Since the invention of airplanes more than a century ago, aircraft assembly for planes has developed from its most basic form to advanced production, where almost half of the aircraft is made with plastics.
Plastic is one material of the future in the aircraft sector. There are more and more interior parts of airplanes that are constructed of plastic. But plastic is also being used in a variety of other applications. Let’s explore all the obvious and unexpected places where aerospace plastics can be used.
Aerospace Parts Design Considerations
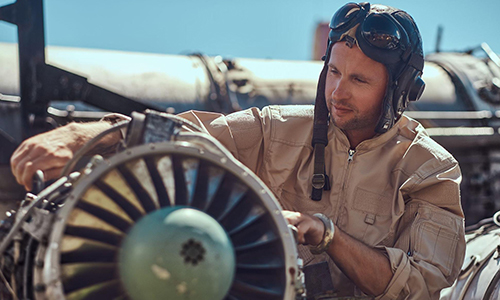
Since the choice of aerospace materials influences many aspects of aircraft performance, from the design stage to disposal, it is important to understand the aerospace parts’ design considerations.
Operating Conditions
The operating conditions of an aircraft play an important role in selecting the material for manufacturing its parts. We already know that an aircraft is subject to radiation, pressurized water and steam, and extreme temperatures.
Even though metal can withstand high temperatures and pressures, manufacturers are turning to thermoplastic for the aircraft’s exterior because of their high resistance powers.
Part’s Design and Shape
An airplane has multiple parts that are different in shape and design for their functionality. Plastic has helped solve this issue as well because it can be easily molded into any shape through the injection molding process. Additionally, plastic is readily available
Engineers are now able to create ground-breaking airplane designs that are not only more ergonomic but also more aesthetically pleasing because of the invention of airplane plastics.
Having “plastic-friendly” part geometries that minimize stress concentrations is important when designing with plastics. In contrast to flat-head screws and sharp corners, where stress concentrations can result in cracking problems, fasteners that disperse stress and internal corners with wide radii typically produce better outcomes. If an application involves temperature cycling, vibration, or the use of corrosive chemicals, cracking issues may become even worse.
Compared to traditional aircraft materials like rubber and aluminum, plastic is significantly simpler to mold and shape while also being much lighter and just as safe, if not safer. Future generations of aircraft will be the safest, most cheap, and most comfortable because of this design flexibility.
Tolerance Issues
Since different plastics have unique properties that can be used to transport particular aircraft parts and components, it is desirable to use a diversity of plastics for aerospace packaging. For instance, many plastics have a high level of strength and are resistant to erosive and thermal effects, which helps protect aeronautical components from damage while in transit.
Additionally, plastic aerospace packaging can be utilized to solve a number of problems associated with shipping aircraft components, including:
- Shock absorption
- Vibrations
- Magnetic Protection
- Extreme humidity and temperature
Plastic is the material of choice for the majority of aircraft manufacturing and packaging needs due to its resistance to these problems.
Flammability Requirements
Flammability testing of aircraft interiors, which evaluates the flame properties of plastics and textiles, is an essential component of any aerospace qualification program. These tests for flammability evaluate how quickly, readily, and with what effects materials used in airplane cabins burn.
Thermal Expansion
The resistance to thermal expansion of many acrylic and polycarbonate polymers is a plus. It’s essential that all of the plane’s components remain safe because aircraft are frequently exposed to extremely high temperatures. An airplane will gain additional durability without adding weight if high thermal stability aerospace polymers are used in its construction.
Quality Standards
The International Aerospace Quality Group (IAQG) established the Aerospace Standards, a set of quality standards based on ISO 9001, to ensure international uniformity and satisfy the various regulatory, safety, and reliability requirements expected by the aerospace industry.
While there are several aerospace standards in use today, each one has a specific function and is ultimately intended to uphold the dependability and quality of the products and services that constitute the aerospace industry.
Airlines today purchase airplanes that are as light as possible due to the high price of fuel and the pressure to cut ticket costs.
