it also has some