The Growing Role of Plastic in Aerospace
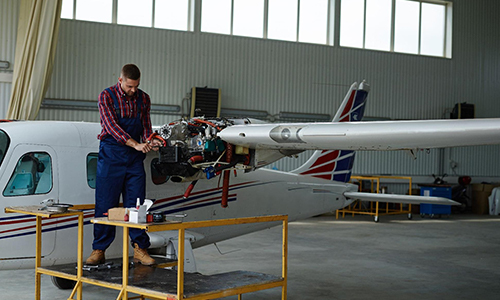
Aerospace refers to human activities in science, engineering, and commerce that include flying in Earth’s atmosphere and other astronomical bodies (astronautics). Organizations involved in the aerospace industry conduct research, develop, produce, operate, or repair aircraft. There are several commercials, industrial, and military uses for the aerospace industry.
Plastics played a significant role in the fast development of aeronautical engineering during the 20th century and into the 21st century by offering functional and practical advancements. In fact, plastic was employed so extensively in the industry that Boeing’s illustrious 787 Dreamliner earned the nickname “the plastic airplane.”
Plastic has a varied range of applications in the aerospace industry. That, coupled with its availability, simplicity in design and manufacture, it has been successful in asserting its dominance since World War II.
Although traditional plastics have been around for a while, aerospace engineers are now using them in new ways. More types of plastics are being developed every year with unique performance features that make them perfect for substituting metal components in specialized applications.
Additionally, there is an added benefit that plastics provide in improving aerodynamics because of their smooth contours. It makes plastic-made aircraft more fuel-efficient and useful. Plastics can be repaired more easily because they are lightweight and widely available.
Recent advancements in plastic technology have pushed the boundaries of what was previously possible in terms of load-bearing, torque handling, and gear-driving capabilities for aerospace applications. Plastics are able to play an ever-increasingly significant part in the aerospace sector because of specialty grades with greater thermal, chemical, and radiation resistance.
Different Types of Plastics Used in the Aerospace Industry
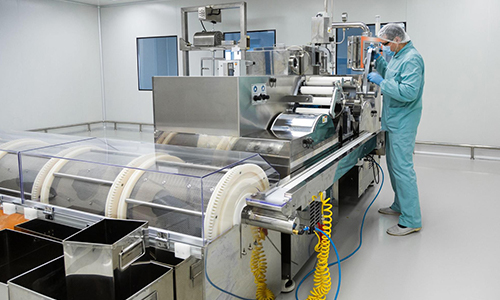
When it comes to airplanes, the aerospace industry generally uses five different types of plastic, and each of them offers a much more practical choice for airplane components.
Polytetrafluoroethylene (PTFE)
Given that it is more commonly known as Teflon, polytetrafluoroethylene (PTFE) is unquestionably the most well-known of all the polymers used in the aerospace industry. PTFE parts help connect different parts of an aircraft.
Application: Insulation is important for the myriad of cables and wires that are essential components of helicopters and airplanes and PTFE can help with that. PTFE is also an electrical insulator and a fluorocarbon polymer. It that the ability to maintain its thermal properties in aeronautical conditions. PTFE products have good tear resistance and minimal flammability.
Polychlorotrifluoroethylene (PCTFE)
This durable plastic has the adaptability to tolerate both extreme cold and intense heat. From 400 degrees Fahrenheit to 400 below, because the corrosive effects of any damage are essentially nonexistent. Additionally, it can endure fire, chemicals, and water damage to the bare minimum, making it one of the perfect materials for aerospace parts.
Application: Its characteristics make PCTFE an excellent material for parts used in external or corrosive settings. It has primarily been used in jet or aviation wings.
Polyetheretherketone (PEEK)
Companies in the aerospace industry favor polyetheretherketone (PEEK), another flexible plastic with a wide operating temperature range. Despite its ability to endure temperatures of more than 400 degrees Fahrenheit, its greatest strength might be its capacity to survive in cold temperatures or bad weather.
Application: PEEK’s mix of characteristics and wide temperature operating range make it the desired product in the aerospace industry, especially in situations where it might be subjected to low temperatures and air particles. Pump gears and valve seats are two common applications.
Polyamide-imide (PAI)
Polyamide-imide (PAI), also known as Torlon in the industry, has the potential to act as a flame retardant and can continue to be strong at temperatures as high as 500 degrees Fahrenheit. Another benefit is that it doesn’t emit any smoke as it burns. This is particularly important if there is a chance that smoke inhalation will happen or if any hazardous substances will be released into the surrounding air.
Thermosetting Polyimide
The benefit of thermosetting polyimide, also known as Meldin 7001, comes from its combination of flexibility and lightweight.
Application: It works best when components like the threaded nuts that essentially hold the plane together are properly insulated, along with the capacity to also offer great chemical resistance. Another big aspect that cannot be ignored is the spacer, whose function is to keep the wheels in the correct alignment.
Advantages of Using Plastic in the Aerospace Industry
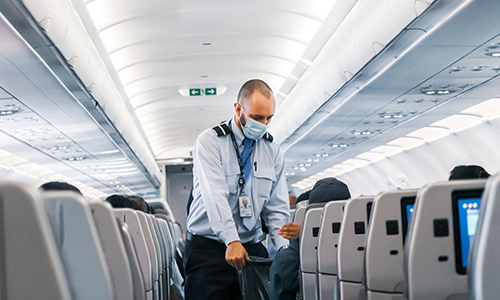
The use of plastic components in aircraft applications is growing as new kinds of high-strength, high-quality plastics and polymers are created.
Benefits at a glance
- Energy consumption can be reduced by up to 60% by using plastic instead of aluminum because plastics can be processed more easily than other materials
- Lower production and installation costs are produced by giving component designers more freedom.
- Excellent chemical resistance
- Inherent resistance to flame.
- High-performance polymers are in compliance with FAR 25.853 and UL 94-V0 fire behavior requirements.
- The density, toxicity, and heat release of smoke gasses as they relate to fire behavior.
- High specific strength because of plastics with fiber reinforcement
- Convincing gliding qualities with exceptional dry-running qualities and maintenance-free operation in the application.
- Low outgassing in an empty space.
- Good radiation resistance.
Some of the applications of plastic in the aerospace industry include:
Interior Wall Panels And Luggage Compartments
Acrylonitrile Butadiene Styrene, or ABS plastic, is frequently used to construct airplane panels and baggage compartments. This plastic can be worked into a wide range of shapes since it is well-suited for vacuum forming. It is ideal for use in airplane interior parts because of its lightweight density and robust construction.
Ducting and Seals for Ventilation
Many acrylics and polycarbonate polymers have the advantage of being thermally resistant. An airplane will gain more durability without adding weight if plastics with excellent thermal stability are used in its construction.
Doors and Fuselages for Aircraft
Plastic is now being used to build aircraft exteriors. Aircraft plastics are resistant to various types of corrosion in addition to significantly reducing the weight of the aircraft, which increases its efficiency. On top of their ability to survive both high and low temperatures, they can also withstand hydrolysis, highly pressured water and steam, and radiation.
Technical Components
The smallest parts of an airplane are made of aircraft plastics, including wiring conduits, bushings, and bearings. A major factor in the development of airplanes as a more affordable mode of transportation is the capacity to use lightweight materials for as many components of an aircraft as possible. Cheaper airfare is made possible by using less fuel, which also reduces the environmental impact of engine exhaust.
Conclusion
Besides aerospace, advancements in the plastic industry have also made it possible for several other industries, including automotive, food and beverage, mechanical engineering, etc., to manufacture precision parts while cutting down the cost. While there are many different types of plastics with unique applications, there’s no doubt that the future will bring more varieties of plastic that will revolutionize the aerospace industry.
When looking for a trustworthy business to manufacture the necessary parts for either airplanes or helicopters, look no further than Dechengwang. They design and manufacture a variety of products that are reliable and stable for their customers using high-performance fluoropolymer materials. Feel free to make a contact and get more information.